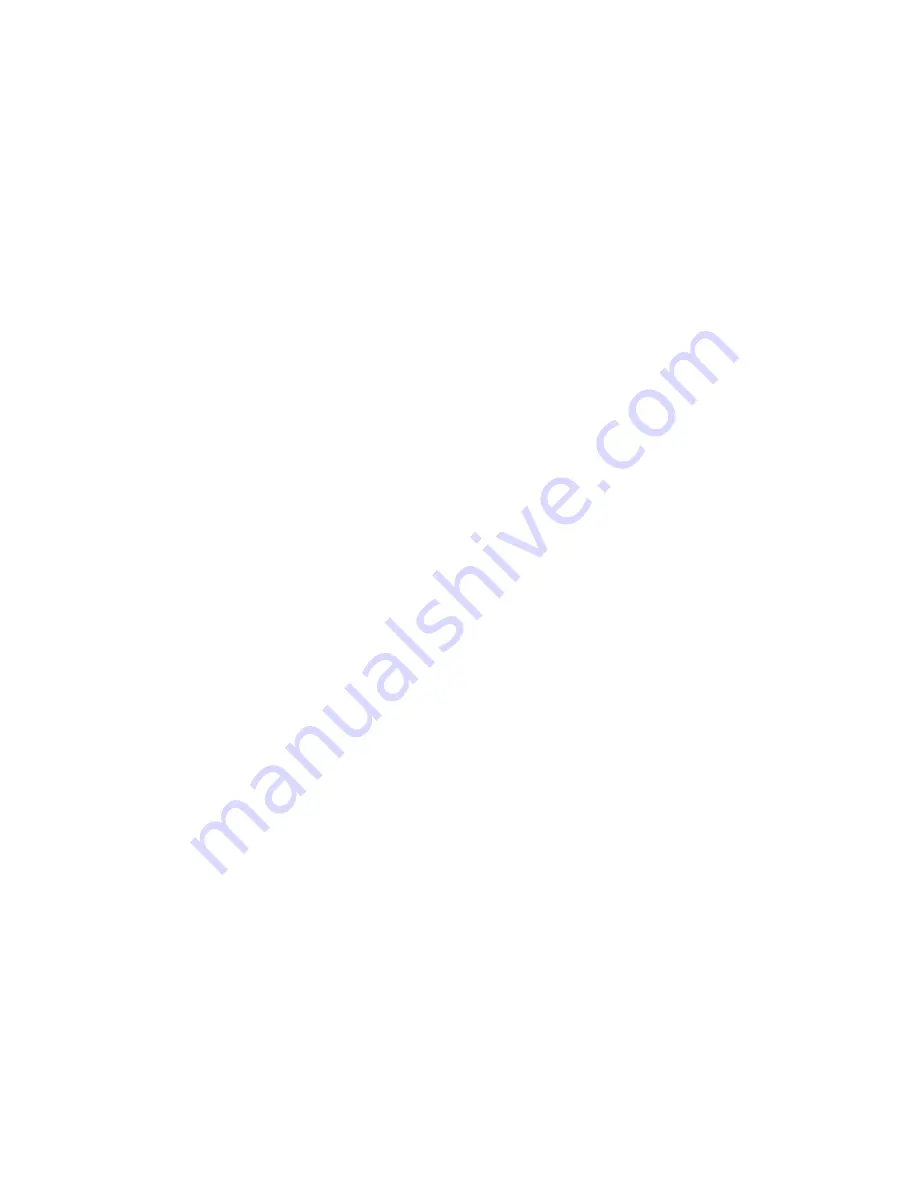
4-6
BL-GL22-1119 - 11-20-2019
3.
Put the controller into the diagnostic mode by
pressing the "Menu Navigation Key" (1,
). Using the Navigation key, select the Faults
menu. Display the Faults menu by pressing the
Right side of the Navigation key. Press the Right
side of the Navigation key again to display the list
of System Faults. The display should indicate "No
Known Faults."
Release the brake by pulling down the steering
arm into the operating position. The controllers
LED should continue blinking a single flash and
the programmer should continue to indicate no
faults. If there is a problem, the LED will flash a
diagnostic code and the programmer will display a
diagnostic message. If you are conducting the
checkout without a programmer, look up the LED
diagnostic code in
.
When the problem has been corrected, it may be
necessary to cycle the brake in order to clear the
fault code.
4.
With the brake released, select a direction and
operate the throttle. The motor should begin to
turn in the selected direction. If it does not, verify
the wiring to the forward/reverse switches and
motor. The motor should run proportionally faster
with increasing throttle. If not, refer to Paragraph
5.
Put the controller into the test mode by using the
Navigation key (1) to select the "Monitor" menu.
Select the Monitor mode by pressing the "Right"
arrow on the Navigation key. Press the Navigation
key "Down" arrow to scroll down to observe the
status of the forward, reverse, brake, emergency
reverse, and mode switches. Cycle each switch in
turn, observing the programmer. Each input
should show the correct state on the programmer.
6.
Check the controller's fault detection circuitry as
described in Paragraph
7.
Take the vehicle off the blocks and drive it in a
clear area. It should have smooth acceleration
and good top speed.
8.
Test the plug braking of the vehicle. The vehicle
should smoothly slow to a stop and reverse direc-
tion, with the audible plugging tone.
9.
