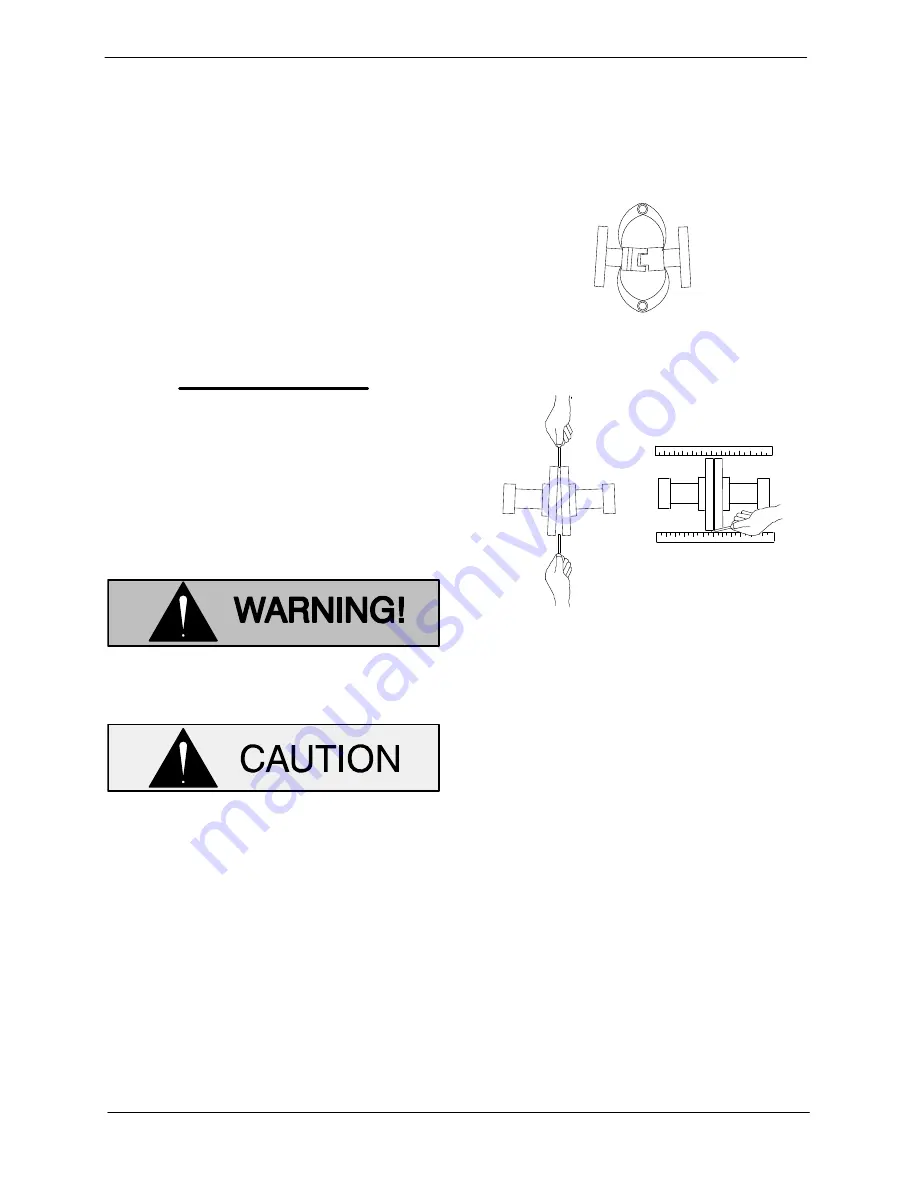
80 SERIES
OM−00974
PAGE B − 5
INSTALLATION
ALIGNMENT
The alignment of the pump and its power source is
critical for trouble-free mechanical operation. In
either a flexible coupling or V-belt driven system,
the driver and pump must be mounted so that their
shafts are aligned with and parallel to each other. It
is imperative that alignment be checked after the
pump and piping are installed, and before opera-
tion.
NOTE
Check
Rotation
, Section C, before final alignment
of the pump.
When mounted at the Gorman-Rupp factory, driver
and pump are aligned before shipment. Misalign-
ment will occur in transit and handling. Pumps
must
be checked and realigned before operation.
Before checking alignment, tighten the foundation
bolts. The pump casing feet and/or pedestal feet,
and the driver mounting bolts should also be tightly
secured.
When checking alignment, disconnect
the power source to ensure that the
pump will remain inoperative.
Adjusting the alignment in one direction
may alter the alignment in another direc-
tion. check each procedure after altering
alignment.
Coupled Drives
When using couplings, the axis of the power
source must be aligned to the axis of the pump
shaft in both the horizontal and vertical planes.
Most couplings require a specific gap or clearance
between the driving and the driven shafts. Refer to
the coupling manufacturer’s service literature.
Align spider insert type couplings by using calipers
to measure the dimensions on the circumference
of the outer ends of the coupling hub every 90 de-
grees. The coupling is in alignment when the hub
ends are the same distance apart at all points (see
Figure 3A).
Figure 3A. Aligning Spider Type Couplings
Figure 3B. Aligning Non-Spider Type
Couplings
Align non-spider type couplings by using a feeler
gauge or taper gauge between the coupling halves
every 90 degrees. The coupling is in alignment
when the hubs are the same distance apart at all
points (see Figure 3B).
Check parallel adjustment by laying a straightedge
across both coupling rims at the top, bottom, and
side. When the straightedge rests evenly on both
halves of the coupling, the coupling is in horizontal
parallel alignment. If the coupling is misaligned,
use a feeler gauge between the coupling and the
straightedge to measure the amount of misalign-
ment.
V-Belt Drives
When using V-belt drives, the power source and
the pump must be parallel. Use a straightedge
along the sides of the pulleys to ensure that the pul-
leys are properly aligned (see Figure 3C). In drive
systems using two or more belts, make certain that