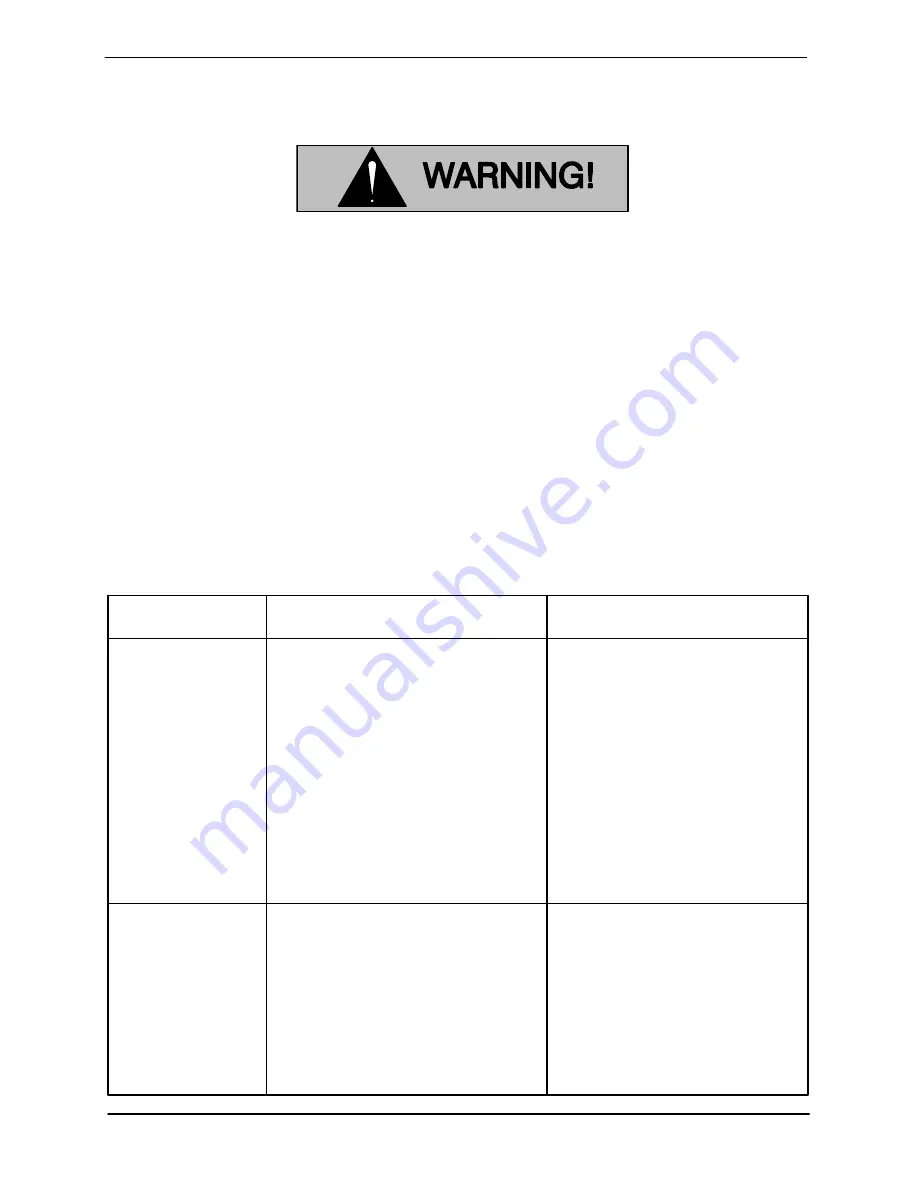
OM−00877
80 SERIES
TROUBLESHOOTING
PAGE D − 1
TROUBLESHOOTING − SECTION D
Review all SAFETY information in Section A.
Before attempting to open or service the
pump:
1. Familiarize yourself with this man-
ual.
2. Lock out or disconnect the power
source to ensure that the pump
will remain inoperative.
3. Allow the pump to completely cool
if overheated.
4. Check the temperature before
opening any covers, plates, or
plugs.
5. Close the suction and discharge
valves.
6. Vent the pump slowly and cau-
tiously.
7. Drain the pump.
TROUBLE
POSSIBLE CAUSE
PROBABLE REMEDY
PUMP FAILS TO
PRIME
Suction check valve contaminated or
damaged.
Clean or replace check valve.
Air leak in suction line.
Lining of suction hose collapsed.
Correct leak.
Replace suction hose.
Leaking or worn seal or pump gasket.
Check pump vacuum. Replace
leaking or worn seal or gasket.
Suction lift or discharge head too high.
Check piping installation and in-
stall bypass line if needed. See
INSTALLATION
.
Strainer clogged.
Check strainer and clean if neces-
sary.
Not enough liquid in casing.
Add liquid to casing. See
PRIMING
.
PUMP STOPS OR
FAILS TO DELIVER
RATED FLOW OR
PRESSURE
Air leak in suction line.
Lining of suction hose collapsed.
Correct leak.
Replace suction hose.
Leaking or worn seal or pump gasket.
Check pump vacuum. Replace
leaking or worn seal or gasket.
Strainer clogged.
Check strainer and clean if neces-
sary.
Suction intake not submerged at
proper level or sump too small.
Check installation and correct sub-
mergence as needed.