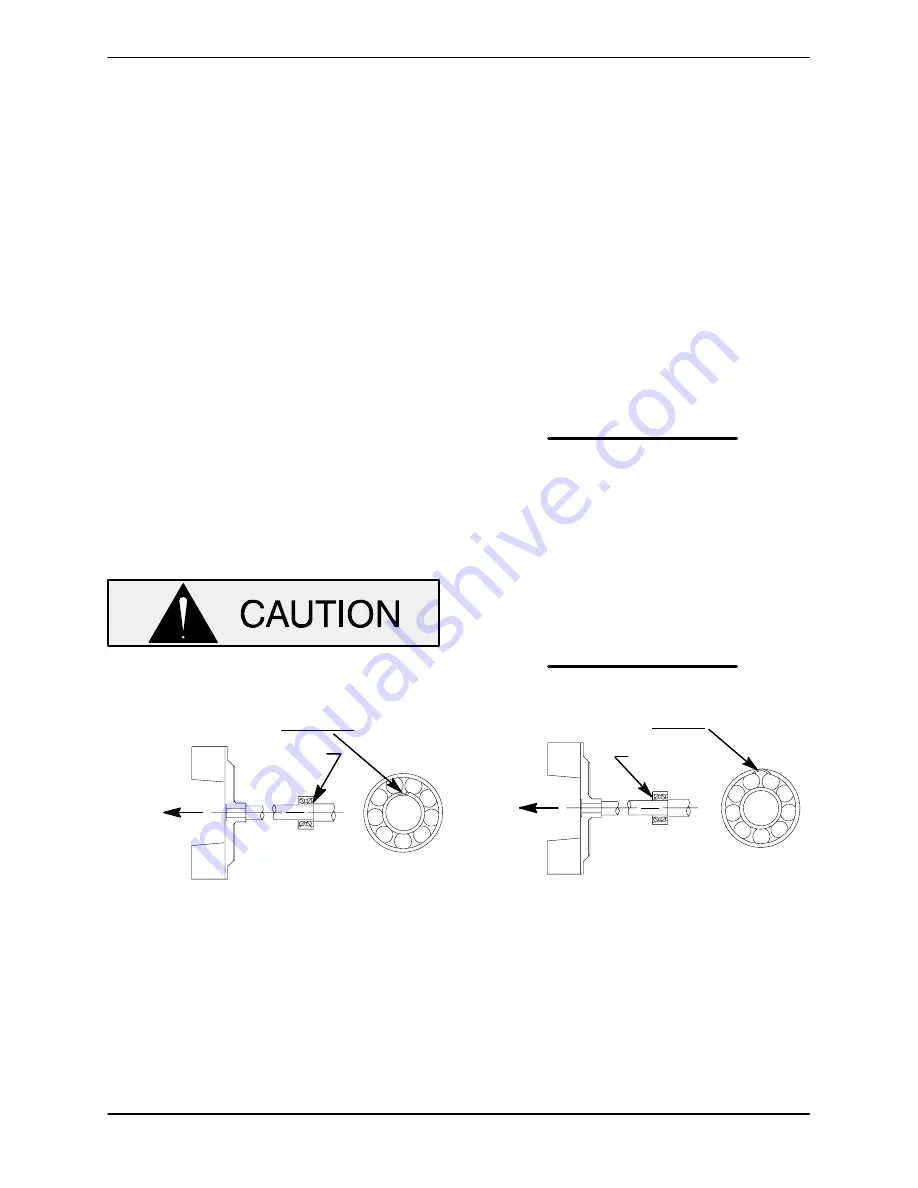
MR−05861
PA SERIES PUMPS
MAINTENANCE & REPAIR
PAGE C − 13
Rotate the bearings by hand to check for rough-
ness or binding and inspect the bearing balls. If ro-
tation is rough or the bearing balls are discolored,
replace the bearings.
The bearing tolerances provide a tight press fit
onto the shaft and a snug slip fit into the bearing
housing. Replace the bearings, shaft, or intermedi-
ate if the proper bearing fit is not achieved.
If bearing replacement is required, use a bearing
puller to remove the inboard and outboard bear-
ings (10 and 12) from the shaft.
Shaft and Bearing Reassembly and Installation
(Figure C−2)
Inspect the shaft for distortion, nicks or scratches,
or for thread damage on the impeller end. Dress
small nicks and burrs with a fine file or emery cloth.
Replace the shaft if defective.
Clean and inspect the bearings as indicated in
Shaft And Bearing Removal And Disassembly
.
To prevent damage during removal from
the shaft, it is recommended that bearings
be cleaned and inspected
in place
. It is
strongly
recommended that the bearings
be replaced
any
time the shaft and bear-
ings are removed.
The bearings may be heated to ease installation.
An induction heater, hot oil bath, electric oven, or
hot plate may be used to heat the bearings. Bear-
ings should
never
be heated with a direct flame or
directly on a hot plate.
NOTE
If a hot oil bath is used to heat the bearings, both the
oil and the container must be
absolutely
clean. If
the oil has been previously used, it must be
thor-
oughly
filtered.
Heat the bearings to a uniform temperature
no
higher than
250
_
F (120
_
C), and slide the bearings
onto the shaft, one at a time, until they are fully
seated. This should be done quickly, in one con-
tinuous motion, to prevent the bearings from cool-
ing and sticking on the shaft.
NOTE
Position the inboard bearing (10) on the shaft as in-
dicated in Figure C-5.
INSTALLATION OF NEW DEPARTURE OR
BCA/FEDERAL MOGAL 5300W SERIES BEARINGS
(OPEN OR ENCLOSED IMPELLERS)
INSTALLATION OF MRC/SKF 5300M OR
FAFNIR 5300W SERIES BEARINGS
(OPEN OR ENCLOSED IMPELLERS)
LOADING
DIRECTION OF
THRUST
BALL LOADING
GROOVE POSITIONED
AWAY FROM IMPELLER
GROOVE
DIRECTION OF
THRUST
LOADING
BALL LOADING
GROOVE POSITIONED
TOWARD IMPELLER
GROOVE
Figure C−5. Inboard Bearing Positioning
After the bearings have been installed and allowed
to cool, check to ensure that they have not moved
away from the shaft shoulders in shrinking. If
movement has occurred, use a suitable sized
sleeve and a press to reposition the bearings
against the shaft shoulders.
If heating the bearings is not practical, use a suit-
able sized sleeve, and an arbor (or hydraulic) press
to install the bearings on the shaft.