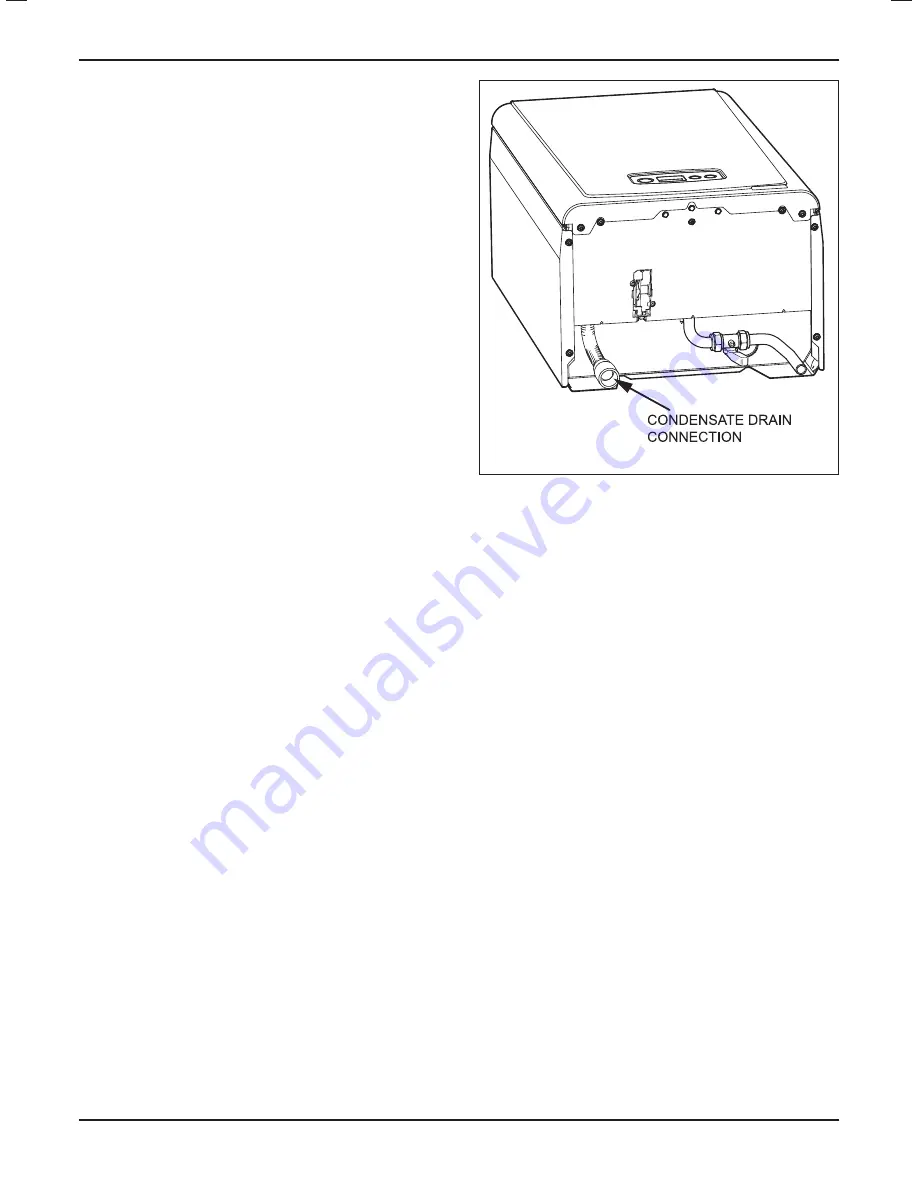
0020107230_04 - 12/14 - Glow-worm
INSTALLATION
- 22 -
9 Condensate Connections
9.1 Condensate Drain Connection
The condensate drain connection, is positioned below the boiler
as shown in diagram 9.1. To discharge condensate to a drain,
the drain pipe should have a fall of a least 44mm/metre (2.5°)
away from the boiler.
Condensate should, if possible be discharged into the
household internal drainage system. If this is not practicable,
discharge can be allowed into the external household drains or
a purpose designed soak away, refer to diagram 9.2.
It is recommended that any external condensate drain pipe is
protected and also preferably of 32mm diameter, to prevent
freezing in adverse weather conditions.
The condensate is discharged periodically in ‘slugs’ by siphonic
action.
It is not necessary to provide air breaks or extra traps in the
discharge pipe as there is already a trap inside the boiler. Fitting
an extra trap may cause the boiler siphon to work incorrectly.
Refer to BS5546 or BS6798 for advice on disposal of boiler
condensate.
14508
Diagram 9.1
Summary of Contents for 12hx
Page 7: ...0020107230_04 12 14 Glow worm TECHNICAL DATA 7 14730 1 Boiler Specification ...
Page 23: ...0020107230_04 12 14 Glow worm INSTALLATION 23 15826 Diagram 9 2 ...
Page 34: ...0020107230_04 12 14 Glow worm MAINTENANCE 34 13917 Diagram 13 4 ...
Page 35: ...0020107230_04 12 14 Glow worm MAINTENANCE 35 13012 Diagram 13 5 ...
Page 50: ......
Page 51: ......