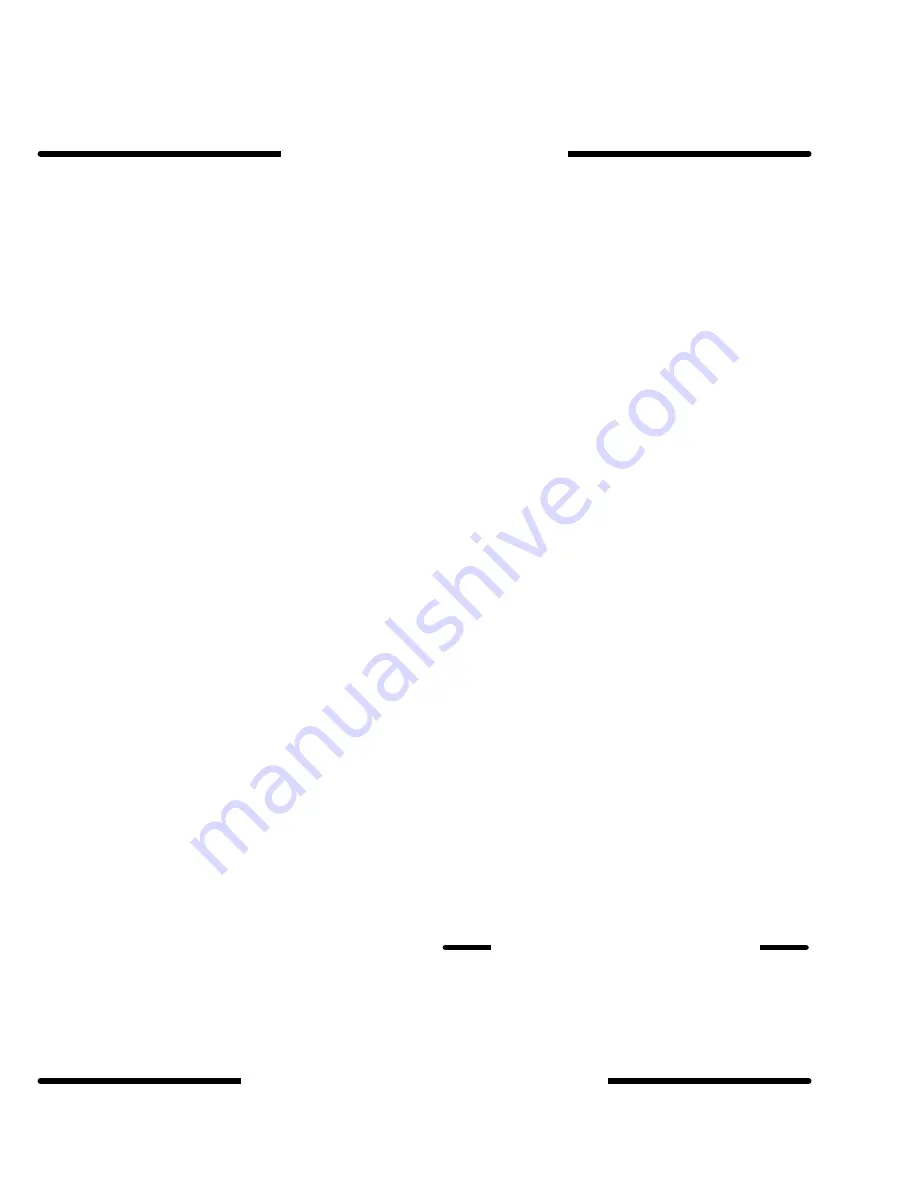
Warning
High Pressure Spray Can Cause Serious Injury. For Professional Use Only.
Observe All Warnings. Read and understand all instruction manuals before operating equipment.
FLUID INJECTION HAZARD
General Safety
This equipment generates very high fluid pressure. Spray from the
gun, leaks or ruptured components can inject fluid through your skin
and into your body and cause extremely serious bodily injury, includ-
ing the need for amputation. Also, fluid injected or splashed into the
eyes or on the skin can cause serious damage.
Never point the spray gun at anyone or at any part of the body. Never
put hand or fingers over the spray tip. Never try to “blow back” fluid;
this is not an air spray system.
