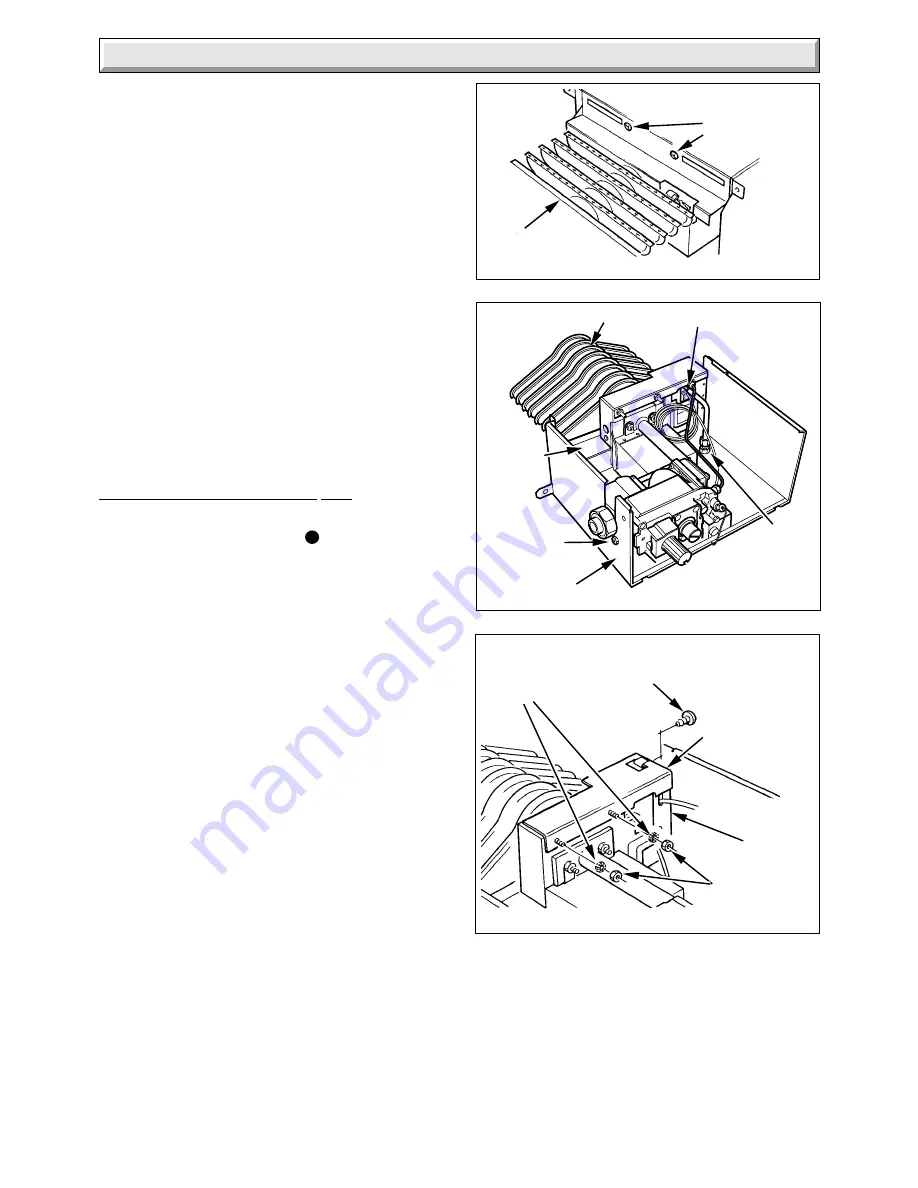
15
221781A
Diagram 8.2
Diagram 8.1
SECURING
SCREWS
1613
BURNER
ELECTRODE
BURNER
LOWER
SENSING
TUBE NUT
GAS VALVE
SECURING
SCREW (2)
COMBUSTION
CHAMBER
EXTENSION
BURNER
SUPPORT
8.1 Servicing Notes.
(a) To ensure the continued efficient and safe operation of the
appliance it is recommended that it is checked and serviced as
necessary at regular intervals.
The frequency of the servicing will depend upon the particular
installation conditions and usage, but in general once a year
should be enough.
(b) It is the Law that servicing must be carried out by a
competent person.
(c) Remove the fire front.
(d) Refer to the Gas Fire Front Installation and Servicing
Instructions for full details of fire front removal.
(e) After completing any servicing always test for gas soundness
with a suitable leak detection fluid and carry out functional
check on controls.
(f) Unless stated otherwise reassembly of all components is in
the reverse order to that for removal.
(g) The flue blockage safety device MUST NOT be adjusted or
disconnected. If replacing use only the correct and approved
parts.
8.2 Isolation of Services
Having removed the fire front.
Isolate the electrical supply to the back boiler.
Refer to diagram 6.1 to identify the controls.
Turn the gas valve control knob “A” to
“Off” position and turn
the appliance gas service cock to “Fire and Back Boiler Off”, see
diagram 6.2.
8.3 Controls Assembly and Burner.
Disconnect the union at the gas service cock, see diagram 6.2.
If necessary release the control thermostat capillary and the
mains cable from the clips on the combustion chamber extension,
see diagram 5.1.
Disconnect the electrical plug from the gas valve, see diagram
5.2.
Remove the control box securing screw and lift the box upwards
to release, see diagram 5.2.
Disconnect the ignition lead from the piezo unit and remove
from control box, see diagram 9.1.
Temporarily refit control box.
Note: On reconnecting the ignition lead to the piezo unit, it may
necessary to temporally remove the control thermostat, see
Section 9.8. Ensure that the control thermostat capillary is
replaced back in the cutout of the control box, see diagram 5.2.
Undo union nut and disconnect the back boiler lower sensing
tube, undo the four combustion chamber extension securing
screws and slide the extension/burner assembly forward to
remove, see diagram 4.8.
Undo the two screws shown in diagram 8.1, which locate the
burner support to the combustion chamber extension.
Turn the combustion chamber extension/burner assembly
upside down.
Undo the lower sensing tube nut, see diagram 8.2.
Disconnect the ignition lead from the piezo unit.
Undo the two screws shown in diagram 8.2 which locate the gas
valve control to the combustion chamber extension.
8 Servicing
Diagram 8.3
SHAKEPROOF
WASHERS
PILOT SHIELD
MOUNTING
BRACKET
PILOT
SHIELD
NUTS
SCREW
1615
8017
The complete gas carrying assembly can now be lifted clear of
the combustion chamber extension.
Undo the screws on the side of the pilot shield, also the two nuts,
also remove the two shakeproof washers securing the pilot
shield mounting bracket to the burner, see diagram 8.3. Remove
the pilot shield mounting bracket from the studs on the burner
and remove the pilot shield.
Inspect the pilot for damage or blockage, clean or replace flue
blockage safety device as necessary.
Make sure the spark gap is as diagram 8.4.