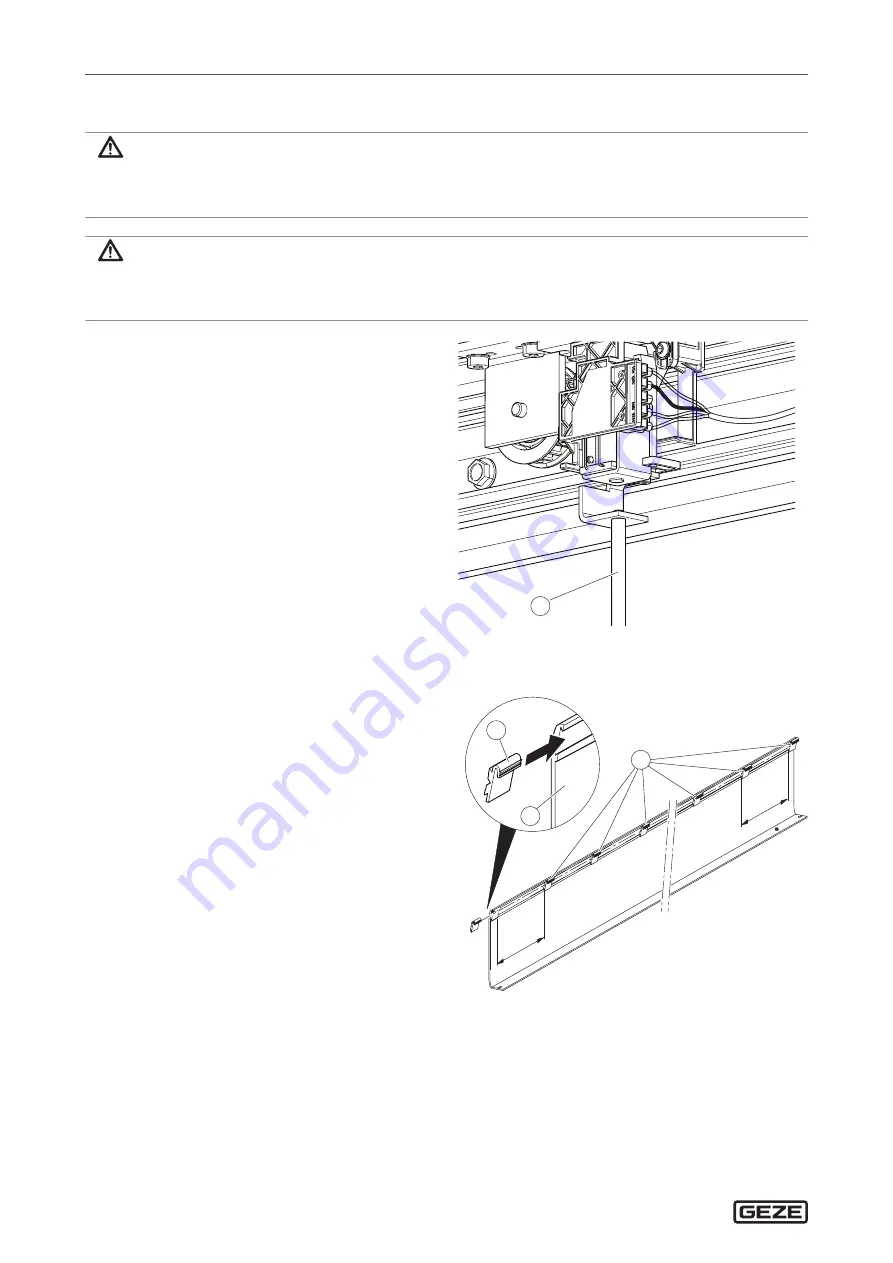
Powerdrive product family
22
Production test and commissioning
6.2 Mounting the cover
WARNING!
Risk of injury!
People can be injured when the cover is handled.
X
Always make sure two people handle the cover.
WARNING!
Risk of injury from falling cover!
X
Make sure that the cover is attached along the entire length of the track.
X
Release the cover carefully and check whether it has been suspended safely.
X
Unscrew the locking pin (1) from the tooth
belt locking mechanism (optional).
6.2.1 Mounting the cover fixing
à
Regardless of the drive length, one cover
fixing (1) must be mounted on each end
of the cover, as well as another fixing offset
by 100 mm.
à
Up to a 3000 mm drive length, a total of
seven cover fixings must be mounted.
à
Above a 3000 mm drive length, a total of
10 cover fixings must be mounted.