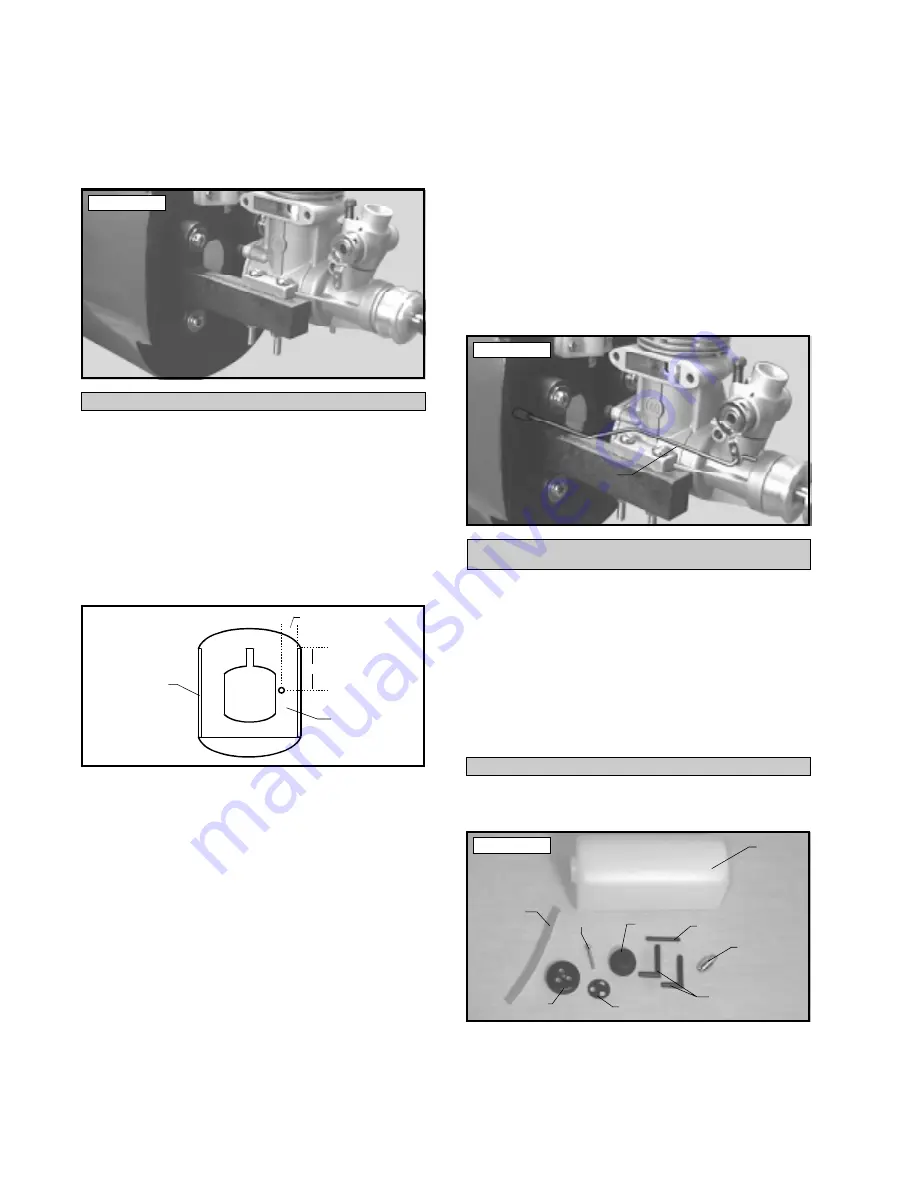
14
q
5) Install the motor mount assembly to the fire-
wall using the four 4mm x 20mm machine screws
and four 4mm flat washers. Tighten the screws com-
pletely to secure the engine mount assembly in place.
See photo # 18 below.
Photo # 18
q
6) Mark and drill a hole through the firewall for
the throttle pushrod housing using a 7/64” drill bit.
Position the hole level with the throttle arm and just
to the outside edge of the motor mounting beam.
q
7) Using a ruler and a pen, measure and place a
mark on the forward bulkhead 1-1/8” down from the
top of the wing saddle and 5/8” out from the inside
edge of the fuselage side. See figure # 11 below.
INSTALLING THE THROTTLE PUSHROD
Figure # 11
q
8)
Using a 7/64 drill bit, carefully drill a hole
through the forward bulkhead at the mark made.
q
9) Slide the 3mm x 250mm pushrod housing
through the hole in the firewall, through the hole in
the forward bulkhead, and into the servo compart-
ment. Leave about 1/4” of the housing extending
beyond the front of the firewall.
q
10) Apply a couple of drops of Kwik Bond Thin
C/A to the pushrod housing where it exits the fire-
wall and where it passes through the forward bulk-
head. This will secure the housing in place.
q
11) Using a modeling knife, cut off the nylon
pushrod housing 1/8” past the back edge of the for-
ward bulkhead.
q
12) Notice one end of the 1.5mm x 250mm push-
rod wire has a Z-Bend premade in it and the other
end is plain. Slide the plain end of the wire into the
end of the pushrod housing at the firewall. Remove
the throttle arm from the engine and attach the Z-Bend
to the hole farthest out in the throttle arm. Reattach
the throttle arm to the engine.
q
13) Using a pair of pliers, carefully bend the
throttle pushrod wire until the wire is aligned with
the throttle arm and does not bind when the throttle
barrel is rotated. See photo # 19 below.
Photo # 19
PARTS REQUIRED
q
{1} 280cc Molded Fuel Tank
q
{1} 4mm x 28mm Nylon Pick-Up Tube
q
{2} 4mm x 28mm Prebent Nylon Vent Tube
q
{1} 3mm x 18mm Self Tapping Screw
q
{1} Length of Fuel Tubing
q
{1} Metal Weighted Pick-Up
q
{1) Nylon Fuel Cap
q
{1} Rubber Stopper
q
{1} Nylon Backplate
STOPPER ASSEMBLY
FUEL TANK
q
1) Identify each of the parts that make up the
fuel tank assembly. See photo # 20 below.
Photo # 20
q
2) Using a modeling knife, cut the silicon fuel
tubing to 3-3/4” long. Connect one end of the tubing
to the weighted fuel pick-up.
1-1/8”
5/8”
Fuselage
Side
Forward
Bulkhead
Pushrod
Wire
Tank
Clunk
Silicon
Tube
Rubber
Stopper
Backplate
Screw
Pickup
Tube
Vent
Tubes
Cap
Summary of Contents for AK-18
Page 26: ...26 ...