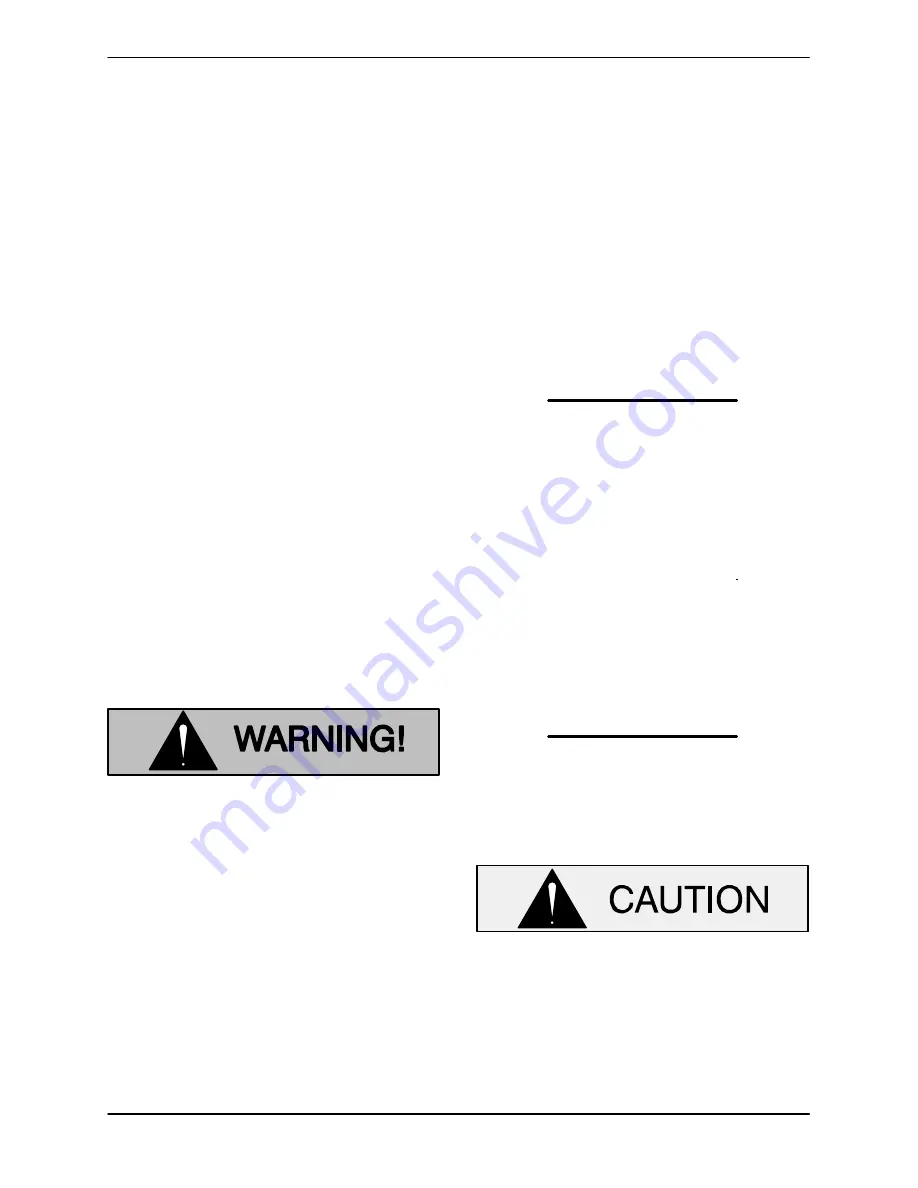
OM-05668
SUPER U SERIES
MAINTENANCE & REPAIR
PAGE E - 16
PRESSURE RELIEF VALVE
MAINTENANCE
(Figure 1)
The back cover is equipped with a pressure relief
valve (45) to provide additional safety for the pump
and operator (refer to
Liquid Temperature And
Overheating
in
OPERATION
).
It is recommended that the pressure relief valve as
sembly be replaced at each overhaul, or any time
the pump overheats and activates the valve.
Never
replace this valve with a substitute which has not
been specified or provided by the Gorman‐Rupp
Company.
Periodically, the valve should be removed for in
spection and cleaning. When reinstalling the relief
valve, apply `Loctite Pipe Sealant With Teflon No.
592', or equivalent compound, on the relief valve
threads. Position the valve as shown in Figure 1
with the discharge port pointing down.
Final Pump Assembly
(Figure 1)
Install the shaft key (19, Figure 2) and reconnect
the power source. Be sure to install any guards
used over the rotating members.
Do not operate the pump without
the
guards in place over the rotating parts.
Exposed rotating parts can catch cloth
ing, fingers, or tools, causing severe in
jury to personnel.
Install the suction and discharge lines and open all
valves. Make certain that all piping connections are
tight, properly supported and secure.
Be sure
the pump and power source have been
properly lubricated, see
LUBRICATION
.
Remove the fill cover assembly (16) and fill the
pump casing with clean liquid. Reinstall the fill
cover and tighten it. Refer to
OPERATION
, Section
C, before putting the pump back into service.
LUBRICATION
Seal Assembly
(Figure 2)
Check the oil level regularly through the sight
gauge (20)
and maintain it at the middle of the
gauge. When lubrication is required, add SAE No.
30 non‐detergent oil through the hole for the
vented plug (11). Clean and reinstall the vented
plug. Maintain the oil at this level.
NOTE
The white reflector in the sight gauge must be posi
tioned horizontally to provide proper drainage.
Bearings
(Figure 2)
The bearing housing was fully lubricated when
shipped from the factory. Check the oil level regu
larly through the sight gauge (21)
and maintain it at
the middle of the gauge. When lubrication is re
quired, add SAE No. 30 non‐detergent
oil through
the hole for the air vent (13).
Do not
over‐lubricate.
Over‐lubrication can cause the bearings to over‐
heat, resulting in premature bearing failure.
NOTE
The white reflector in the sight gauge must be posi
tioned horizontally to provide proper drainage.
Under normal conditions, drain the bearing hous
ing once each year and refill with clean oil. Change
the oil more frequently if the pump is operated con
tinuously or installed in an environment with rapid
temperature change.
Monitor the condition of the bearing lubri
cant regularly for evidence of rust or mois
ture condensation. This is especially im
portant in areas where variable hot and
cold temperatures are common.
For cold weather operation, consult the factory or a
lubricant supplier for the recommended grade of
oil.