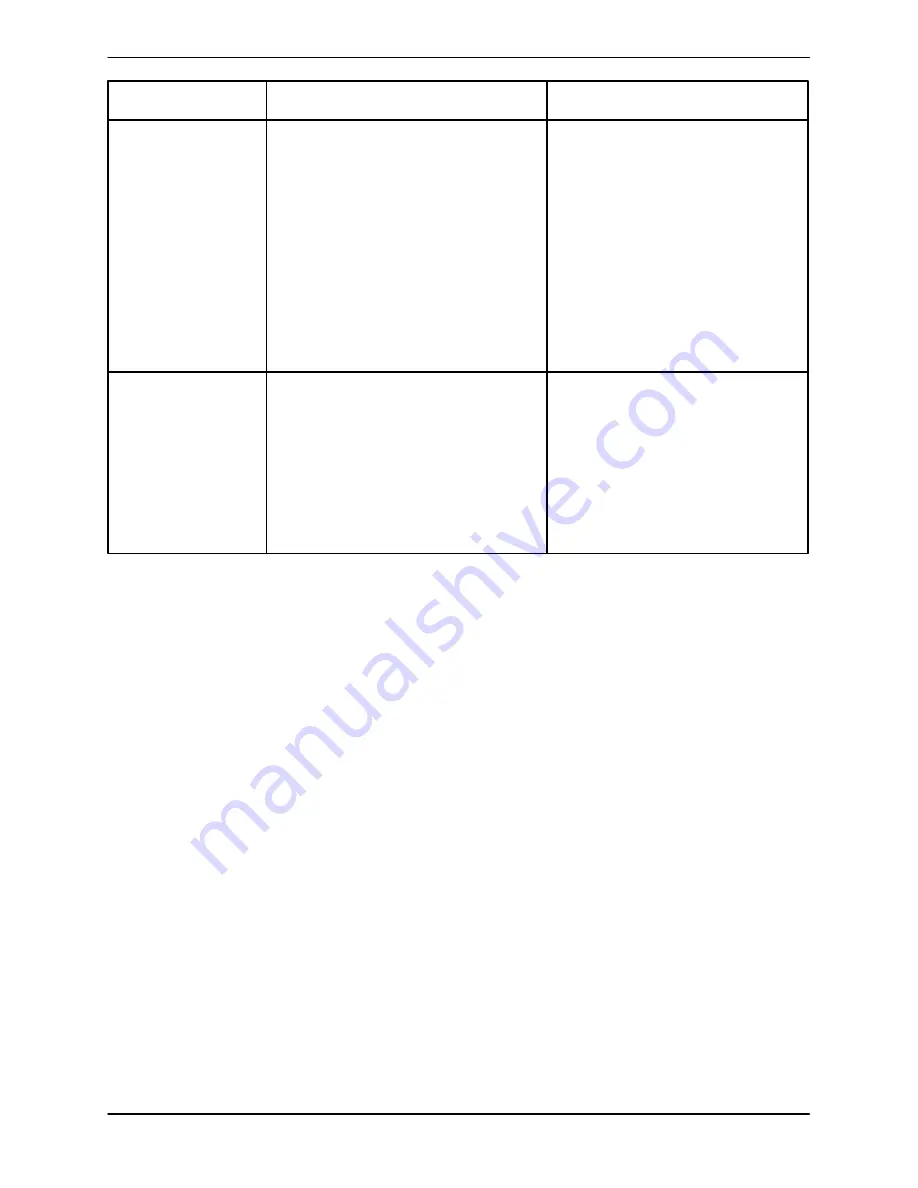
SUPER T SERIES
OM−05267
TROUBLESHOOTING
PAGE D − 3
TROUBLE
POSSIBLE CAUSE
PROBABLE REMEDY
BEARINGS RUN
TOO HOT
Bearing temperature is high, but
within limits.
Check bearing temperature regu-
larly to monitor any increase.
Low or incorrect lubricant.
Check for proper type and level of
lubricant.
Suction and discharge lines not
properly supported.
Check piping installation for
proper support.
Drive misaligned.
Align drive properly.
EXCESSIVE NOISE
Cavitation in pump.
Impeller clogged or damaged.
Pump or drive not securely mounted.
Pumping entrained air.
Reduce suction lift and/or friction
losses in suction line. Record vac-
uum and pressure gauge readings
and consult local representative or
factory.
Locate and eliminate source of air
bubble.
Secure mounting hardware.
Clean out debris; replace dam-
aged parts.
PREVENTIVE MAINTENANCE
Since pump applications are seldom identical, and
pump wear is directly affected by such things as
the abrasive qualities, pressure and temperature
of the liquid being pumped, this section is intended
only to provide general recommendations and
practices for preventive maintenance. Regardless
of the application however, following a routine pre-
ventive maintenance schedule will help assure
trouble-free performance and long life from your
Gorman-Rupp pump. For specific questions con-
cerning your application, contact your Gorman-
Rupp distributor or the Gorman-Rupp Company.
Record keeping is an essential component of a
good preventive maintenance program. Changes
in suction and discharge gauge readings (if so
equipped) between regularly scheduled inspec-
tions can indicate problems that can be corrected
before system damage or catastrophic failure oc-
curs. The appearance of wearing parts should also
be documented at each inspection for comparison
as well. Also, if records indicate that a certain part
(such as the seal) fails at approximately the same
duty cycle, the part can be checked and replaced
before failure occurs, reducing unscheduled down
time.
For new applications, a first inspection of wearing
parts at 250 hours will give insight into the wear rate
for your particular application. Subsequent inspec-
tions should be performed at the intervals shown
on the chart below. Critical applications should be
inspected more frequently.