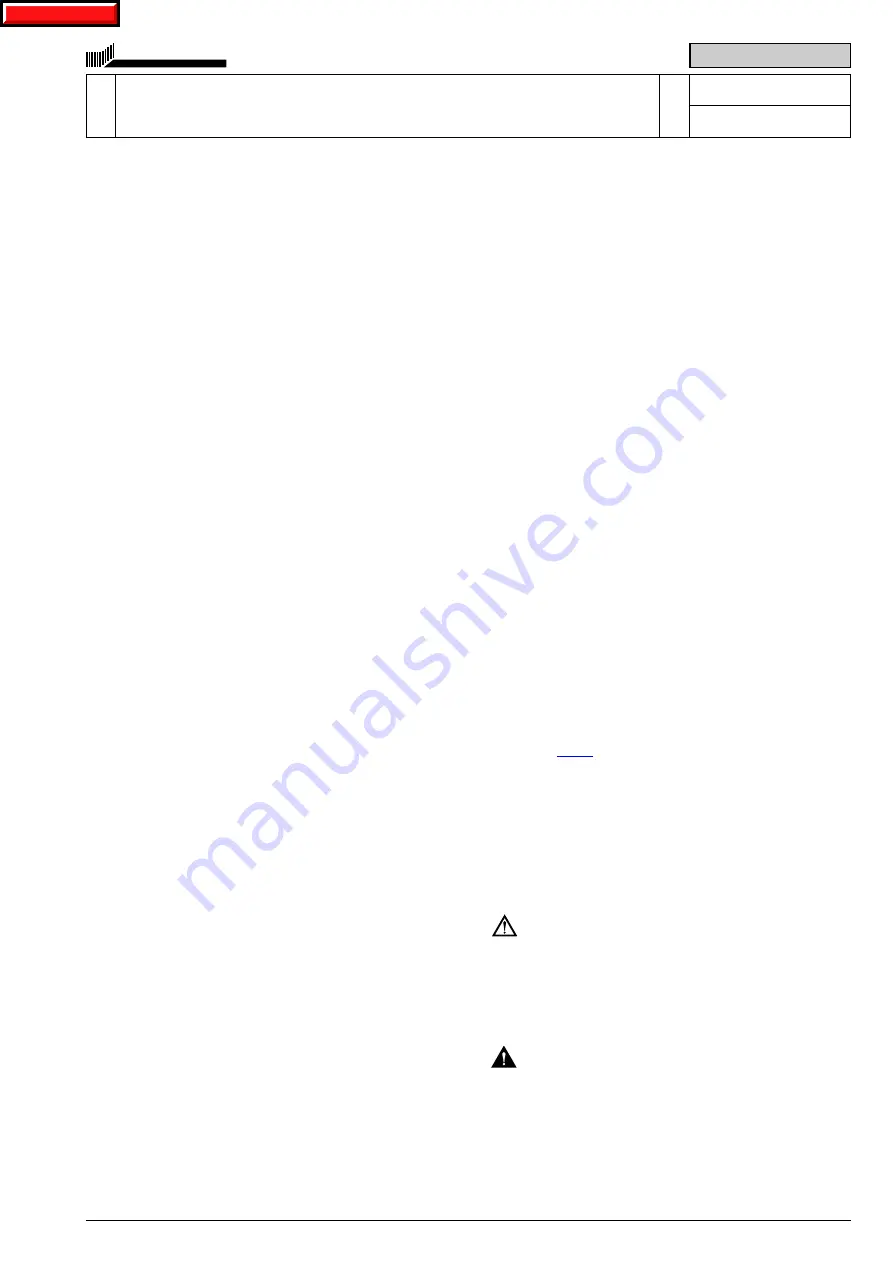
2.1 GENERAL AND SAFETY REGULATIONS
A) Qualification of operators
All maintenance, disassembly and repairs must be
carried out by expert mechanics who are familiar
with all the accident prevention and safety regula-
tions after reading through the procedures in this
manual.
B) Safety measures
All the engines are built in conformity with the
European safety regulations in force.
To maintain initial safety levels in the long term, the
Service Centre should take proactive measures by
making checks whenever possible.
Every time you are asked to service the engine (or
the lawnmower on which it is installed), you should:
1) check:
– that the safety devices function correctly;
– that the guards and covers have not been
removed;
– that the nameplates or specification labels
have not been removed or made illegible,
as they form an integral part of the safety
devices.
2) also:
– make sure the safety devices function cor-
rectly if they have been tampered with or
removed;
– replace ineffective, damaged or missing
guards and covers;
– replace illegible labels;
– do not carry out operations or modifica-
tions on the lawnmower or on the engine
that could affect their performance or lead
to an improper or different use from the
one for which it has been designed and
approved;
– warn the customer that the failure to com-
ply with the above points automatically
voids the warranty and the responsibility of
the manufacturer.
C) Precautions during servicing
The operations described in this manual do not
entail particularly hazardous situations besides the
normal hazard related to mechanical operations
and that can be avoided by taking the necessary
care and attention normally required for this type of
work.
As well as following the usual accident prevention
regulations that apply to most repair shops, we rec-
ommend you:
– disconnect the spark plug cap before servic-
ing;
– protect hands with suitable working gloves,
especially when working near the cutting unit;
– check that you do not cause accidental petrol
leaks or other losses;
– do not smoke when working on the tank or
when handling petrol;
– do not inhale oil or petrol fumes;
– clean up all traces of spilt petrol immediately;
– test the engine in a well-ventilated environ-
ment or where there are adequate exhaust
fume extraction systems;
– do not pollute the environment with oil, petrol
or other waste and dispose of all waste in
accordance with the laws in force.
D) Necessary equipment
All the operations can be carried out with the tools
normally used in a good garage.
Some operations require special equipment and
tools
E) Symbols and terms used for safety purposes
Some paragraphs in this manual are preceded by
symbols which indicate the following:
Operations that should be carried out with
utmost care to avoid impairing the functionality
and safety of the engine and/or lawnmower on
which it is installed.
Operations that should be carried out with
utmost care to avoid injury to operators.
“WARNING” stresses the risk of injury to oneself
and others if instructions and regulations are not
observed.
01/2005
SV 150
2.1
.
0
GENERAL AND SAFETY REGULATIONS
1 / 1
WORKSHOP MANUAL
page
from
2004
to
••••