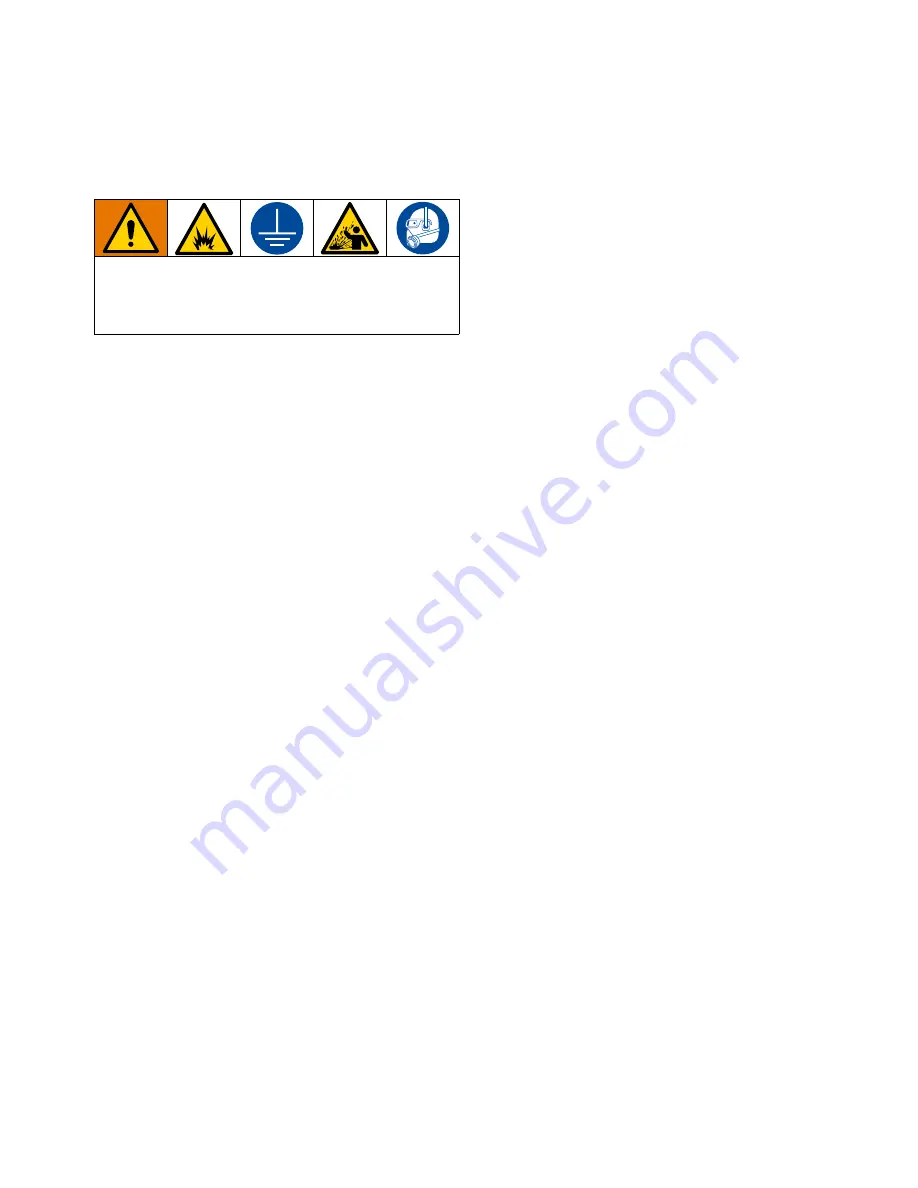
Flush the Equipment (Solvent-Based Materials)
313537E
5
Flush the Equipment
(Solvent-Based Materials)
•
Flush before changing materials, before fluid can
dry or cure in the equipment, at the end of the day,
before storing, and before repairing equipment.
•
Flush with a fluid that is compatible with the fluid
being dispensed and the equipment wetted parts.
•
Flush at the lowest pressure possible. Check con-
nectors for leaks and tighten as necessary.
•
Do not leave the applicator or any parts in water or
cleaning solvents.
1. Follow
2. Remove the spray tip and guard by loosening
retaining ring (11).
3. Hold a metal part of the gun firmly to a grounded
metal pail. Trigger the gun until clean solvent
dispenses.
4. Store in a dry location.
To avoid fire and explosion, always ground equipment
and waste container. To avoid static sparking and
injury from splashing, always flush at the lowest
possible pressure.