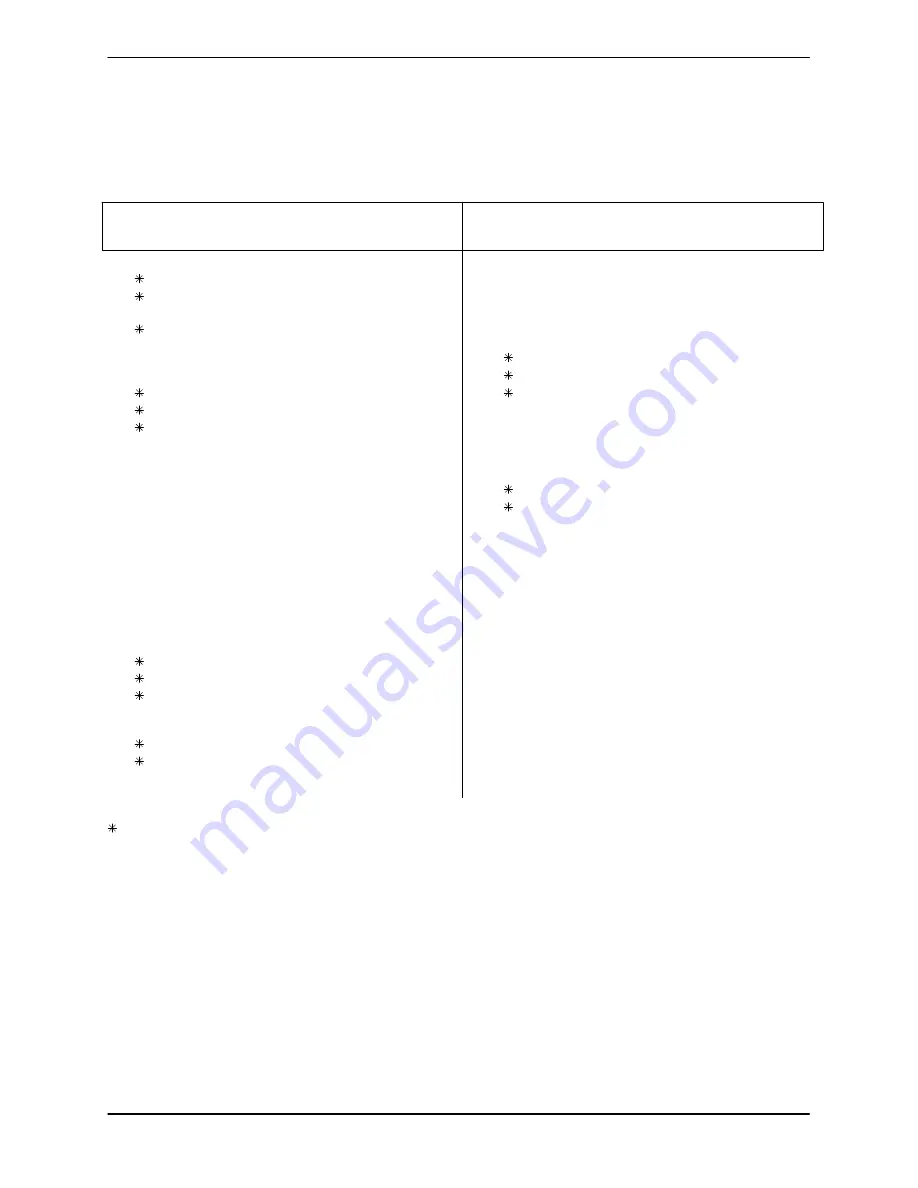
ITEM
NO.
PART NAME
PART
NUMBER
MAT'L
CODE
QTY
ITEM
NO.
PART NAME
PART
NUMBER
MAT'L
CODE
QTY
OM-02816
VG SERIES
MAINTENANCE & REPAIR
PAGE E - 3
PARTS LIST
Pump Model VG5C3-B
(From S/N 1188885 up)
If your pump serial number is followed by an “N”, your pump is
NOT
a standard production model. Contact
the Gorman‐Rupp Company to verify part numbers.
1
PUMP CASING
26821-745
---
1
2
IMPELLER
26821-108
---
1
3
SEAL ASSY
25271-095
---
1
4
DISCHARGE STICKER
6588BJ
---
1
5
SEAL PLATE GSKT
26821-426
---
1
6
SEAL PLATE
26821-691
---
1
7
SETSCREW
26821-942
---
2
8
SEAL COLLAR
26821-034
---
1
9
SHAFT SLEEVE O-RING 25154-132
---
1
10
SHAFT SLEEVE
26821-224
---
1
11
SEAL CAP GSKT
26821-463
---
1
12
HEX NUT
26821-934
---
16
13
STUD
26821-892
---
16
14
STUD
26821-890
---
6
15
HEX NUT
26821-933
---
6
16
NAME PLATE
38814-043
13990
1
17
DRIVE SCREW
BM#04-03
17000
2
18
HEX HD CAPSCREW
22645-162
---
4
19
BEARING CAP
26821-074
---
1
20
BEARING HOUSING
26821-068
---
1
21
BEARING SPACER
26821-321
---
1
22
RETAINING RING
26821-384
---
1
23
ROTATION DECAL
2613M
---
1
24
LUBE DECAL
38816-079
---
1
25
OIL INLET PLUG
26821-616
---
1
26
OUTBRD BALL BRG
23275-012
---
1
27
BRG CAP GSKT
26821-404
---
1
28
OUTBRD OIL SEAL
26821-634
---
1
29
HEX HD CAPSCREW
22645-162
---
4
30
BEARING CAP
26821-074
---
1
31
SHAFT KEY
N0814
15990
1
32
REPAIR IMP SHAFT
26821-174
---
1
-INCLUDES ITEMS 31, 48 AND 49
33
HEX HD CAPSCREW
22645-162
---
2
34
FLAT WASHER
K06
15991
2
35
FOOT
26821-208
---
1
36
BEARING SPACER
26821-321
---
1
37
BRG RETAINER RING
26821-384
---
1
38
OIL LEVEL
26821-611
---
1
39
PIPE PLUG
P06
15079
1
40
INBRD BALL BRG
S1033
---
1
41
BRG CAP GSKT
26821-404
---
1
42
INBRD OIL SEAL
26821-634
---
1
43
DEFLECTOR
26821-494
---
1
44
HEX NUT
26821-932
---
4
45
STUD
26821-880
---
4
46
SEAL CAP
26821-244
---
1
47
PIPE PLUG
P08
15079
1
48
IMPELLER NUT
26821-135
---
1
49
IMPELLER KEY
26821-264
---
1
50
SUCTION STICKER
6588AG
---
1
51
PIPE PLUG
P08
15079
1
NOT SHOWN:
INSTRUCTION TAG
38817-011
---
1
INSTRUCTION TAG
38817-024
---
1
OPTIONAL:
NPT SUCTION FLANGE
1758
10010
1
SUCT FLANGE GSKT
1679G
18000
1
NPT DISCHARGE FLANGE 1757
10010
1
DISCH FLANGE GSKT
1678G
18000
1
STRAINER, STD
S2278
---
1
STRAINER, IRRIGATION
S1529
---
1
DISCH CHECK VLV ASSY GRP14-02A ---
1
HAND PRIMER
GRP43-09
---
1
VITON SEAL
25271-096
---
1
BRONZE IMPELLER
26821-088
---
1
INDICATES PARTS RECOMMENDED FOR STOCK