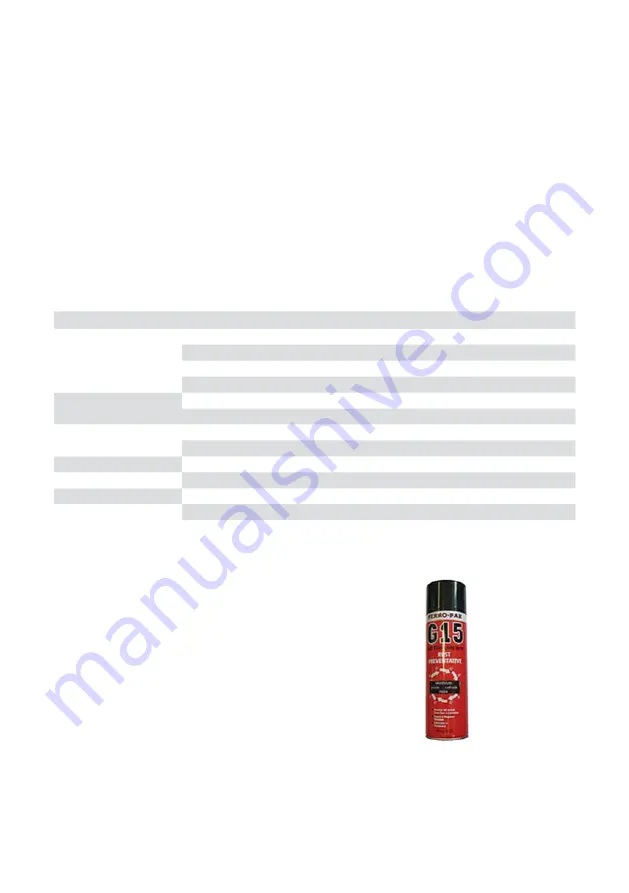
27
Lubrication
To ensure maximum life and performance
from the sprayer, grease points should be
periodically re-lubricated according to the
maintenance schedule. These include the axle
hubs, leaf spring pivots and boom hinges.
A quality
multi purpose grease
should be
used when lubricating your equipment.
An
SAE 15W40 engine oil
should be used in
the diaphragm pump.
Maintenance
To ensure maximum life and performance from
the sprayer, follow the maintenance schedule
set out below:
Corrosion Prevention
To ensure maximum life and performance from
the sprayer, G15 anti-corrosion spray has been
applied at the time of manufacture. It is used
on all fasteners such as bolts, nuts, washers
and any zinc plated components.
G15 anti-corrosion spray should also be
applied to the sprayer pre and post season.
The amount of corrosion protection necessary
will ultimately depend on local and operating
conditions.
Frequency
Maintenance Tasks
8 Hour
Check pump oil level & condition
8 Hour
Check tyre pressure
8 Hour
Check wheel nuts are torqued correctly to 100 Nm (74 ft/lb)
8 Hour
Clean suction filter if blocked
25 Hour
Grease wheel bearings
25 Hour
Grease leaf spring pivots
50 Hour
Check Aluminium outer boom bolts
50 Hour
Grease boom hinges
150 Hour
Check wheel bearings for sideways movement
300-350 Hour
Change pump oil
3 Months
Check bolts on axle bearing caps
Yearly
Clean wheel bearings, inspect, re-grease and set rolling torque
Yearly
Carry out a complete decontamination of the sprayer