Verify that all options, such as high pedal disable
(HPD), static return to off (SRO), and anti-tie-
down, are as desired.
10. Check to see whether the emergency reverse
(belly button) feature is working correctly. Verify
that the circuit is operational by momentarily dis-
connecting one of the emergency reverse wires.
The vehicle should be disabled and a fault indi-
cated.
4-2.5. Diagnostic History
The handheld programmer can be used to access the
controller's diagnostic history file. When the program-
mer is connected to the unit, the error log file is auto-
matically uploaded into the handheld programmer.
To see the present status of the unit, use the Menu
Navigation Key (1,
) to select:
Faults->System Faults.
To access this log, use the Menu Navigation Key to
select:
Faults->Fault History
The faults are shown as a code and descriptive text. If
there are multiple faults, you have to scroll through the
list using the Up and Down Buttons on the Menu Navi-
gation Key
The faults may be intermittent faults, faults caused by
loose wires, or faults caused by operator errors. Faults
such as HPD or over-temperature may be caused by
operator habits or by overloading.
After a problem has been diagnosed and corrected,
clearing the diagnostic history file is recommended.
This allows the controller to accumulate a new file of
faults. By checking the new diagnostic history file at a
later date, you can quickly determine whether the
problem has been completely fixed.
To clear the diagnostic history file, select:
Faults->Clear Fault History.
You will be asked to confirm your actions. Use the
"plus" arrow (+) for yes to clear the menu and the
"minus" arrow (-) (3) to cancel your selection and not
clear the Fault History.
4-2.6. Test the Fault Detection Circuitry
1.
Put the vehicle up on blocks to get the drive wheel
off the ground.
2.
Engage the emergency stop switch and turn off
key switch.
3.
Using an inline fuse holder fitted with a 10 amp
fuse and alligator clips, connect the controller's M
and B- terminals.
4.
Disengage the emergency stop switch and turn
on key switch.
Summary of Contents for 989021
Page 9: ...BL GL22 1119 11 20 2019 2 3 Figure 2 2 Sample of Operator Check List R8549 ...
Page 12: ...2 6 BL GL22 1119 11 20 2019 NOTES ...
Page 18: ...3 6 BL GL22 1119 11 20 2019 NOTES ...
Page 38: ...4 20 BL GL22 1119 11 20 2019 NOTES ...
Page 43: ...BL GL22 1119 11 20 2019 5 5 Figure 5 4 Cap Assembly EF_0007 ...
Page 46: ...6 2 BL GL22 1119 11 20 2019 Figure 6 1 Transmission Motor Brake Assembly EF_0004 ...
Page 48: ...7 2 BL GL22 1119 11 20 2019 Figure 7 1 Transmission Motor Brake Mounting EF_0004 ...
Page 50: ...7 4 BL GL22 1119 11 20 2019 NOTES ...
Page 55: ...BL GL22 1119 11 20 2019 9 3 Figure 9 2 Elevation System Telescopic EF_0016 ...
Page 58: ...10 2 BL GL22 1119 11 20 2019 Figure 10 1 Electrical System Telescopic EF_0011 ...
Page 61: ...BL GL22 1119 11 20 2019 11 1 SECTION 11 OPTIONAL EQUIPMENT N ABL GL22 1119 11 20 2019 ...
Page 62: ...11 2 BL GL22 1119 11 20 2019 NOTES ...
Page 64: ...12 2 BL GL22 1119 11 20 2019 Figure 12 1 Frame System Telescopic Mast EF_0002 ...
Page 66: ...12 4 BL GL22 1119 11 20 2019 Figure 12 2 Caster Assembly EF_0003 ...
Page 68: ...12 6 BL GL22 1119 11 20 2019 Figure 12 3 Transmission Motor and Brake EF_0004 ...
Page 70: ...12 8 BL GL22 1119 11 20 2019 Figure 12 4 Steering System EF_0005 ...
Page 72: ...12 10 BL GL22 1119 11 20 2019 Figure 12 5 Control Head EF_0006 ...
Page 74: ...12 12 BL GL22 1119 11 20 2019 Figure 12 5 Cap Assembly EF_0007 ...
Page 76: ...12 14 BL GL22 1119 11 20 2019 Figure 12 6 Hydraulic System EF_0008 ...
Page 78: ...12 16 BL GL22 1119 11 20 2019 Figure 12 7 Pump and Motor Assembly EF_0010 ...
Page 80: ...12 18 BL GL22 1119 11 20 2019 Figure 12 8 Lift Cylinder EF_0009 ...
Page 82: ...12 20 BL GL22 1119 11 20 2019 Figure 12 9 Telescopic Mast Lift System EF_0016 ...
Page 84: ...12 22 BL GL22 1119 11 20 2019 Figure 12 10 Telescopic Mast Chain Assembly EF_0017 ...
Page 86: ...12 24 BL GL22 1119 11 20 2019 Figure 12 11 Fork Carriage EF_0018 ...
Page 88: ...12 26 BL GL22 1119 11 20 2019 Figure 12 12 Electrical System EF_0011 ...
Page 90: ...12 28 BL GL22 1119 11 20 2019 Figure 12 13 Wiring Harness EF_0012 ...
Page 92: ...12 30 BL GL22 1119 11 20 2019 Figure 12 14 Wiring Cables EF_0013 ...
Page 94: ......