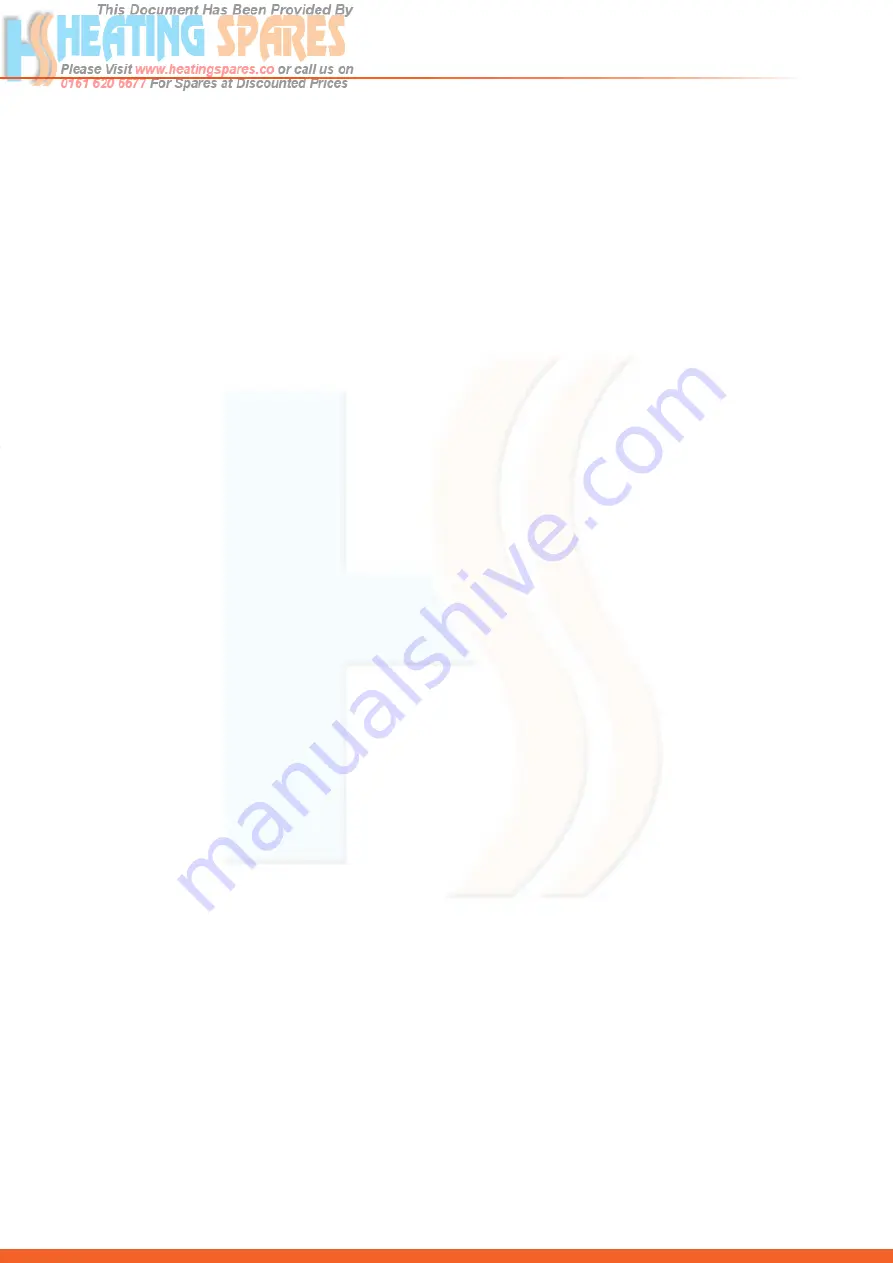
Supplied By www.heating spares.co Tel. 0161 620 6677
7
Servicing, Maintenance
and Spare Parts
Servicing and Maintenance
To ensure the continued efficient and safe operation of the
boiler it is recommended that it is checked and serviced as
necessary at regular intervals. The frequency of servicing will
depend upon the particular installation conditions and usage,
but in all cases the boiler must be serviced at least once a
year.
If this appliance is installed in a rented property there is a duty
of care imposed on the owner of the property by the current
issue of the Gas Safety (Installation and Use) Regulations,
Section 35.
Servicing/maintenance should be carried out by a
competent
person
in accordance with the rules in force in the countries
of destination.
To obtain service, please call your installer or Glow-worm’s
own service organisation using the telephone number on the
inside front cover of this literature.
“Benchmark” scheme
Glow-worm support the Benchmark initiative. It is very
important that the Installation, Commissioning and Service
Record is completed by the installation engineer and handed
over to the user.
Spare Parts
Remember, when replacing a part on this appliance, use
only spare parts that you can be assured conform to the
safety and performance specification that we require. Do not
use reconditioned or copy parts that have not been clearly
authorised by Glow-worm.
If a part is required contact Glow-worm’s own service
organisation.
Please quote the name of the appliance, this information will
be on the name badge on the front of the appliance.
If in doubt seek advice from the local gas company or Glow-
worm’s own service organisation using the telephone number
on the inside front cover of this booklet.