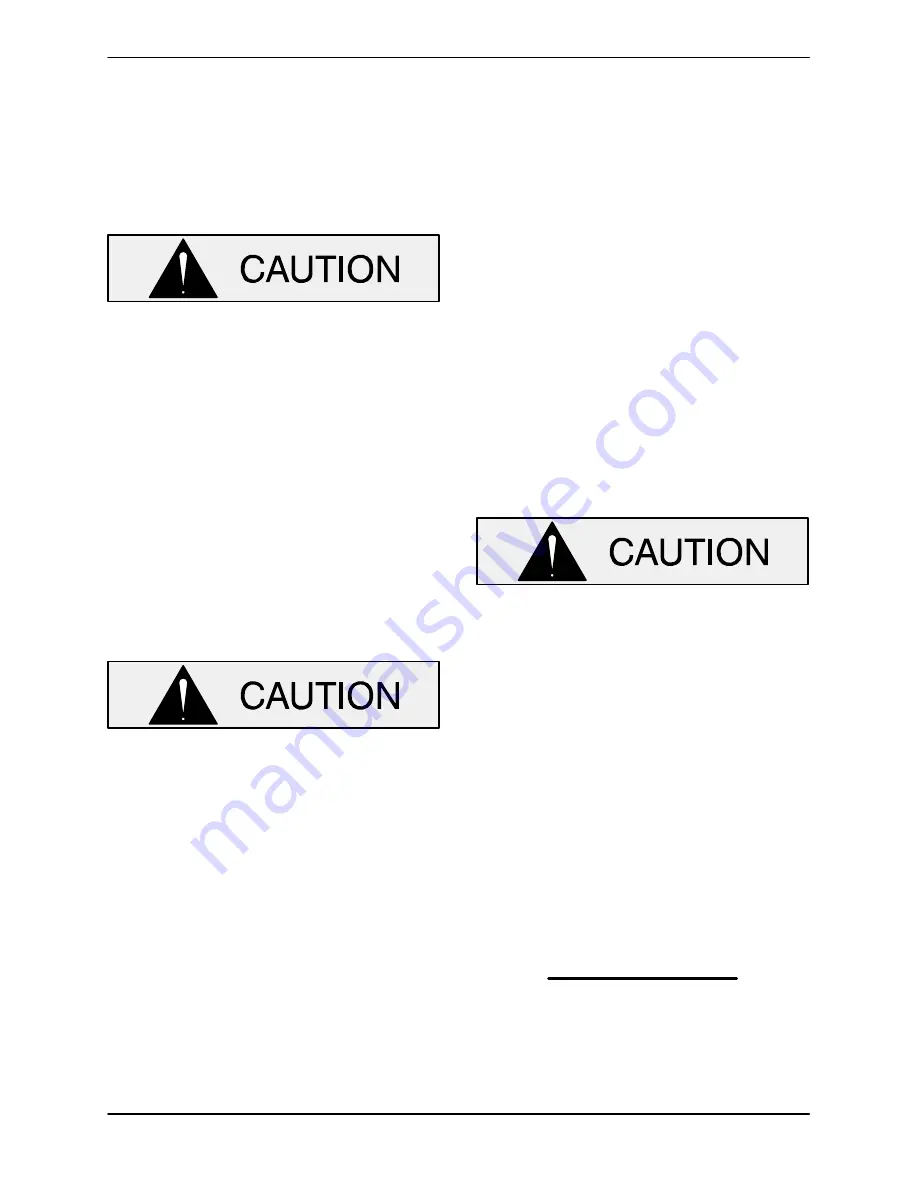
OM-05816
ULTRA V SERIES
MAINTENANCE & REPAIR
PAGE E - 13
proper clearance as described in
Impeller Instal
lation and Adjustment
.
If necessary to reuse an
old seal
in an emer
gency, carefully separate the rotating and station
ary seal faces from the bellows retainer and sta
tionary seat.
A new seal assembly should be installed
any time
the old seal is removed from the
pump. Wear patterns on the finished faces
cannot be realigned during reassembly.
Reusing an old seal could result in prema
ture failure.
Handle the seal parts with extreme care to prevent
damage. Be careful not to contaminate precision
finished faces; even fingerprints on the faces can
shorten seal life. If necessary, clean the faces with a
non‐oil based solvent and a clean, lint‐free tissue.
Wipe
lightly
in a concentric pattern to avoid
scratching the faces.
Carefully
wash all metallic parts in fresh cleaning
solvent and allow to dry thoroughly.
Do not
attempt to separate the rotating
portion of the seal from the shaft sleeve
when reusing an old seal. The rubber bel
lows will adhere to the sleeve during use,
and attempting to separate them could
damage the bellows.
Inspect the seal components for wear, scoring,
grooves, and other damage that might cause leak
age. Inspect the integral shaft sleeve for nicks or
cuts on either end. If any components are worn, or
the sleeve is damaged, replace the complete seal;
never mix old and new seal parts
.
Install the stationary seal element in the stationary
seat. Press this stationary subassembly into the
seal plate bore until it seats squarely against the
bore shoulder. A push tube made from a piece of
plastic pipe would aid this installation. The I.D. of
the pipe should be slightly larger than the O.D. of
the shaft sleeve.
Slide the rotating portion of the seal (consisting of
the integral shaft sleeve, spring centering washer,
spring, bellows and retainer, and rotating element)
onto the shaft until the seal faces contact.
Proceed with
Impeller Installation and Adjust
ment
.
Impeller Installation And Adjustment
(Figure 2)
Inspect the impeller, and replace it if cracked or
badly worn. Inspect the impeller and shaft threads
for dirt or damage, and clean or dress the threads
as required.
The shaft and impeller threads
must
be
completely clean before reinstalling the im
peller. Even the slightest amount of dirt on
the threads can cause the impeller to seize
to the shaft, making future removal difficult
or impossible without damage to the im
peller or shaft.
Install the same thickness of impeller adjusting
shims (2) as previously removed. Apply anti-
seize (G‐R P/N 18685-031) to threads. Install and
fully tighten impeller prior to installing impeller
washer and capscrew.
NOTE
At the slightest sign of binding, immediately back
the impeller off, and check the threads for dirt.
Do
not
try to force the impeller onto the shaft
.
A clearance of .025 to .040 inch (0,64 to 1,02 mm)
between the impeller and the seal plate is recom
mended for maximum pump efficiency. Measure
this clearance, and add or remove impeller adjust
ing shims as required.