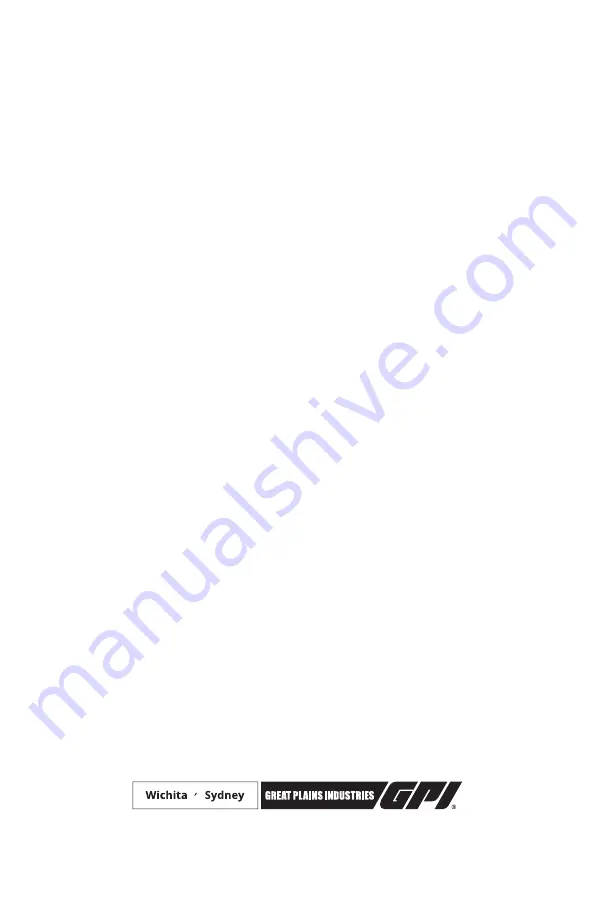
© 2020 Great Plains Industries, Inc., All Rights Reserved.
Great Plains Industries, Inc. / 800-835-0113 / GPI.net
11
/2020
GPI
®
TWO
-YEAR LIMITED WARRANTY
Great Plains Industries, Inc. 5252 E. 36th Street North, Wichita, KS USA 67220-3205,
hereby provides a limited warranty against defects in material and workmanship on all
products manufactured by Great Plains Industries, Inc. This product includes a
2
year
warranty from date of purchase as evidenced by the original sales receipt. A
30
month
warranty from product date of manufacture will apply in cases where the original sales
receipt is not available. Reference product labeling for the warranty expiration date based
on
30
months from date of manufacture. Manufacturer’s sole obligation under the
foregoing warranties will be limited to either, at manufacturer’s option, replacing or
repairing defective goods (subject to limitations hereinafter provided) or refunding the
purchase price for such goods theretofore paid by the buyer, and buyer’s exclusive remedy
for breach of any such warranties will be enforcement of such obligations of manufacturer.
The warranty shall extend to the purchaser of this product and to any person to whom such
product is transferred during the warranty period. This warranty shall not apply if:
A. the product has been altered or modified outside the warrantor’s duly appointed
representative;
B. the product has been subjected to neglect, misuse, abuse or damage or has been
installed or operated other than in accordance with the manufacturer’s operating
instructions.
To make a claim against this warranty, contact the GPI Customer Service Department at
316-686-7361 or 800-835-0113.
Or by mail at:
Great Plains Industries, Inc.
5252 E. 36th St. North
Wichita, KS, USA 67220-3205
The company will guide you through a product troubleshooting process to determine
appropriate corrective actions.
GREAT PLAINS INDUSTRIES, INC., EXCLUDES LIABILITY UNDER THIS WARRANTY
FOR DIRECT, INDIRECT, INCIDENTAL AND CONSEQUENTIAL DAMAGES INCURRED
IN THE USE OR LOSS OF USE OF THE PRODUCT WARRANTED HEREUNDER.
The company herewith expressly disclaims any warranty of merchantability or fitness for
any particular purpose other than for which it was designed.
This warranty gives you specific rights and you may also have
other rights which vary from U.S. state to U.S. state.
Note: In compliance with MAGNUSON-MOSS CONSUMER WARRANTY ACT –
Part 702 (governs the resale availability of the warranty terms).
92
1487
-
09
Rev
E
per ECN
5821