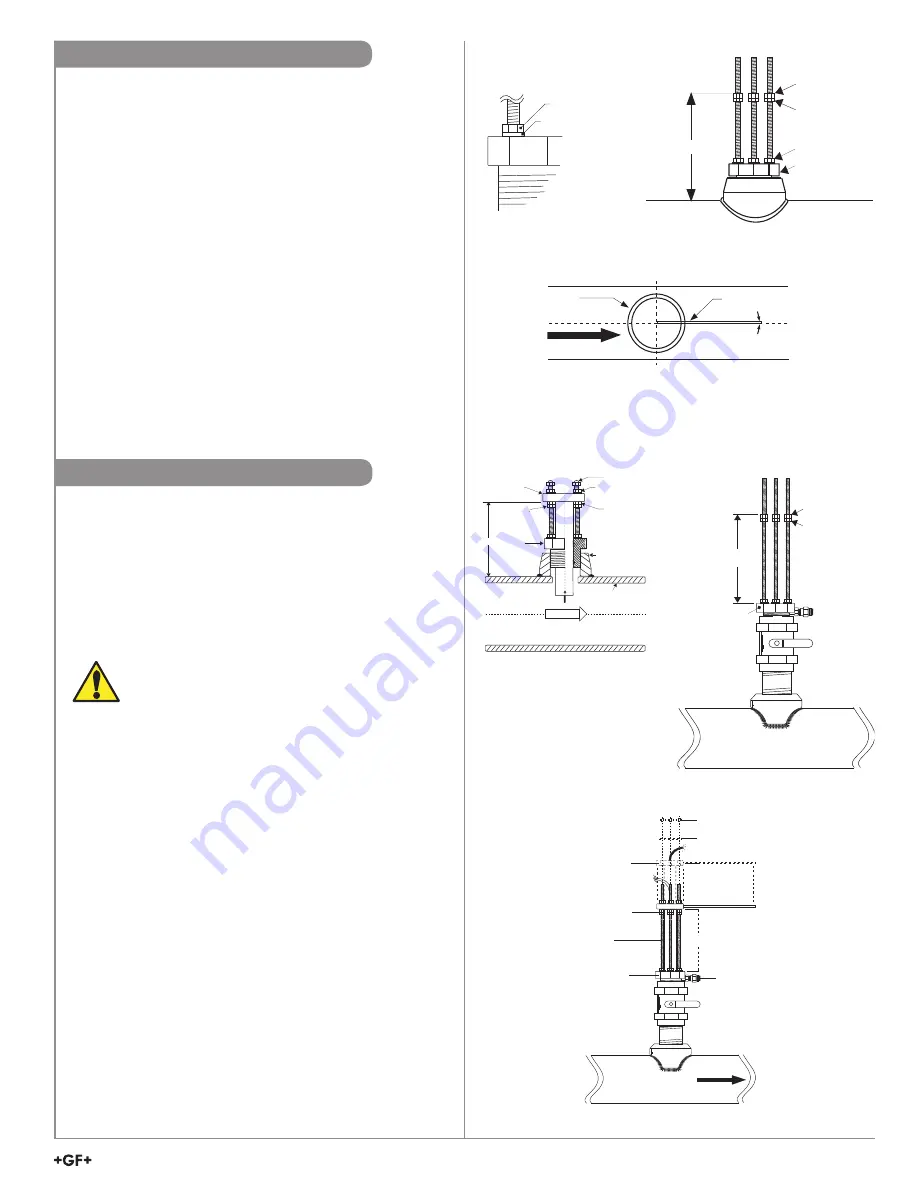
7
Signet 2540 High Performance Flow Sensor
lower hex nut
and jam nuts
sensor flange
18 inch
threaded rods
359 mm (14.14 in)
process pipe (side view)
direction
of flow
alignment rod
Upper hex nuts
(3/16 x 1/4-20)
1/4 in. lock
washers
sensor
fitting
bleed valve
lower hex nuts
(3/16 x 1/4-20)
jam nuts
(5/32 x 1/4-20)
359 mm
(14.14 in.)
sensor
fitting
UNDER PRESSURE!
Fig. 8
Fig. 9
"H"
process
pipe wall I.D.
sensor
fitting
upper hex nuts
& lockwashers
lower hex nuts
jam nuts
sensor
flange
cap nuts
female pipe fitting
FLOW
alignment
rod
sensor
flange
process pipe
(top view)
The flow sensor alignment rod
MUST
be
parallel to the process pipe as shown.
flow direction
Fig. 6
Fig. 7
A.
Thread one hex nut onto each of the three threaded rods
included in package. Install threaded rod with a lock
washer onto the sensor fi tting. Secure rods in place by
tightening each hex nut against the sensor fi tting. (Fig. 4)
B.
Thread one jam nut and lower hex nut onto each threaded
rod so that the top surface of each nut is at the proper "H"
dimension for your pipe. Secure each hex nut with a jam
nut. (Fig. 5)
C.
Insert the fl ow sensor into the sensor fi tting, making
sure the alignment hole on the sensor fl ange is pointing
downstream.
D.
Place the alignment rod in the alignment hole on the
sensor fl ange. Align the fl ange so rod is parallel to the
process pipe. (Fig. 6)
E.
Thread upper hex nuts with lock washers until they contact
the sensor fl ange and tighten. Check for proper "H"
dimension and readjust if necessary. (Fig. 7)
A.
Thread one hex nut onto each of the three threaded rods
included in package. Install threaded rod with a lock
washer onto the sensor fi tting. Secure rods in place by
tightening each hex nut against the sensor fi tting. (Fig. 4)
B.
Thread one jam nut and lower hex nut onto each threaded
rod so that the top surface of each nut is 359 mm
(14.14 in.) from the top surface of the sensor fi tting.
Secure each hex nut with a jam nut. (Fig. 8)
CAUTION: This setting is critical to ensure an
adequate sensor seal and to prevent the rotor
from hitting the isolation valve orifi ce
during installation.
C.
Wipe the sensor body with a dry, clean cloth. Orient the
alignment hole on the sensor fl ange to point
downstream
.
Place the slotted fl ange over the threaded rods. Lower the
sensor into the fi tting until the sensor fl ange rests on the
lower hex and jam nuts.
D.
Secure the sensor with lock washers and upper hex nuts
on the top of the fl ange. Before tightening, align the
sensor fl ange so that the alignment rod is parallel and level
with the process pipe. (Fig. 6 & Fig. 9)
E.
Make sure the bleed valve is closed
(full clockwise position).
sensor fitting
hex nut
Lock washer
Fig. 4
Fig. 5
process pipe
lower hex nuts
(3/16 x 1/4-20)
jam nuts
(5/32 x 1/4-20)
"H"
sensor fitting
hex nut &
lock washer
Standard Sensor Installation
Hot-Tap Sensor Installation