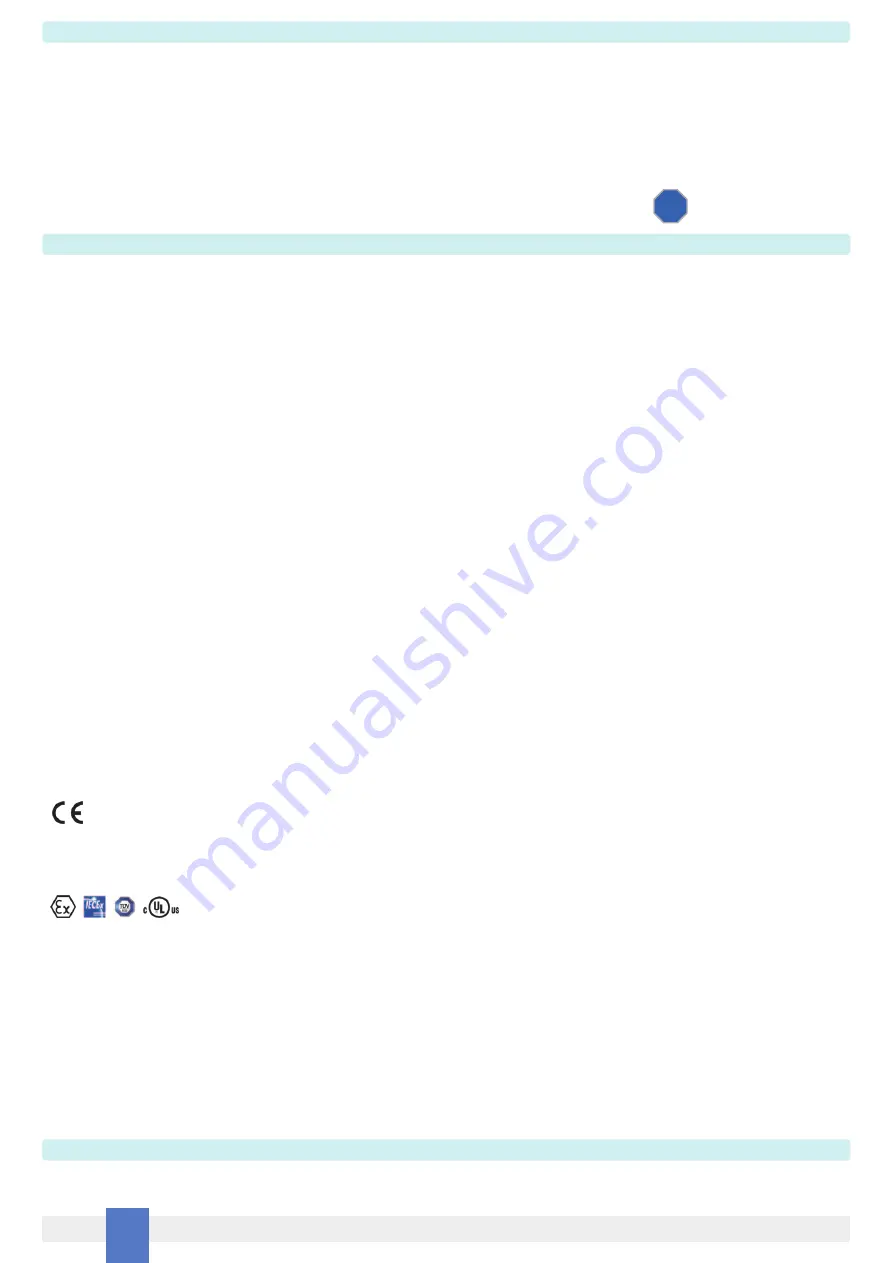
D6072
- SIL 2 Multifunction Temperature Converter
G.M. International ISM0216-5
2
General Description:
The single and dual channel Temperature Signal Converter D6072S and D6072D accepts a low level dc signal from millivolt, thermocouple or resistance/RTD or
transmitting potentiometer sensor and converts, with isolation, the signal to drive a load, suitable for applications requiring SIL 2 (according to IEC 61508:2010) in safety related
systems for high risk industries. Output signal can be direct or reverse. Modbus RTU RS-485 output is available on Bus connector.
Cold junction compensation can be programmed as:
- Automatic: provided by an internal temperature sensor;
- Fixed: to a user-customizable temperature value;
- External: making use of an external RTD;
- Remote: (only D6072D) connecting compensation RTD to one of the two channels.
For D6072D module: duplicator function provides two independent outputs from one single input. Output function can be configured as: average, subtractor, low/high or redundancy
selector. Modules are provided with alarm function, which is available via solid state contact output, Termination Board and Power Bus. Mounting on standard DIN-Rail, with or without
Power Bus, or on customized Termination Boards, in Safe Area / Non Hazardous Location or in Zone 2 / Class I, Division 2.
Functional Safety Management Certification:
G.M. International is certified by TUV to conform to IEC61508:2010 part 1 clauses 5-6 for safety related systems up to and included SIL3.
Technical Data
Characteristics
Supply:
24 Vdc nom (18 to 30 Vdc) reverse polarity protected, ripple within voltage limits
≤
5 Vpp, 2 A time lag fuse internally protected.
Current consumption @ 24 V:
50 mA (D6072D), 35 mA (D6072S) with 20 mA out typical.
Power dissipation @ 24 V:
1.0 W (D6072D), 0.75 W (D6072S) with 20 mA out typical.
Isolation (Test Voltage):
In/Out 2.5 KV; In/Supply 2.5 KV; In/In 500 V; Out/Supply 500 V; Out/Out 500 V.
