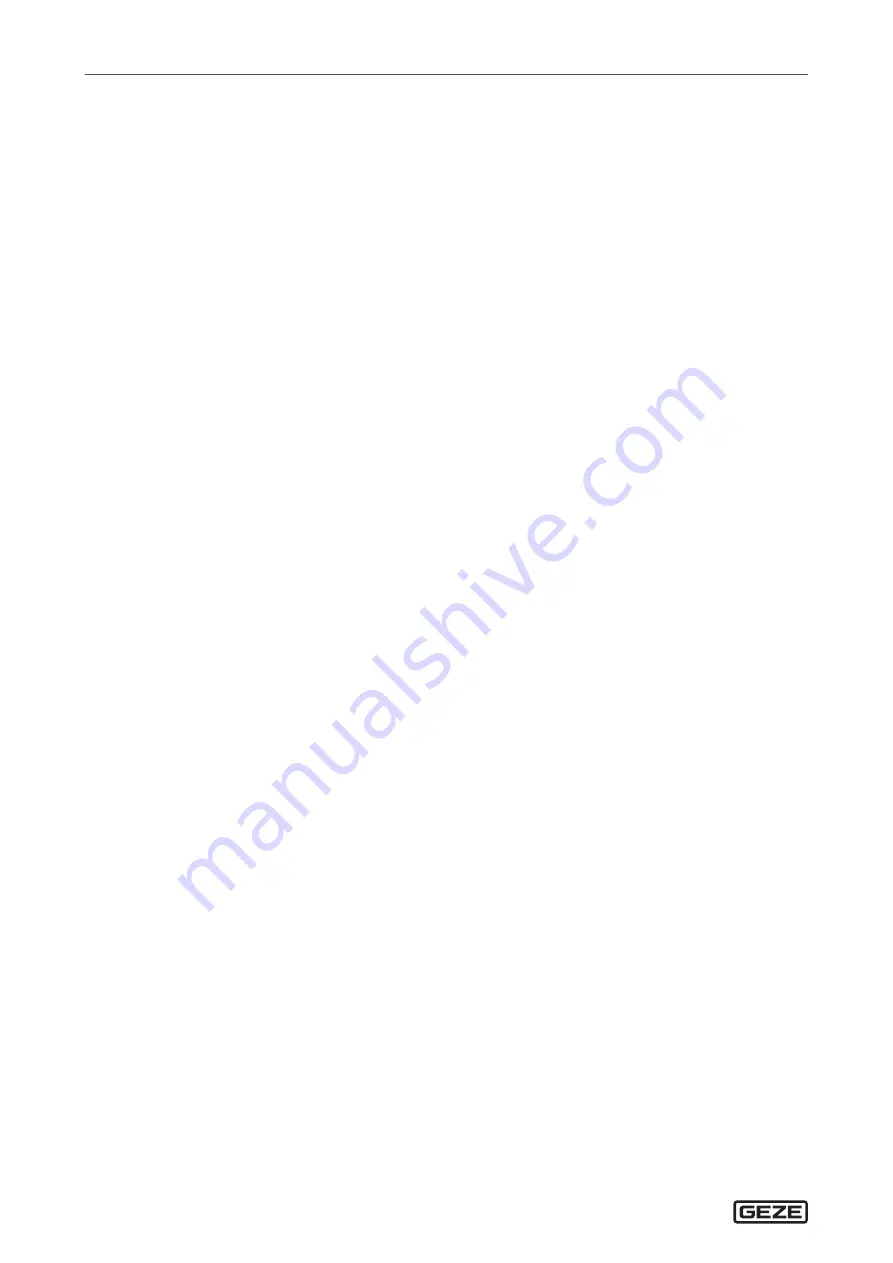
UFO-NT
42
Commissioning and service
20 Commissioning and service
Commissioning and service can be performed using the DPS DPS, the service terminal ST220 or the internal
service keys.
20.1 Commissioning
20.1.1 Requirements
à
Drive
à
attached
à
not taught
à
set to default setting
à
Electrical installation is complete.
à
During commissioning the DPS displays “LE”.
à
When newly teaching the drive: both drives to automatic operating mode.
20.1.2 Carrying out commissioning
X
Check whether the drive works mechanically when de-energised (check by hand).
X
Switch the mains switch on.
X
Set the peripheral equipment before the teaching run.
X
Perform the teaching run as described in chapter 20.2 "Teaching run".
The safety sensor is active due to teaching wall blanking.
X
Check the functionality of the safety sensors.
X
Check other functions.
X
The set static and dynamic forces must be measured
Optional:
The braking force in the disconnected state can be set for different door weights. See chapter 21, "Disconnected
20.2 Teaching run
à
For the teaching run to be carried out, the drive must be completely installed and supplied with voltage.
à
The spring force required must be set before the teaching run, see Powerturn installation instructions.
X
Mechanically set on drive and calibrate on the door leaf.
à
If “Start teaching” is started using the parameter menu (DPS, ST220, service keys), the user has 1 minute to
start the teaching process.
à
If the door is not moved within this time, the drive cancels the teaching run and retains the data previously
stored.
à
In the default setting the safety sensors are configured as active.
à
The teaching run starts and ends in the closed position so that the drive learns the direction of opening/clos-
ing movement properly.
The following points must be observed:
à
Activating the safety sensor within the movement run (part of the teaching process) does not stop the door
leaf. For this reason, only complete a movement run under supervision or with passage safeguard.
à
If the door leaf is blocked within the movement run, fault message 25 is issued and the teaching run must be
repeated.
If a 2-leaf system has to be taught, the “Number of leaves” (EF) parameter must first be installed on both drives:
X
Select the parameter with service terminal ST220 or the DPS DPS and set the value 02 for active leaf and the
value 03 for passive leaf.
X
Connect both drives.
The drive differentiates between two conditions:
à
The drive is situated in the factory setting (factory setting)
untaught
à
Drive is re-taught
Summary of Contents for UFO-NT F
Page 1: ......
Page 7: ...UFO NT 7 Supply terminals 4 Supply terminals DCU800 1 2 24V GND 6 1 RS485 passive leaf 2 FREE ...
Page 79: ...UFO NT 79 ...
Page 80: ......