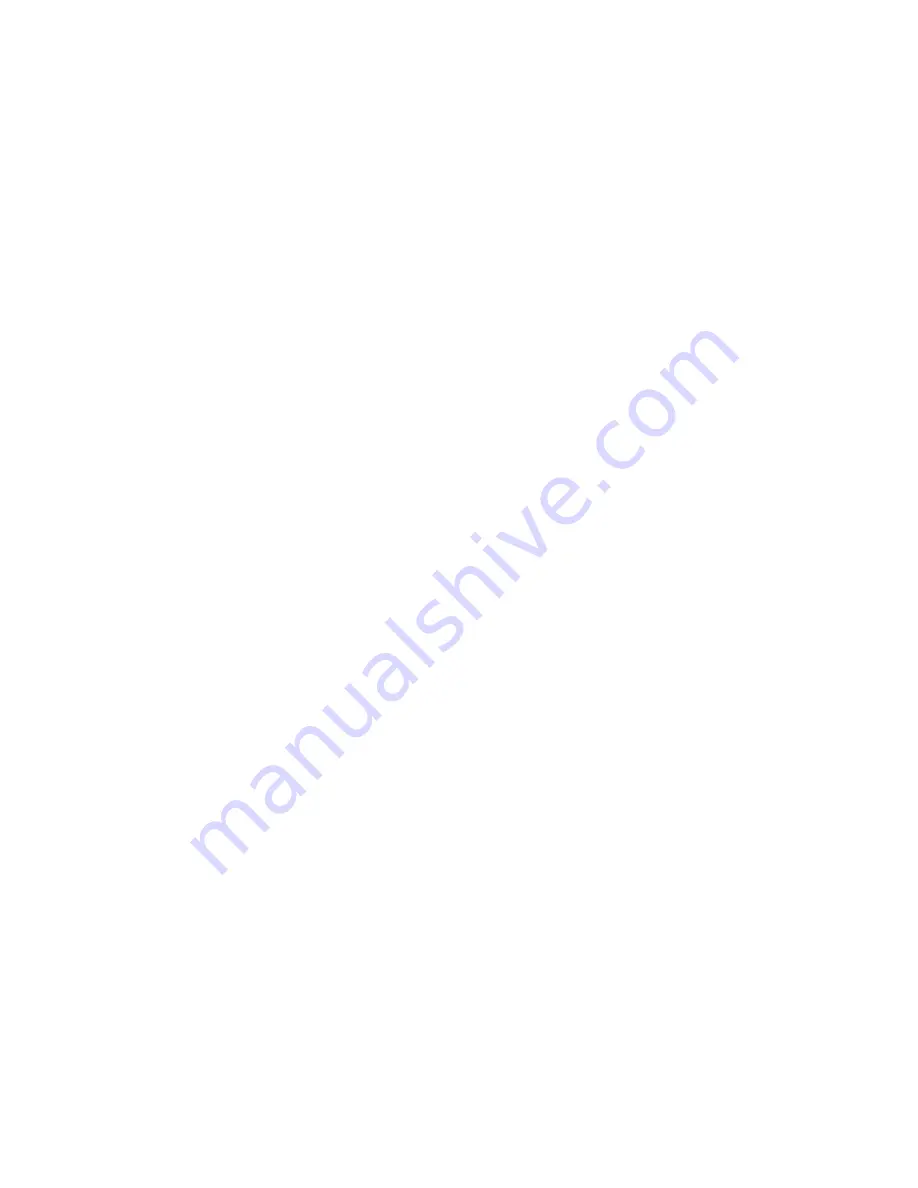
4.3 TEMPERATURE
A battery location having an ambient temperature of 25°C
(77°F) will result in optimum battery life. Batteries operated
above this temperature will suffer reduced life, while batteries
operated below this temperature may exhibit suppressed
capacity. Though brief temperature excursions between
0°C (32°F) and 40°C (104°F) can be tolerated, the normal
operating temperature is between 16°C (60°F) and 32°C
(90°F).
4.4 ELECTROLYTE LEVEL
During normal operation, the electrolyte level should be
between the high and low marks on the battery container.
