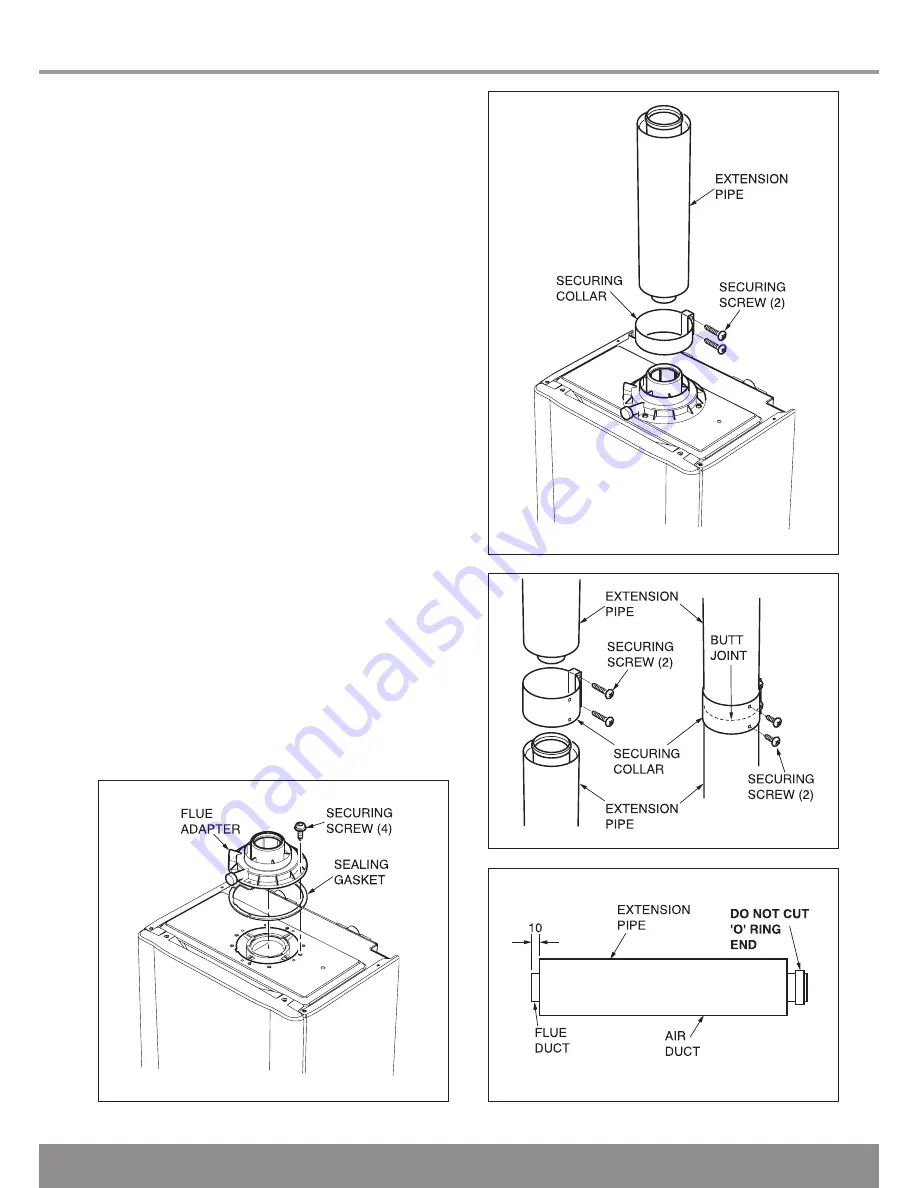
29
10 Vertical Flue - Length, Preparation and Installation
Diagram 10.20
13243
Diagram 10.21
13242
Diagram 10.22
12982
Completion of Installation
With the flue terminal positioned in the roof the length of
the final pipe can be determined. If a telescopic length
cannot be used, then a standard flue length can be cut to
make the correct length. Cut the flue to the desired length
measuring from the ‘O’ ring end and discard the plain end of
the tube. The cuts must be square and made free of burrs
to allow correct assembly. (NOTE: The flue pipe is 10mm
longer than the air pipe), see diagram 10.23. Carefully push
the terminal assembly upwards to allow room for fitting the
final flue piece. Fit a fixing bracket to the terminal assembly.
Pull the terminal assembly down and join to the flue system.
Ensure that the terminal is making a weather tight seal on the
weather collar. Secure the fixing bracket fitted to the terminal
to the roofing struts or a purpose made batton.
Diagram 10.23
12983
Summary of Contents for 18sxi
Page 30: ...30 10 Twin Flue Length Preparation and Installation Diagram 10 24 13226...
Page 46: ...46 14 Fault Finding 13012 Diagram 14 5 CENTRAL HEATING...
Page 48: ...48 14 Fault Finding 13447 Diagram 14 6 Fault Codes continued...
Page 61: ...61 16 Spare Parts Diagram 15 21 13861 1 2 3 4 5 7 9 10 12 6 8 11 13...
Page 63: ...63...