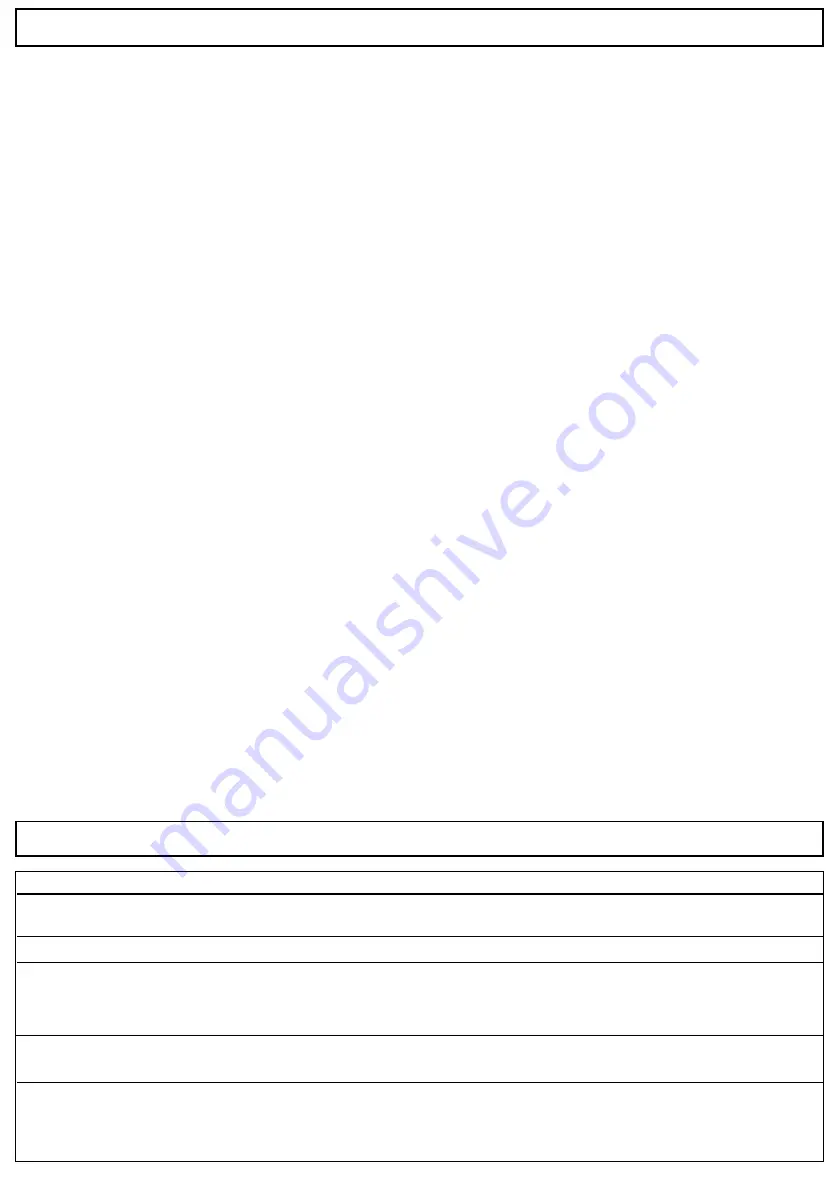
!1% 1% % $ 1 + "4,#%'1% $ ) -.)#
Maintenance and repairs should only be carried out by a
competent person, using genuine GLORIA replacement
parts. If in any doubt, please contact GPS Sprayers Ltd.,
UK Agent for GLORIA. We will be pleased to either
supply parts or service the sprayer for a reasonable
charge.
BEFORE COMMENCING ANY WORK ON THE
SPRAYER, ALWAYS RELEASE ANY REMAINING
PRESSURE FOLLOWING THE INSTRUCTIONS AT
1a & 2a UNDER “OPERATING THE SPRAYER”.
REGULAR EXAMINATION
The entire sprayer should be thoroughly examined at frequent, regular
intervals for evidence of corrosion, breakage or leaks. Any faulty component
found should be replaced before using the sprayer again.
GENERAL LUBRICATION
Occasional lubrication of rubber seals and ‘O’ rings which move, will keep
the sprayer functioning nicely. If parts which employ an ‘O’ ring seal are
removed, a light smear of grease around the outside of the ‘O’ ring, before
the part is replaced, will ensure they slide into place properly to make a
good seal. Suitable lubricants are a light grease or petroleum jelly.
