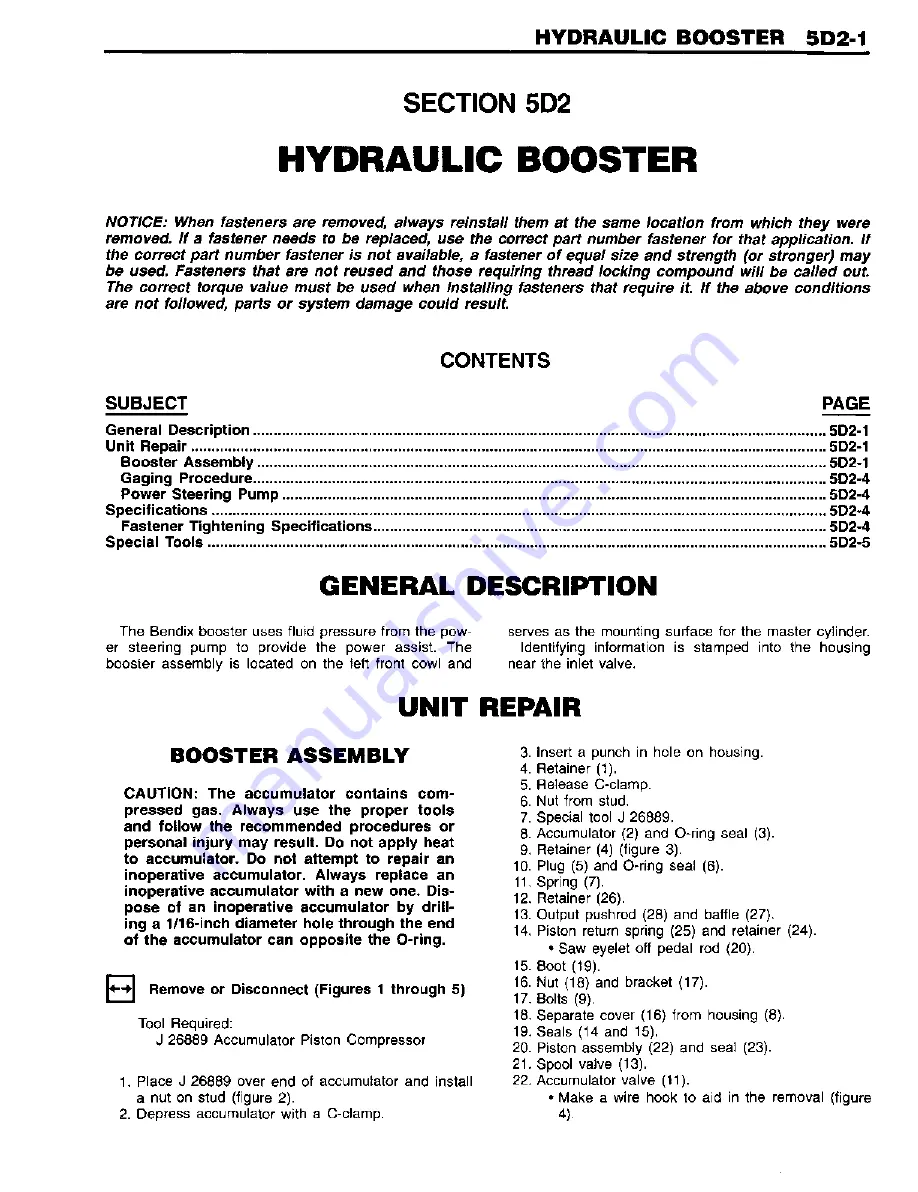
SECTION 5D2
HYDRAULIC BOOSTER
NOTICE: When fasteners are removed, always reinstall them at the same location from which they were
removed. If a fastener needs to be replaced, use the correct part number fastener for that application. If
the correct part number fastener is not available, a fastener of equal size and strength (or stronger) may
be used. Fasteners that are not reused and those requiring thread locking compound will be called out.
The correct torque value m ust be used when installing fasteners that require it. If the above conditions
are not followed, parts or system damage could result
CONTENTS
General D escription........................................................................................................................................................ 5D2-1
Unit R e p a ir........................................................................................................................................................................ 5D2-1
Booster A ssem b ly....................................................................................................................................................... 5D2-1
Gaging Procedure........................................................................................................................................................ 5D2-4
Power Steering P u m p ................................................................................................................................................ 5D2-4
GENERAL DESCRIPTION
The Bendix booster uses fluid pressure from the pow-
serves as the mounting surface for the master cylinder,
er steering pump to provide the power assist. The
Identifying information is stamped into the housing
booster assembly is located on the left front cowl and
near the inlet valve.
UNIT REPAIR
BOOSTER ASSEMBLY
CAUTION: The accum ulator contains com
pressed gas. Always use the proper tools
and follow the recommended procedures or
personal injury may result. Do not apply heat
to accumulator. Do not attempt to repair an
inoperative accumulator. Always replace an
inoperative accumulator with a new one. Dis
pose of an inoperative accumulator by drill
ing a 1/16-inch diameter hole through the end
of the accumulator can opposite the O-ring.