Input:
See section “Input specifications” for more details on Input sensors.
4-wire RTD input only on D6072S. Possibility of configuring user customized sensor (TC or RTD). Choice between °C/°F.
Integration time:
from 50 ms to 500 ms depending on sensor and fast/slow integration.
Resolution:
1 µV on mV/TC, 1 m
Ω
on RTD/resistance, 0.0001 % on transmitting pot.
Visualization:
0.1 °C on temp.,10 µV on mV, 10 m
Ω
on resistance, 0.1 % on pot.
Input range:
within sensor limits (-500 to +500 mV for mV, 0-4 k
Ω
for resistance).
Measuring RTD current:
≤
0.15 mA.
2 wire RTD line resistance compensation:
≤
50
Ω
(programmable).
Thermocouple Reference Junction Compensation:
programmable as
automatic with internal compensator, fixed (–60 to +100 °C), external with any supported RTD, or remote
using 1 channel (D6072D).
Thermocouple burnout current:
≤
50 µA.
Fault:
enabled or disabled. Analog output can be programmed to reflect fault conditions via downscale, highscale or customized value forcing. Fault conditions are also signaled via BUS
and by red LED on front panel for each channel. Fault conditions are: Sensor burnout, Sensor out of range, Output saturation, Internal fault, Cable resistance fault.
Output:
Fully customizable 0/4 to 20 mA, on max. 300
Ω
load source mode, current limited at 24 mA. In sink mode, external voltage generator range is V min. 3.5V at 0
Ω
load and V
max. 30V. If generator voltage Vg > 10 V, a series resistance
≥
(Vg - 10)/0.024
Ω
is needed. The maximum value of series resistance is (Vg - 3.5)/0.024
Ω
.
Resolution:
1 µA current output.
Transfer characteristic:
linear, direct or reverse on all input sensors.
Response time:
≤
20 ms (10 to 90 % step).
Output ripple:
≤
20 mVrms on 250
Ω
load.
Damping factor:
≤
30 s, configurable.
Modbus Output:
Modbus RTU protocol, from 4800 to 115.200 bps.
Alarm:
Trip point range:
within rated limits of input sensor (see input step resolution).
ON-OFF delay time:
0 to 1000 s, 100 ms step.
Hysteresis:
within rated limits of input sensor.
Output:
voltage free SPST photoMOS: 100 mA, 60 Vdc (
≤
1 V voltage drop).
Performance:
Ref. Conditions 24 V supply, 250
Ω
load, 23 ± 1 °C ambient temperature, slow integration mode, 4-wires (for D6072S) or 3-wires (for D6072D) configuration for RTD.
Input:
Calibration and linearity accuracy:
see section “Input Specifications”.
Temperature influence:
see section “Input Specifications”.
Ref. Junction Compensation influence:
≤
± 1 °C (internal PT1000 sensor).
Analog Output:
Calibration accuracy:
≤
±10 µA.
Linearity error:
≤
±10 µA.
Supply voltage influence:
≤
±0.02 % of full scale for a min to max supply change.
Load influence:
≤
±0.02 % of full scale for a 0 to 100 % load resistance change.
Temperature influence:
≤
±2 µA/°C.
Compatibility:
CE mark compliant, conforms to Directive:
2014/34/EU ATEX, 2014/30/EU EMC, 2014/35/EU LVD, 2011/65/EU RoHS.
Environmental conditions:
Operating:
temperature limits – 40 to + 70 °C, relative humidity 95 %, up to 55 °C.
Max altitude:
2000 m a.s.l.
Storage:
temperature limits – 45 to + 80 °C.
Safety Description:
ATEX:
II 3G Ex ec IIC T4 Gc
IECEx:
Ex ec IIC T4 Gc
UL:
NI / I / 2 / ABCD / T4;
C-UL:
NI / I / 2 / ABCD / T4
Approvals:
ATEX conforms to EN60079-0, EN60079-7
(pending)
.
IECEx conforms to IEC60079-0, IEC60079-7
(pending)
.
UL & C-UL E222308 conforms to UL 61010-1 and UL 121201 for UL and CAN/CSA C22.2 No.61010-1-12 and CSA C22.2 No. 213 for C-UL.
TÜV Certificate No. C-IS-722160171, SIL 2 conforms to IEC61508:2010 Ed.2 .
TÜV Certificate No. C-IS-236198-09, SIL 3 Functional Safety Certificate conforms to IEC61508:2010 Ed.2, for Management of Functional Safety.
Mounting:
EN/IEC60715 TH 35 DIN-Rail, with or without Power Bus or on customized Termination Board.
Weight:
about 135 g D6072D, 130 g D6072S.
Connection:
by polarized plug-in disconnect screw terminal blocks to accommodate terminations up to 2.5 mm
2
.
Location:
installation in Safe Area/Non Hazardous Locations or Zone 2, Group IIC T4 or Class I, Division 2, Group A,B,C,D, T4.
Protection class:
IP 20.
Dimensions:
Width 12.5 mm, Depth 123 mm, Height 120 mm.
The module is fully programmable. Operating parameters can be changed from PC via PPC5092 adapter connected to USB serial line and SWC5090 software.
Measured values and diagnostic alarms can be read on both serial configuration or Modbus output line.
SWC5090 software also allows the Monitoring and Recording of values. For details please see SWC5090 manual ISM0154.
Programming
FSM
SIL 3