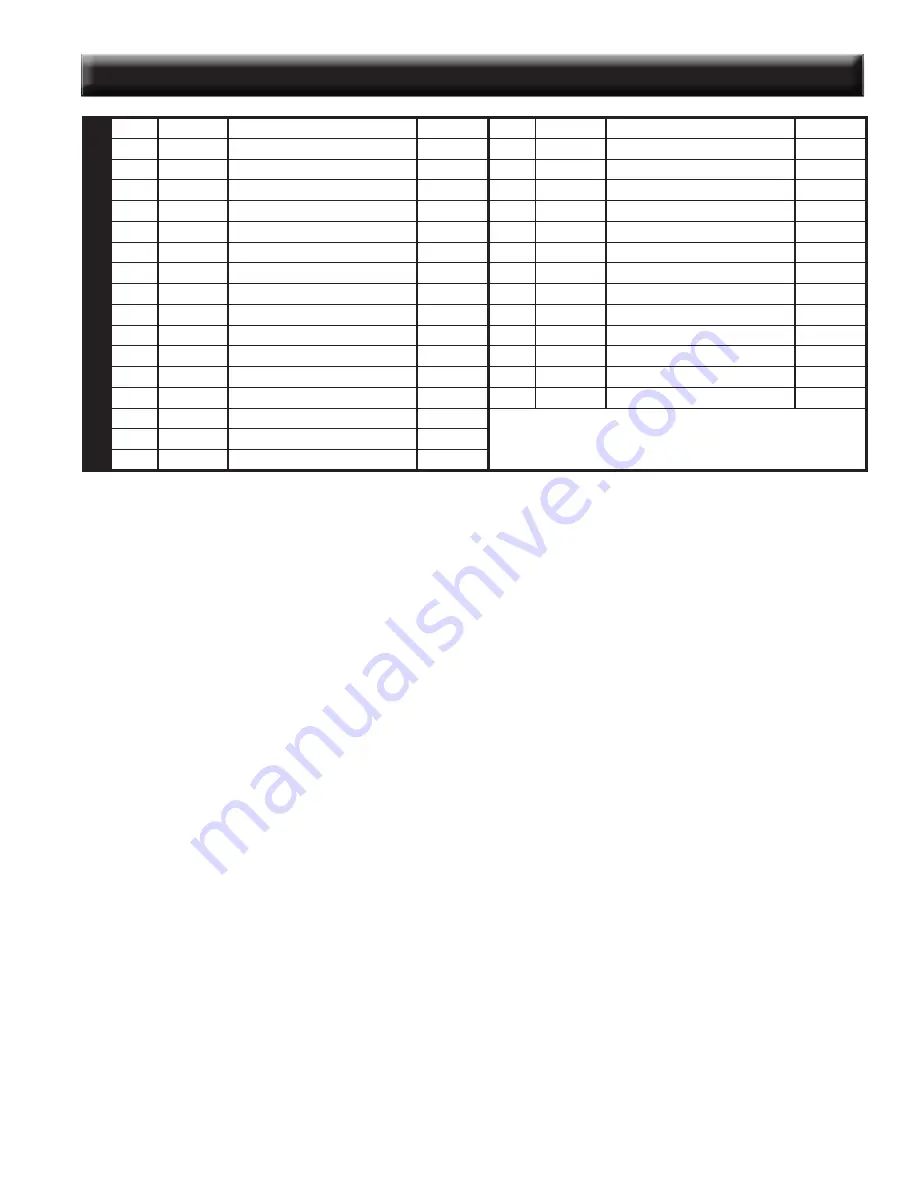
USSC
29
PARTS LIST - INSERT
Parts List
Key
Part No.
Description
Qty.
Key
Part No.
Description
Qty.
1
891373
Pad, Door Hinge (Threaded)
2
17
25580
Left Side-Rear Cabinet
1
2
69547
Weldment Sub-Base
1
18
25578
Back, Cabinet
1
3
25569
Bracket, Caster
2
19
25587
Wldmt., Facade Panel Rt-Side
1
4
891424
Caster, Plastic
2
20
89943
Knob, Cabinet Door
1
5
83412
1/4-20 x 1-1/2 Hex Bolt
2
21
25585
Panel-Left Side Facade
1
6
83136
Washer
4
22
25590
Top-Panel, Facade (2 piece)
2
7
83261
1/4-20 Lock Nut
2
23
80575
Circuit Board (PCB)
1
8
69548
Weldment, Ash Pan
1
24
25583
Cover, PCB
1
9
891137
Handle (Brushed Nickel)
1
25
25582
Cover, Panel
1
10
25570
Facade, Bottom
2
26
891435
Kit, Facade Trim (B-Lux)
1
11
83479
Leveler
2
27
891135
Handle, Spring (Large)
1
12
69619
Hopper Assembly
1
28
891331
Handle, Spring (Small)
1
13
25586
Weldment, Cabinet Top
1
N/S
891299
Poker, Burnpot
1
14
891148
Handle, Plastic
1
N/S = Not Shown
Add the suffix “MB” to the part number of any painted part.
15
25581
Right Side Cabinet
1
16
25579
Left Side-Front Cabinet
1
Notice:
For all other repair components not listed above, refer to the Pedestal Repair list and
diagrams for info.
Summary of Contents for GE200B
Page 5: ...USSC 5 COMPONENT LOCATION ...
Page 9: ...USSC 9 CLEARANCES TO COMBUSTIBLES INSERT ...
Page 25: ...USSC 25 WIRING DIAGRAM WIRING SCHEMATIC ...
Page 31: ...USSC 31 NOTE ...