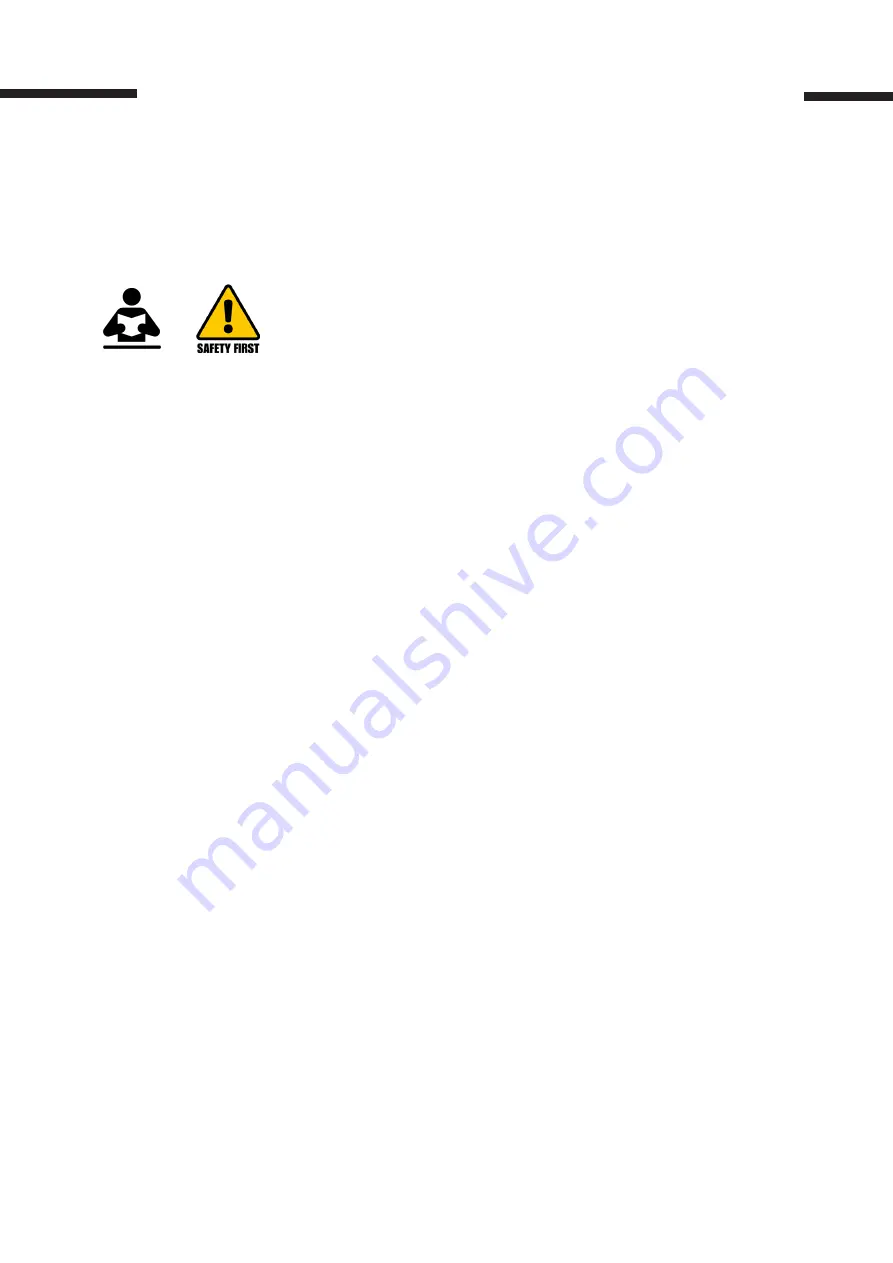
4
SAFETY INFORMATION
PLEASE READ THOROUGHLY AND CAREFULLY. IMPROPER OPERATION OR FAILURE TO
FOLLOW THESE PRECAUTIONS COULD RESULT IN SERIOUS INJURY.
DO NOT operate a damaged hoist.
DO NOT modify the hoist in any way.
DO NOT lift more than max capacity.
DO NOT lift over people, or transport people.
DO NOT wrap chain around load.
DO NOT apply the load to the tip of the hook or the hook latch.
DO NOT operate beyond limits of the load chain travel.
DO NOT leave load supported by the hoist unattended.
DO NOT allow the load chain or hook to be used as an electrical or welding ground.
DO NOT use the hoist’s overload limiting clutch to measure load.
DO NOT use the hoist’s limit switches as routine operating stops.
ALWAYS make sure people remain clear during use.
ALWAYS make sure the load is centered under hoist.
ALWAYS make sure the hoist is securely attached to a suitable support.
ALWAYS take up slack carefully – make sure load is balanced.
ALWAYS stop immediately if the hoist malfunctions and inspect carefully.
ALWAYS check brake function by tightening the hoist prior to each lift operation.
ALWAYS use hook latches and make sure they are closed.
ALWAYS make sure the load is free to move and will clear all obstructions.
ALWAYS avoid swinging the load or hook.
ALWAYS make sure hook travel is in the same direction as shown on the controls.
ALWAYS inspect the hoist regularly and replace damage or worn parts.
ALWAYS lubricate load chain per instructions in this manual.
INSTALLATION & SET UP
Suspending/Mounting the Hoist to Supporting Structure:
1. The structure used to support the hoist must have a load rating equal to or greater than
that of the hoist.
2.
The supporting structure must be able to effectively suspend both the weight of the hoist
and the rated load.
3. Proper installation requires that the upper hook is seated in the center of the hook saddle
and the spring safety latch is completely closed.
4. The hoist must be in the same straight line with the load to avoid side forces.
5. If trolley is mounted to a beam, make sure the beam has end stops to prevent the trolley
running off the end of the beam, causing serious injury.