Always have the tip guard in place on the spray gun when spraying.
Always follow the
Pressure Relief Procedure, right, before cleaning
or removing the spray tip or servicing any system equipment.
Never try to stop or deflect leaks with your hand or body.
Be sure equipment safety devices are operating properly before each
use.
Medical Alert––Airless Spray Wounds
If any fluid appears to penetrate your skin, get
emergency medical
care at once. Do not treat as a simple cut. Tell the doctor exactly
what fluid was injected.
NOTE TO PHYSICIAN: Injection in the skin is a traumatic injury. It is
important to treat the injury surgically as soon as possible. Do
not delay treatment to research toxicity. Toxicity is a concern with
some exotic coatings injected directly into the blood stream. Consulta-
tion with a plastic surgeon or reconstructive hand surgeon may be
advisable.
Spray Gun Safety Devices
Be sure all spray gun safety devices are operating properly before
each use. Do not remove or modify any part of the spray gun; this can
cause a malfunction and result in serious bodily injury.
Safety Latch
Whenever you stop spraying, even for a moment, always set the
safety latch in the closed or “safe” position, making the spray gun
inoperative. Failure to set the safety latch can result in accidental trig-
gering of the spray gun.
Trigger Guard
Never operate the spray gun with the trigger guard removed. This
guard helps prevent the gun from triggering accidentally if it is dropped
or bumped.
Diffuser
The spray gun diffuser breaks up spray and reduces the risk of fluid
injection when the tip is not installed. Check the diffuser operation
regularly. Follow the
Pressure Relief Procedure, at right, then re-
move the spray tip. Aim the spray gun into a grounded metal pail,
holding the spray gun firmly to the pail. Using the lowest possible pres-
sure, trigger the spray gun. If the fluid emitted is not diffused into an
irregular stream, replace the diffuser immediately.
Tip Guard
Always have the tip guard in place on the spray gun while spraying.
The tip guard alerts you to the fluid injection hazard and helps reduce,
but does not prevent, the risk of accidentally placing your fingers or
any part of your body close to the spray tip.
Spray Tip
Use extreme caution when cleaning or changing spray tips. If the
spray tip clogs while spraying, engage the safety latch immediately.
Always follow the
Pressure Relief Procedure and then remove the
spray tip to clean it.
Never wipe off build-up around the spray tip until pressure is fully re-
lieved and the safety latch is engaged.
Pressure Relief Procedure
To reduce the risk of serious bodily injury, including fluid injection,
splashing in the eyes or on the skin, or injury from moving parts, al-
ways follow this procedure whenever you shut off the pump, when
checking or servicing any part of the spray system, when installing,
cleaning or changing spray tips, and whenever you stop spraying.
1. Engage the spray gun safety latch.
2. Shut off the air or hydraulic fluid to the pump.
3. Close the bleed-type master air valve (required in air-powered
systems).
4. Disengage the spray gun safety latch.
5. Hold a metal part of the spray gun firmly to the side of a grounded
metal pail, and trigger the gun to relieve pressure.
6. Engage the spray gun safety latch.
7. Open the drain valve (required in your system), having a con-
tainer ready to catch the drainage.
8. Leave the drain valve open until you are ready to spray again.
If you suspect that the spray tip or hose is completely clogged, or that
pressure has not been fully relieved after following the steps above,
very slowly loosen the retaining nut or hose end coupling and relieve
pressure gradually, then loosen completely. Now clear the tip or hose.
MOVING PARTS HAZARD
Moving parts can pinch or amputate your fingers or other body parts.
When the pump is operating, the air motor piston (located behind the
air motor plates) moves. Therefore, never operate the pump with the
air motor plates removed. Before servicing the pump, follow the
Pres-
sure Relief Procedure above to prevent the pump from starting acci-
dentally.
PLURAL COMPONENT MATERIALS
Be extremely cautious when handling plural component materials and
solvents used with them. Some are extremely toxic. See the
WARN-
ING on the front cover. Read and follow the coating and solvent manu-
facturer’s safety precautions and warnings, including any regarding
protective clothing, eyewear, and respirator.