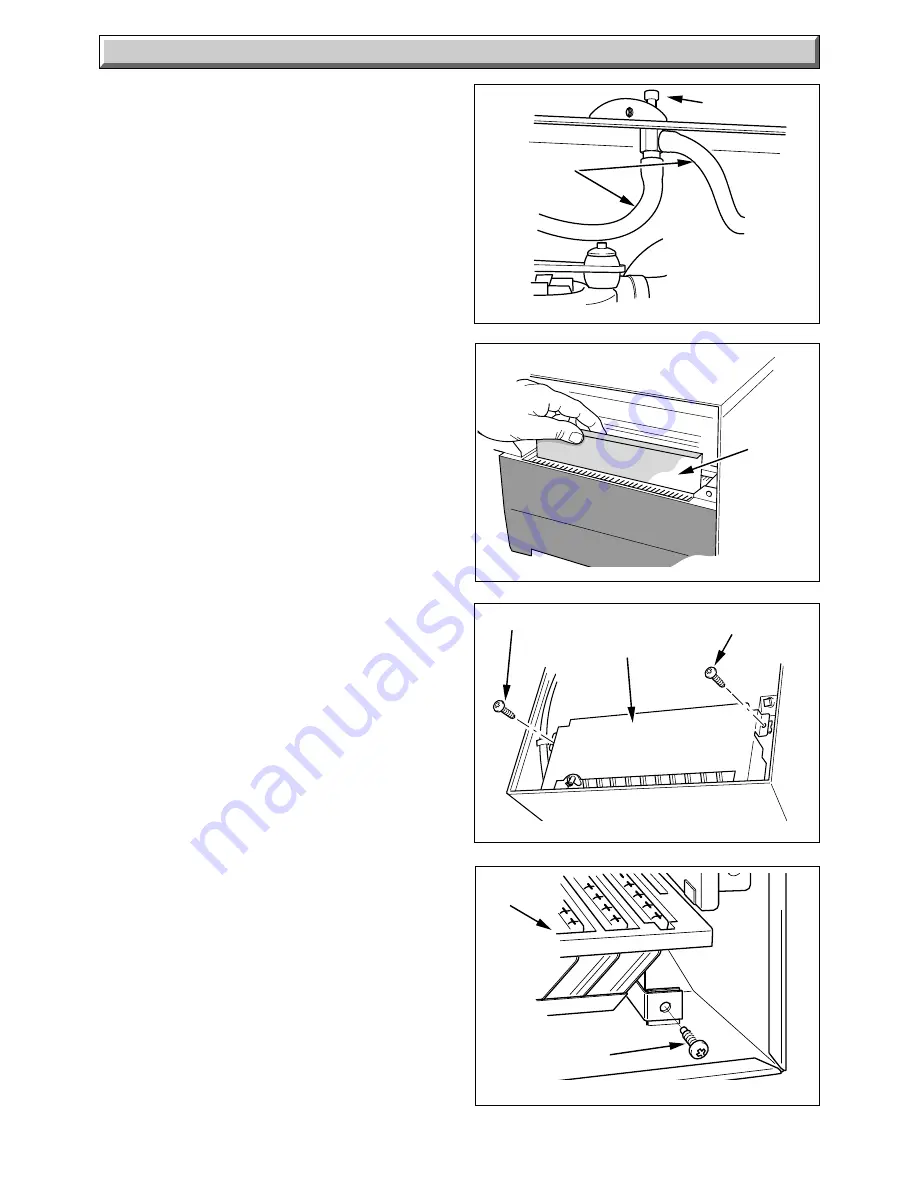
18
221899A
Diagram 8.4
COMBUSTION
CHAMBER
COVER
7226
SCREW
BURNER
RETAINING
SCREW
BURNER
SCREW
Diagram 8.3
6778
8 Servicing
Diagram 8.2
BAFFLE
(6 off)
6779
REMEMBER, When replacing a part on this appliance, use only
spare parts that you can be assured conform to the safety and
performance specification that we require. Do not use
reconditioned or copy parts that have not been clearly authorised
by Hepworth Heating Ltd.
Products of Combustion Check
Note: To obtain a products of combustion reading, remove the
cap from the sampling point, located on top of the inner casing,
see diagram 8.1.
Connect the analyser tube onto the nipple.
Switch on the electrical supply and gas supply then operate the
boiler.
On completion of the test switch off the electrical supply and the
gas supply, remove analyser tube and replace sampling point
cap.
Servicing
Before servicing turn off the gas and isolate the electrical supply
to the boiler.
After completing a service always test for gas soundness, make
electrical checks and carry out functional check on controls.
Unless stated otherwise all parts are replaced in the reverse
order to removal.
8.1 Access
Remove the boiler case, see diagram 5.1 and Section 5.2.
8.2 Burner
Remove front combustion chamber cover which is secured by
two screws, see diagram 8.3.
Pull back electrode protection sleeve and disconnect electrode
connection along with earth connection, see diagram 8.6.
Remove the burner retaining screw located at the right hand
side of the burner, see diagram 8.4.
When completed, take hold of burner and slide it to the left
clearing the injector and remove. Take care not to damage the
combustion chamber insulation
Use a vacuum cleaner or suitable stiff brush (not wire) to clean
the burner thoroughly, making sure that all the burner ports are
clear and unobstructed.
On refitting and after cleaning the heat exchanger make sure
the burner is fitted correctly, that is, located on the injector and
horizontal.
Note: It is advisable while servicing the burner to check the
combustion chamber insulation and replace if damaged, see
Section 10.10.
8.3 Cleaning Heat Exchanger Flueways
Disconnect the air pressure switch tube connection, both clear
tubes from test nipple, see diagram 8.1.
Remove the blue and purple electrical connections from the fan
see diagram 5.5.
If top outlet installation: Remove air deflector, or it may just be
swung back by loosening the wing-nuts, to enable fan assembly
to be removed, see diagram 8.7 and Section 5.3.
Remove the fan assembly complete with the flue elbow, see
diagram 5.5 and Section 5.3
Place a sheet of paper in the base of the combustion chamber
and over the injector to prevent particles entering.
Remove the baffles, see diagram 8.2.
Diagram 8.1
CLEAR AIR
PRESSURE
TUBES
SAMPLING
POINT
7231