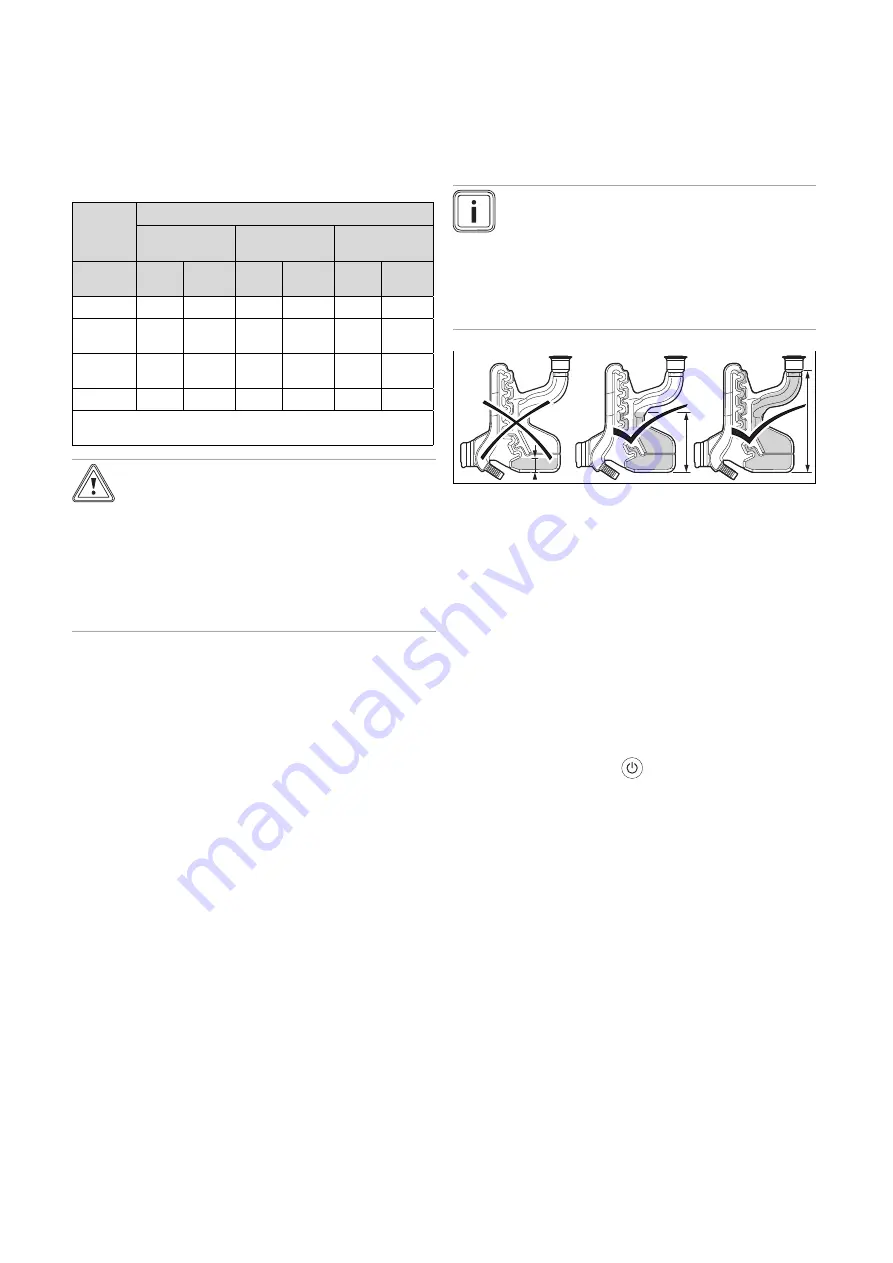
Start-up 9
0020289288_02 MicraCom Installation and maintenance instructions
25
–
If the entire filling and supplementary water quantity dur-
ing the operating life of the system exceeds three times
the nominal volume of the heating installation, or
–
If the guideline values listed in the following table are not
met, or
–
If the pH value of the heating water is less than 8.2 or
more than 10.0.
Total
heating
output
Water hardness at specific system volume
1)
≤
20 l/kW
> 20 l/kW
≤
50 l/kW
> 50 l/kW
kW
ppm
CaCO
₃
mol/
m
³
ppm
CaCO
₃
mol/
m
³
ppm
CaCO
₃
mol/
m
³
< 50
< 300
< 3
200
2
2
0.02
> 50
to
≤
200
200
2
150
1.5
2
0.02
> 200
to
≤
600
150
1.5
2
0.02
2
0.02
> 600
2
0.02
2
0.02
2
0.02
1) Nominal capacity in litres/heating output; in the case of multi-
boiler systems, the smallest single heating output is to be used.
Caution.
Risk of material damage if the heating
water is treated with unsuitable additives.
Unsuitable additives may cause changes in
the components, noises in heating mode and
possibly subsequent damage.
▶
Do not use any unsuitable antifreeze and
corrosion inhibitors, biocides or sealants.
No incompatibility with our products has been detected to
date with proper use of the following additives.
▶
When using additives, follow the manufacturer's instruc-
tions without exception.
We accept no liability for the compatibility of any additive or
its effectiveness in the rest of the heating system.
Additives for cleaning measures (subsequent
flushing required)
–
Adey MC3+
–
Adey MC5
–
Fernox F3
–
Sentinel X 300
–
Sentinel X 400
Additives intended to remain permanently in the
installation
–
Adey MC1+
–
Fernox F1
–
Fernox F2
–
Sentinel X 100
–
Sentinel X 200
Additives for frost protection intended to remain
permanently in the installation
–
Adey MC ZERO
–
Fernox Antifreeze Alphi 11
–
Sentinel X 500
▶
If you have used the above-mentioned additives, inform
the end user about the measures that are required.
▶
Inform the end user about the measures required for frost
protection.
9.3
Filling the heating installation
Note
After each start-up, the product works at reduced
output when starting in order to facilitate the heat
transfer effect. This does not apply for check pro-
grammes and does not result in any loss of com-
fort for the end user. Status code
S.58
corres-
ponds to this phase. The display shows a tem-
perature of approx. 50 °C in this phase.
1.
Ensure that the condensate siphon has been filled cor-
rectly.
2.
Before filling the heating installation, ensure that it has
been flushed out sufficiently.
3.
Connect the filling/draining cock in the heating install-
ation to a heating water supply in accordance with the
relevant standards.
4.
Open all of the thermostatic radiator valves and, if re-
quired, the service valves.
5.
Open the heating water supply and the filling tap so that
the heating water flows into the heating installation.
◁
The heating circuit is automatically purged via the
hose that is connected to the pump.
Starting up the product
6.
Press the on/off button
.
◁
The display shows the basic display.
7.
Start check programme
P.08
. (
Check programmes (
◁
The product's heating circuit is automatically purged
via the hose that is connected to the pump.
8.
Purge the highest radiator until water flows out of the
purging valve without bubbles.
9.
Purge all other radiators until the entire heating installa-
tion has been completely filled with heating water.
10. Close all purging valves.
11. Fill with heating water until the required filling pressure
is reached.
–
0.10 to 0.14 MPa (1.00 to 1.40 bar)
▽
If the heating installation extends over several
storeys, higher filling pressures may be required to
avoid air entering the heating installation.
12. Close the filling tap and the heating water supply.
13. Check all of the connections and the entire circuit for
leaks.