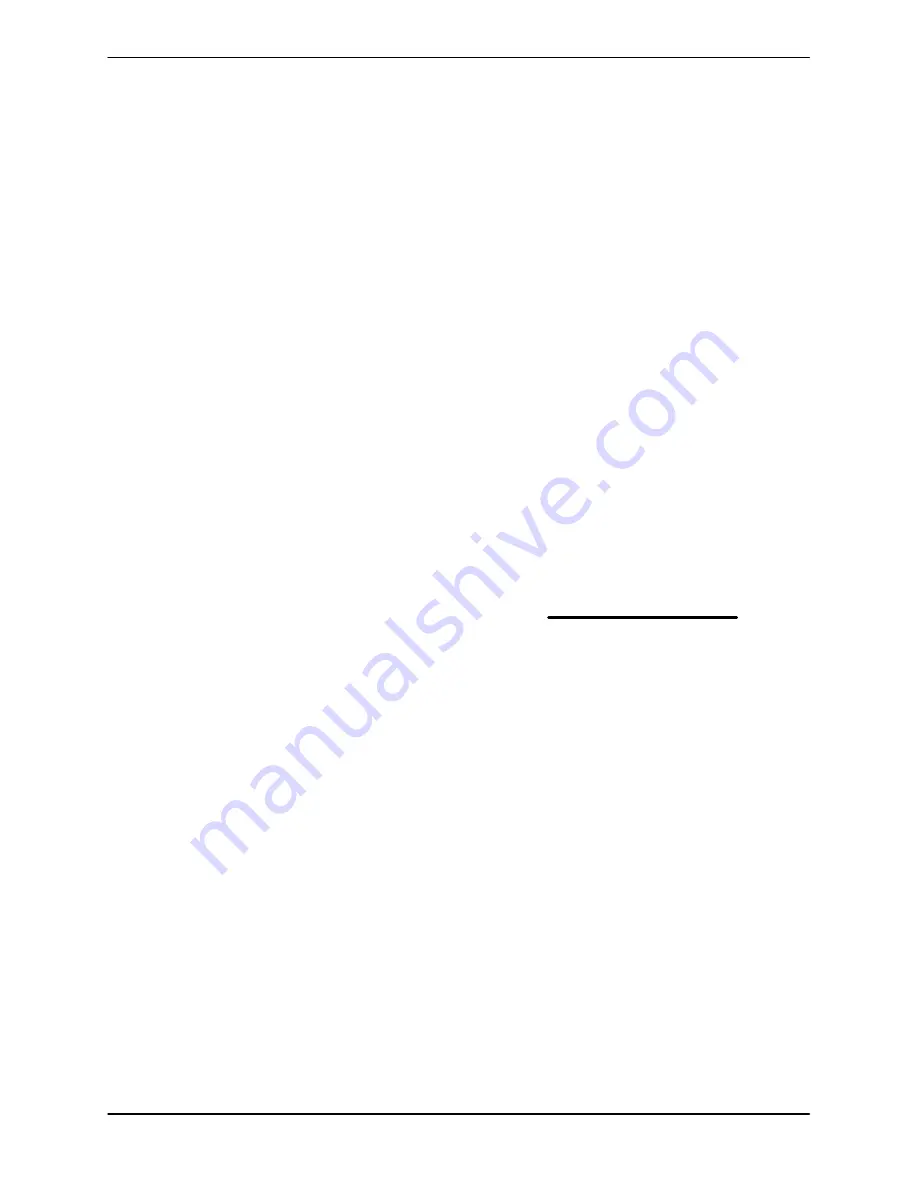
OM-07454
10 SERIES
MAINTENANCE & REPAIR
PAGE E - 9
the sealing face lightly in a concentric pattern with
a clean, lint‐free tissue.
Position the intermediate and stationary subas
sembly over the shaft and against the engine. Se
cure the intermediate to the engine with the hard
ware (5 and 6).
Slide the rotating subassembly (consisting of the
element, bellows and retainer) over the lubricated
shaft sleeve until the rotating element is
just
flush
with the chamfered end of the sleeve. Slide the
sleeve over the shaft until the sealing faces con
tact. Continue to press the shaft sleeve through the
seal assembly until it seats squarely against the
shaft shoulder.
Install the seal spring and spring retainer (11).
Impeller Installation And Adjustment
(Figure 2)
Inspect the impeller, and replace it if cracked or
badly worn. Install the same thickness of impeller
shims (12) as previously removed and screw the
impeller onto the shaft until tight.
A clearance of .015 to .040 inch (0,38 to 1,02 mm)
between the impeller and the intermediate is nec
essary for maximum pump efficiency. Measure this
clearance and add or remove impeller shims until
this clearance is reached.
Pump Casing Installation
(Figure 2)
Install the same thickness of pump casing gaskets
(14) as previously removed and secure the pump
casing (1) to the intermediate (9) with the nuts (7).
Do not
fully tighten the nuts at this time.
A clearance of .010 to .020 inch (0,25 to 0,51 mm)
between the impeller and the wear plate is also rec
ommended for maximum pump efficiency. This
clearance must be set after installing the back cov
er by adding or removing pump casing gaskets un
til the impeller scrapes against the wear plate when
the shaft is turned. After the impeller scrapes, add
approximately .010 inch (0,25 mm) of gaskets.
After the face clearance has been set, tighten the
nuts (7) securing the pump casing to the intermedi
ate.
See Figure 1 and secure the pump casing to the
base (6) with the hardware (15,16,17). Be sure to
reinstall any leveling shims used under the mount
ing feet of the pump casing.
Back Cover Installation
(Figure 2)
Inspect the wear plate (15) and replace it if badly
worn or grooved. Carefully center the wear plate on
the back cover (25) and secure it with the hardware
(21 and 22). The wear plate must be concentric to
prevent binding when the back cover is installed.
Clean any scale or debris from the back cover
shoulder and pump casing which might prevent a
good seal.
NOTE
Apply a film of `Never‐Seez' or equivalent com
pound on the back cover shoulder or any surface
which contacts the pump casing to ease future dis
assembly and to reduce rust and scale build up.
Replace the back cover gasket (20) and slide the
back cover assembly into the pump casing. Be
sure the wear plate does not bind against the
pump casing.
Secure the back cover assembly using the hard
ware (23 and 24).
Do not
over tighten the wing
nuts; they should be just tight enough to ensure a
good seal at the back cover shoulder.
Suction Check Valve Installation
(Figure 2)
Inspect the check valve components and replace
as required. Assemble the check valve weights to
each side of the check valve and secure with the
previously removed hardware.
Position the check valve assembly (27) in the suc
tion port with the large weight toward the impeller
and the small weight toward the suction flange. In
stall the suction flange (26) and secure it with the
nuts (7). Check the operation of the check valve to
ensure proper seating and free movement.