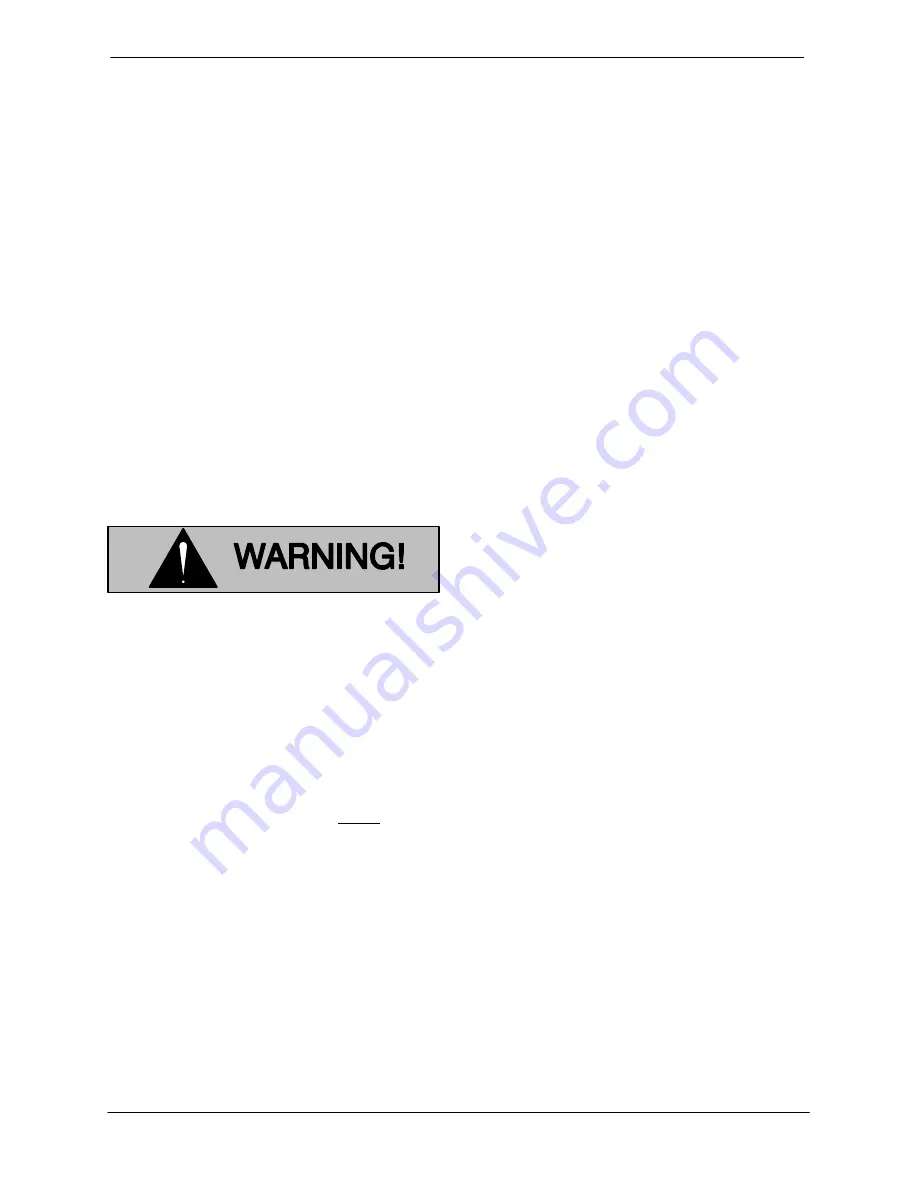
OM-01510
D SERIES
PAGE B - 2
INSTALLATION
or replaced
to ensure maximum pump serv
ice.
If the maximum shelf life has been exceeded, or if
anything appears to be abnormal, contact your
Gorman‐Rupp distributor or the factory to deter
mine the repair or updating policy.
Do not
put the
pump into service until appropriate action has
been taken.
POSITIONING PUMP
Lifting
This pump is designed to be easily positioned for
operation using the drawbar and wheels. The total
pump weight is approximately
370 pounds (167,8
kg)
, not including accessories. Customer installed
equipment such as suction and discharge piping
must
be removed before attempting to lift.
Death or serious personal injury and
damage to the pump or components
can occur if proper lifting procedures
are not observed. Make certain that
hoists, chains, slings or cables are in
good working condition and of suffi
cient capacity and that they are posi
tioned so that loads will be balanced
and the pump or components will not be
damaged when lifting. Suction and dis
charge hoses and piping must be re
moved from the pump before lifting. Lift
the pump or component only as high as
necessary and keep personnel away
from suspended objects.
Mounting
Locate the pump in an accessible place as close as
practical to the liquid being pumped. Level mount
ing is essential for proper operation.
The pump may have to be supported or shimmed
to provide for level operation or to eliminate vibra
tion.
After the pump has been positioned, block the
wheels and secure the pump to prevent creeping.
SUCTION AND DISCHARGE PIPING
Pump performance is adversely effected by in
creased suction lift, discharge elevation, and fric
tion losses. See Page E‐1 to be sure your overall
application allows the pump to operate within the
safe operation range.
Materials
Either pipe or hose maybe used for suction and
discharge lines; however, the materials must be
compatible with the liquid being pumped. If hose is
used in suction lines, it must be the rigid‐wall, rein
forced type to prevent collapse under suction. Us
ing piping couplings in suction lines is not recom
mended.
Line Configuration
Keep suction and discharge lines as straight as
possible to minimize friction losses. Make mini
mum use of elbows and fittings, which substan
tially increase friction loss. If elbows are necessary,
use the long‐radius type to minimize friction loss.
Never pull a line into place by tightening connec
tions at the pump. Lines near the pump must be in
dependently supported to avoid strain on the
pump which could cause excessive vibration and
increased diaphragm and gear train wear. If hose‐
type lines are used, they should have adequate
support to secure them when filled with liquid and
under pressure.
Fixed, Rigid Piping
This pump is equipped with an integral suction ac
cumulator chamber which promotes an efficient
flow of liquid and acts as an air cushion against
shock. Since the air in this chamber will leak away
during pump operation, the air must be replen
ished periodically. To introduce air into the cham
ber, stop the pump and remove the suction accu
mulator plug and integral gasket; this will break
prime and allow the liquid in the chamber to drain
away through the suction line.
If the pump is mounted in a system with fixed, rigid
piping, it is recommended that a flexible connec