Remove or Disconnect (Figures 1 through 5)
Tool Required:
J 26889 Accumulator Piston Compressor
1. Place J 26889 over end of accumulator and install
a nut on stud (figure 2).
2. Depress accumulator with a C-clamp.
3. Insert a punch in hole on housing.
4. Retainer (1).
5. Release C-clamp.
6. Nut from stud.
7. Special tool J 26889.
8. Accumulator (2) and O-ring seal (3).
9. Retainer (4) (figure 3).
10. Plug (5) and O-ring seal (6).
11. Spring (7).
12. Retainer (26).
13. Output pushrod (28) and baffle (27).
14. Piston return spring (25) and retainer (24).
• Saw eyelet off pedal rod (20).
15. Boot (19).
16. Nut (18) and bracket (17).
17. Bolts (9).
18. Separate cover (16) from housing (8).
19. Seals (14 and 15).
20. Piston assembly (22) and seal (23).
21. Spool valve (13).
22. Accumulator valve (11).
• Make a wire hook to aid in the removal (figure
4).
Summary of Contents for S Series 1994
Page 1: ......
Page 11: ...VIEW A p n n n j VIEW C F7554 Figure 10 Hydra Matic 4L60 E Transmission I D Location...
Page 24: ...NOTES...
Page 26: ......
Page 69: ...NOTES...
Page 71: ...3 2 STEERING...
Page 73: ......
Page 84: ......
Page 102: ...40...
Page 130: ...NOTES...
Page 146: ...NOTES...
Page 162: ...NOTES...
Page 166: ...Figure 5 Removing the Pinion Flange Figure 6 Pressing the Drive Pinion from the Cage...
Page 178: ...Figure 3 Spreading the Differential Case Figure 4 Removing the Differential...
Page 190: ...NOTES...
Page 202: ...NOTES...
Page 206: ...F5785...
Page 212: ...B Button Moved Out of Bearing Bore F5791...
Page 228: ...NOTES...
Page 232: ......
Page 234: ......
Page 236: ...Adjuster 63 Bolt 64 Lock Figure 10 Turning the Adjuster Plug K3 Models...
Page 237: ...Figure 13 Removing the Pinion Seal 39 Bearing Cup Figure 16 Removing the Inner Bearing Cap...
Page 261: ...F7475...
Page 267: ...B Button Moved Out of Bearing Bore F5791...
Page 294: ...NOTES...
Page 300: ...NOTES...
Page 318: ...NOTES...
Page 322: ...SR207LN2 EDS...
Page 324: ......
Page 326: ...OVERHEAD OILING AND RETURN MAIN OIL GALLERY N30005 6A2 J EDS...
Page 368: ...103 153 127 V1200...
Page 370: ......
Page 372: ......
Page 374: ...F9375 Figure 7 Engine Lubrication Diagram Engines Without Balance Shaft...
Page 376: ...Figure 9 Engine Lubrication Diagram Engines With Balance Shaft...
Page 399: ...V2974...
Page 410: ......
Page 412: ...195 196 201 174 252 163 165 164 244 3706r3924...
Page 452: ......
Page 454: ...163 164 V1202...
Page 456: ...20 21x 302 210 4 0 41 2 5 2 5 1 2 51 4 2 e3 54 3 9 252 252 S 255 255 25 6 256 209 V1196...
Page 458: ...100 1 8 4 185 183 177 v 75 201 3706r1204...
Page 460: ......
Page 510: ......
Page 512: ...V2131...
Page 514: ...110 106 106 103 90 93 89 88 87 86 v 7 7 7 7 j A _ 111 f t 2 a a s 53 49 L 47 46 3706r4751...
Page 516: ...259 260 150 237 S lM 180 167180 J 1 82 183 170 169 1 1 78 1 7 9 213212 2 0 7 205 r i 3706r4752...
Page 566: ...NOTES...
Page 574: ...NOTES...
Page 618: ...SPECIAL TOOLS...
Page 620: ...NOTES...
Page 672: ......
Page 682: ......
Page 686: ......
Page 694: ...RH0213 4L60 E...
Page 695: ...657 659 m i J 8092 H J 34196 4 3 34196 5 657 658 665 J 23907 J 7004 1 J 8092 RH0214 4L60 E...
Page 696: ...J 8092 J 34196 4 33 31 J 8092 RH0215 4L60 E...
Page 697: ...SPECIAL TOOLS...
Page 698: ...SPECIAL TOOLS...
Page 758: ...RH0194 4L80 E...
Page 764: ......
Page 770: ...SPECIAL TOOLS...
Page 771: ...SPECIAL TOOLS CONT...
Page 772: ......
Page 775: ......
Page 776: ......
Page 785: ......
Page 804: ...NOTES...
Page 806: ......
Page 808: ......
Page 822: ...3707r5079...
Page 840: ......
Page 848: ...NOTES...
Page 852: ......
Page 860: ...F5435...
Page 866: ......
Page 878: ...F9167...
Page 882: ...16 FrontOutputShaft 18 DrivtQNr 19 DrivenGm t 20 DriveChain 22 FrontOutputBearing V2836...
Page 890: ...F9168...
Page 908: ......
Page 919: ......