Upon receipt of the battery, the electrolyte level may be a
bit lower than this mark; after charging, it may be higher.
The reason is that gas bubbles formed during charge will
adhere to the battery plates, displacing and raising the
electrolyte level. Do not attempt to adjust the electrolyte
either immediately upon receipt or immediately after the
initial charge.
4.5 CELL POSITIONING
By now, it is assumed that the rack has been assembled.
Determine the desired position of the positive and negative
terminals. Measure and mark the center of the rack.
Determine the number of battery blocks that will fit on a step/
tier of the rack. If that number is odd, position the centerline
of the first battery block on the centerline of the rack step/tier.
If the number is even, position the end of battery block on
the centerline of the rack step/tier. Work from the center out,
positioning the positive terminal next to the negative terminal
of the adjacent cell.
If a lubricant is needed to facilitate battery
positioning, use only Dow Corning 111.
Lubricants that contain solvents may damage
the battery containers and void warranty.
4.6 FLASH ARRESTORS
After the batteries have been positioned on the rack (but
before the inter-unit and inter-tier connections have been
made), replace the shipping caps with the provided flame/
flash arrestors.
4.7 CONTACT SURFACES
Gently clean the contact surfaces of the battery terminal
posts using a 3M Scotch Brite or similar scouring pad. Coat
the electrical contact surfaces lightly with provided No-Ox
grease.
4.8 ELECTRICAL CONNECTIONS
Install and torque the provided M8 stainless steel hardware
and torque the cell connector (or terminal plate) to the post.
Target connection torque is 100 - 110 inch-lbs. (11.3-12.0
N-m). Re-torque the stainless steel hardware 24 hours after
the initial tightening to account for relaxation of the lead-
hardware connection.
Electrical connections must be clean to minimize voltage drop
and prevent connector heating. If corrosion is observed, DO
NOT RE-TORQUE! The connection must be disassembled,
cleaned, neutralized, and then re-torqued.
Install the inter-tier cables as necessary. Do not connect
cables directly to the battery post. Utilize the terminal
plates provided for main terminal and inter-tier connections.
Re-check to be certain that the batteries are connected
positive terminal to negative terminal throughout the string.
Before connecting the battery string to the charger/load,
measure the total voltage at the battery terminals. The
voltage should be equal to the number of cells times the
voltage of one cell. For example, 60 cells times 2.09 volts
per cell = 125.40 volts (1.250 SG) or 60 cells times 2.05 volts
per cell = 123.0 volts (1.215 SG).
4.9 CONNECTION RESISTANCE
Connection resistance or micro-ohm (µ
Ω
) measurements
should be taken at the time of installation and annually
thereafter. Initial measurements at installation become
benchmark values. Future values are compared to
this benchmark as an indication of connection integrity.
Re-torque of connections should be performed annually or
when connection resistance increases to more than 20%
over the benchmark value.
4.10 Labels and Markings
Numerals and polarity markings should not be applied
until after the cells have been installed on the rack. It is
recommended that they be applied to jar surfaces only, and
not to cell covers or rack rails.
2. Clean the plastic jar surface, in the area where the
numeral is to be located, by using a cloth dampened with a
washing soda solution. Immediately dry the area using a soft
dry cloth to remove residual washing soda.
CAUTION!!
Do not use any solvent type materials as they
may cause damage to the plastic jar material.
3. It is a general practice to designate the positive terminal
cell as #1 with succeeding cells in series in ascending order.
4.11 INITIAL CHARGE
The first charge that the battery receives after shipping,
storage and installation is very important as it may affect the
life of the battery. Determine the maximum charge voltage
output that the charge system can provide and charge the
battery in the least amount of time possible according to
Table A. This maximum voltage divided by the number of
cells connected in series is the maximum charge voltage per
cell (VPC). If long periods of continuous charging are not
possible at the installation, (e.g. photovoltaic applications)
the battery should be charged where such capability exists.
The recommended times given in TABLE A are considered
minimum. Charge the cells until the charge current tapers
and stabilizes for 3 hours. Then, charge the battery for the
times and voltages given in TABLE A.
3
Summary of Contents for 93.10G
Page 10: ...8 NOTES ...
Page 11: ......