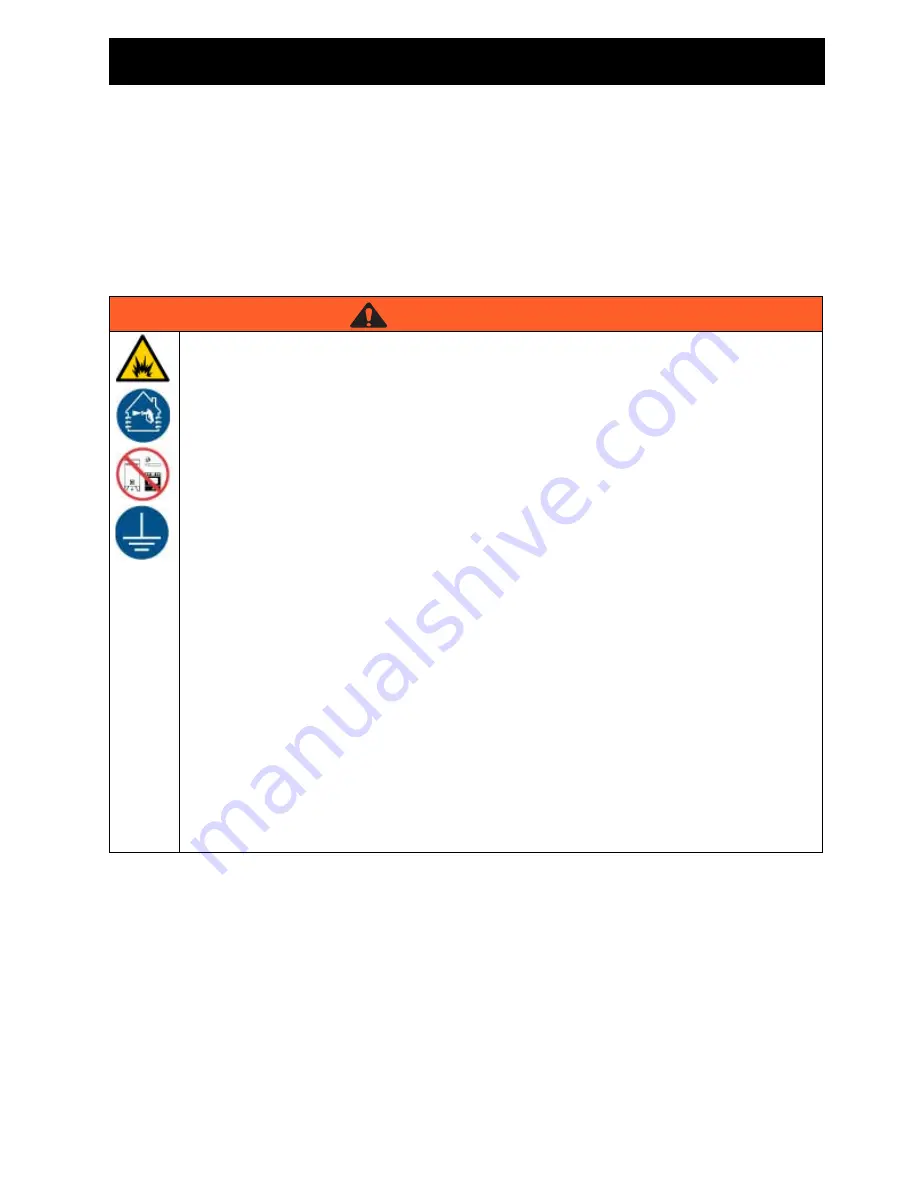
Warnings
334599F
3
Warnings
The following warnings are for the setup, use, grounding, maintenance, and repair of this
equipment. The exclamation point symbol alerts you to a general warning and the hazard
symbols refer to procedure-specific risks. When these symbols appear in the body of this
manual or on warning labels, refer back to these Warnings. Product-specific hazard symbols
and warnings not covered in this section may appear throughout the body of this manual
where applicable.
WARNING
FIRE AND EXPLOSION HAZARD
Flammable fumes, such as solvent and paint fumes, in work area can ignite or explode. To help
prevent fire and explosion:
•
Do not spray flammable or combustible materials near an open flame or sources of ignition
such as cigarettes, motors, and electrical equipment.
•
Paint or solvent flowing through the equipment is able to result in static electricity. Static
electricity creates a risk of fire or explosion in the presence of paint or solvent fumes. All
parts of the spray system, including the pump, hose assembly, spray gun, and objects in
and around the spray area shall be properly grounded to protect against static discharge
and sparks. Use Graco conductive or grounded high-pressure airless paint sprayer hoses.
•
Verify that all containers and collection systems are grounded to prevent static discharge.
Do not use pail liners unless they are anti static or conductive.
•
Connect to a grounded outlet and use grounded extensions cords. Do not use a 3-to-2
adapter.
•
Do not use a paint or a solvent containing halogenated hydrocarbons.
•
Do not spray flammable or combustible liquids in a confined area.
•
Keep spray area well-ventilated. Keep a good supply of fresh air moving through the area.
•
Sprayer generates sparks. Keep pump assembly in a well ventilated area at least 20 feet
(6.1 m) from the spray area
when spraying, flushing, cleaning, or servicing
. Do not spray
pump assembly.
•
Do not smoke in the spray area or spray where sparks or flame is present.
•
Do not operate light switches, engines, or similar spark producing products in the spray
area.
•
Keep area clean and free of paint or solvent containers, rags, and other flammable
materials.
•
Know the contents of the paints and solvents being sprayed. Read all Safety Data Sheets
(SDS) and container labels provided with the paints and solvents. Follow the paint and
solvents manufacturer’s safety instructions.
•
Fire extinguisher equipment shall be present and working.
Summary of Contents for 17C487
Page 20: ...Notes 20 334599F Notes...
Page 21: ...Notes 334599F 21 Notes...