TO LUBRICATE THE PUMP
The piston “O” ring (58), accessed by unscrewing the pump cap (3) at the
top of the pump and withdrawing the piston rod (1). It should be lubricated
with petroleum jelly or a similar light grease, but only on its’ external
perimeter. The frequency of this operation will depend on usage, but
experience will soon tell when excessive friction occurs and the “O” ring is
dragging, making pumping difficult. A little lubricant on the piston rod will
also make pumping easier.
TO LUBRICATE THE TRIGGER VALVE
If the trigger valve becomes stiff or sluggish to operate, it is necessary to
lubricate the valve spindle and its’ ‘O’ rings (66) & (67).
CLEANING THE FILTER IN THE TRIGGER VALVE
There is a filter (44) in the handle of the trigger valve to prevent nozzle
blockages. The filter can be unscrewed from the brass valve body (46) for
cleaning, after first unscrewing the filter barrel (43).
TESTING THE SAFETY RELIEF VALVE
The safety valve should be tested at frequent, regular intervals; every three
months if the machine is used continuously, or every six months if only
used periodically. Proceed as follows.
1)
Ensure that the trigger valve is closed.
2)
Fill the sprayer almost full with water to exclude nearly all the air
inside.
3)
Pressurise the sprayer using the pump until the relief valve
opens. This should occur at between 6 and 7 bars (90-100 psi.)
If the valve is not heard to operate between these
pressures, it must be replaced before the sprayer is used
again.
REMOVING & REPLACING THE FILLER FUNNEL (17)
This is necessary to access the relief valve (70), decompression valve (62),
or pressure gauge (37). After releasing the pressure, replace the pump,
and pour near boiling water into the funnel, allowing it to stand for a couple
of minutes to soften the plastic. With gloves on, tip out the water, remove
the pump and pull off the filler funnel whilst holding the container base with
your feet. To replace, immerse the funnel in very hot water for a few
minutes, then with gloves on and a blunt screwdriver handy, offer it into
position on the container and press it home with your thumbs onto the
container neck. The screwdriver may be necessary to prise the last area of
lip home.
HYDRAULIC TESTING
This test is essential to ensure that the container is in good condition and
has not become weakened by corrosion or damage. Test at least once a
year, more often if the sprayer is used continuously, or with aggressive
chemicals. Test Equipment - It is recommended that an auxillary pump
such as a bucket pump, or boiler test pump is used. A check valve should
be installed in the pump outlet and connected directly to the container under
test, via a suitable hose at leat 10 metres long. A 14 bar pressure gauge
and bleed-off valve should be connected downstream of the check valve.
This valve will allow the container pressure to be released after testing.
Preparation - Carefully remove the funnel, relief valve, decompression
valve and pressure gauge and replace them with test plugs. (Part No. 08-
055 available from GPS Sprayers Ltd.) Connect the 10 metre hose to the
container outlet and remove the sprayers’ pump assembly.
Testing - Completely fill the container with water to exclude all air and
replace the pump assembly. Thoroughly dry the outside of the container
before testing, to allow possible leaks to show up. The container under test
should be placed behind a protective screen and the auxillary pump
operated at the full 10 metres distance provided by the hose. The container
should be pressurised to 10 bars and the pressure maintained for at least
10 minutes. After testing, decompress by opening the bleed-off valve.
IMPORTANT - Failure to remove all air before performing the test
could lead to explosive failure during testing.
Examination - Examine external surface for signs of leaks, especially at
the seams. Remove test hose and empty the container. Remove the
sprayer pump and use a light to examine internal seams for corrosion and
distortion. If there is any doubt, even after the test, as to the soundness of
the container, it should be replaced immediately.
#4,") -% $
SYMPTOM
Pump is difficult to operate, or does
not appear to be creating pressure.
Piston rises after pumping.
Pump is operating, but pressure is
being lost from container.
Container has pressure but will not
spray.
Poor spray pattern, even though all
strainers appear clear and there is
pressure in the container.
POSSIBLE CAUSE
Piston ‘O’ ring (58) is dry or damaged.
Footvalve (60) damaged or dirty.
Pump not screwed in tight.
Pump sealing ‘O’ ring (59) damaged.
Blocked strainer (44) in trigger valve,
or blocked nozzle.
Nozzle partially blocked, or damaged.
REMEDY
Lubricate or replace piston ‘O’ ring.
Replace footvalve assembly.
Tighten pump carefully - BUT DO
NOT OVERTIGHTEN.
Replace pump sealing ‘O’ ring.
Remove and clean the strainer or
nozzle by flushing with water.
Remove and clean, or fit a new
nozzle. Never use a metallic object to
clean the nozzle, it will ruin the spray
pattern and render it useless.
Summary of Contents for Spezial 141 T
Page 1: ......