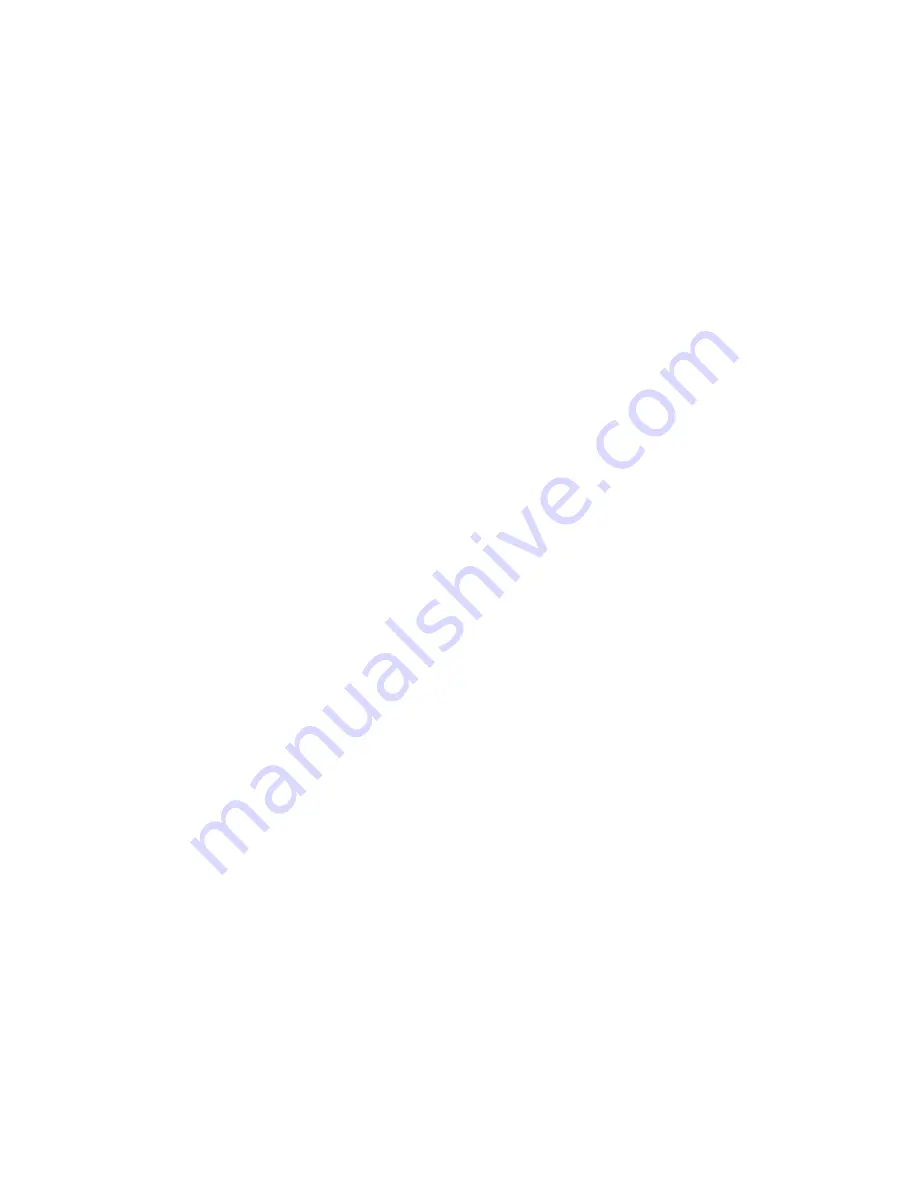
13
Pump Diaphragms
The pump diaphragms are wearing
components that need to be replaced during
the life of the pump. Life expectancy depends
upon the operation and maintenance and its
suitability for the task.
• Pump diaphragms should be replaced
prior to diaphragm failure.
• For large operations, where the sprayer
is used extensively, the pump should be
reconditioned once a season, including
replacing diaphragms, seals and valve
springs.
• It is recommended to keep a spare pump
repair kit (including diaphragms, seals,
valve o-rings and springs) on hand in
case of a breakdown. The main causes of
premature diaphragm failure are:
• Blocked or incorrectly fitted suction filter
restricting flow to the pump.
• Incorrect air damper chamber pressure.
• Running pump at speeds greater than 540
RPM.
• Exceeding the pressure limit of the pump.
• Failure to wash chemicals from pump after
use.
• Incompatibility of the diaphragm material
and the chemicals used.
• A change of oil colour indicates a pump
problem. The oil should be regularly
monitored when spraying so that any
problem is detected as soon as possible.
If the oil goes milky in colour, it is likely the
diaphragm has been damaged and the
spray mixture has come into contact with
the oil. If the oil goes black (or dark grey), it
is likely the pump has overheated.
To replace a side diaphragm:
When side diaphragms require replacement it
is normal practice to replace the air damper
diaphragm as well.
1. Flush pump with clean water to remove
chemical residue, then flush with
appropriate decontaminating agent (refer
to chemical label for decontamination
instructions).
2. Run pump dry for 15-20 seconds to
remove water.
3. Remove all air from air damper chamber
by pushing in air valve.
4. Remove pump from sprayer.
5. Remove pump manifolds and pump
heads.
6. Drain oil from pump.
NOTE: Carefully note the position and
orientation of all heads, manifolds and
valves when disassembling pump. Failure to
reassemble correctly will result in severe pump
damage.
7. Remove diaphragms.
8. Remove cylinder sleeves.
9. Flush inside of pump with diesel.
10. Visually inspect inner workings of pump.
11. Reassemble with new diaphragms (must
be correct diaphragms) once satisfied with
condition of pump.
12. Refill with oil. Rotate pump manually (by
hand) to remove air locks. Do not overfill.