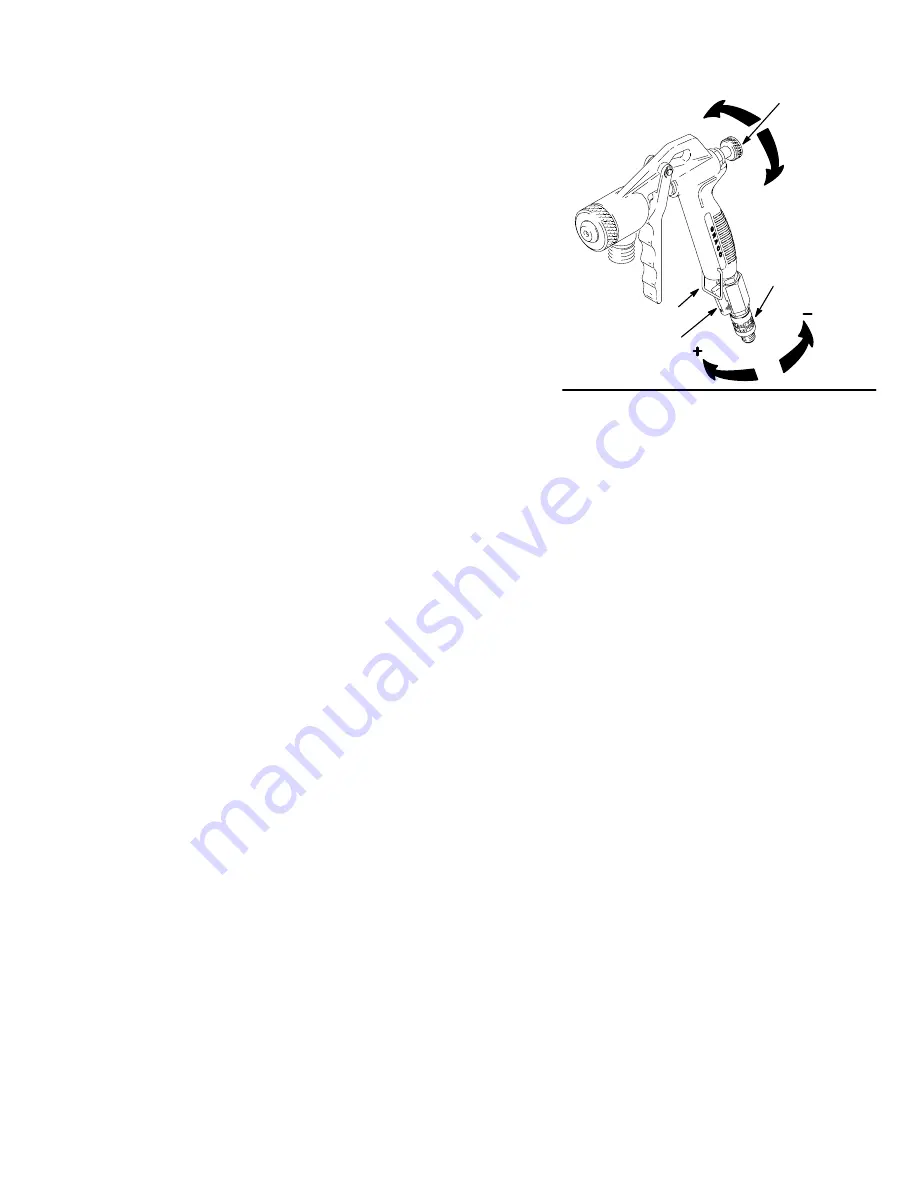
11
308–342
Spray Techniques
How to Prevent Material Surge at the
Beginning of a Spray Pattern
Squeeze the trigger slowly to the fully triggered posi-
tion while moving the gun quickly.
For Continuous Spraying
Use the trigger bail (401) to hold the trigger open to
reduce operator fatigue.
Check Material Consistency Periodically
Check and thin the material as needed to maintain the
proper consistency. The material may thicken as it sits
and slow down production or affect the spray
pattern.
0631
423
Fig. 10
418
IN
OUT
424
401