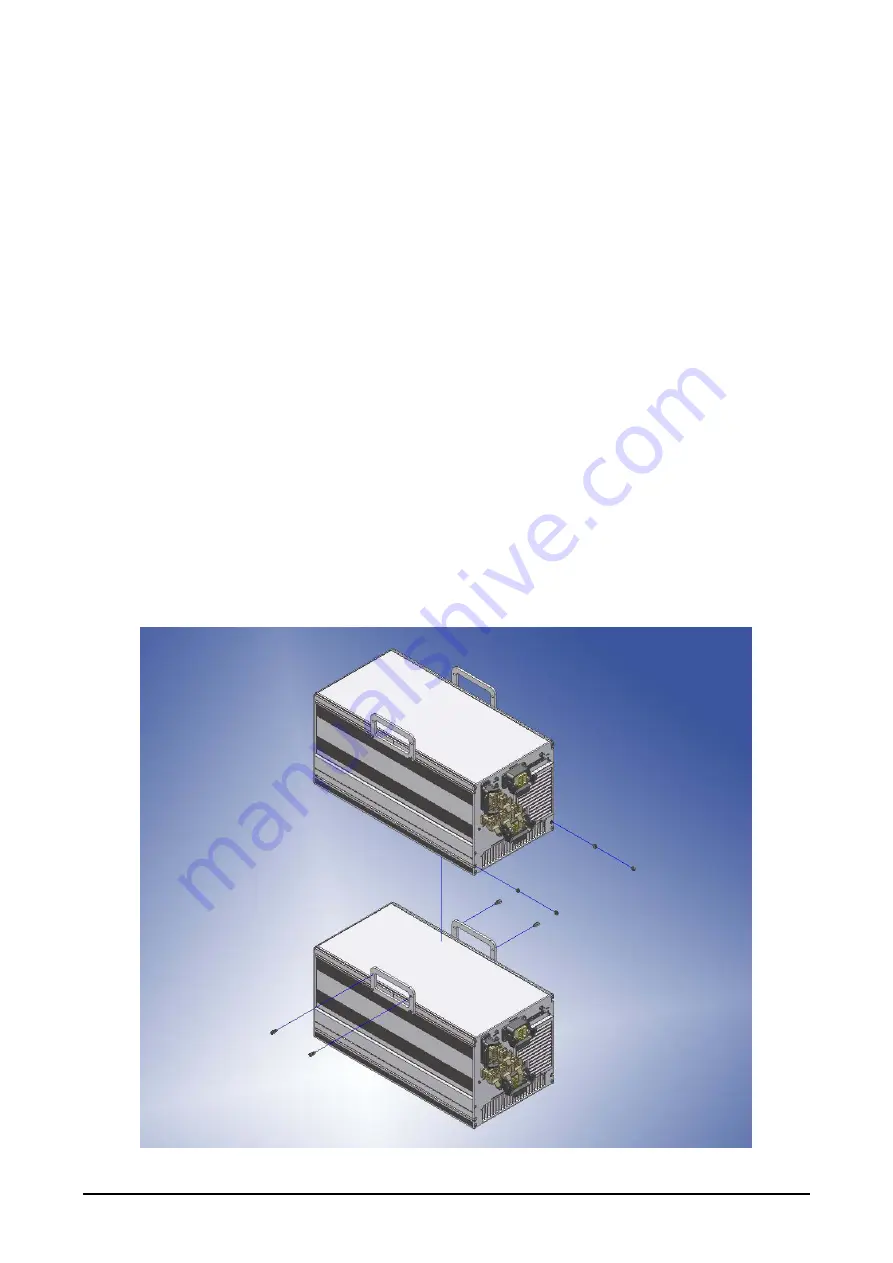
3. Installation
&
Commissioning
During installation and throughout the working life of the UV system, observe the following:
•
Avoid knocking or banging the
e-Brick
or UV dryers
•
Always keep service cables and ducting away from busy areas such as walkways, and
away from potential hazards such as forklifts
•
When moving the equipment, never strain cables or unscrew quick release plugs
•
Apply power to the system only when all connections have been made and tested.
Note!
Illustrations show 9kW
e-Brick
, 12 and 22kW products are installed in a similar manner but
their additional size and mass must be taken in to account.
3.1.
Fixing / anchoring
Depending on the application the
e-Brick
can be freestanding or permanently mounted inside a
cabinet, e.g. an individual print station.
3.1.1. Freestanding applications
For freestanding use, the shelf or surface should be stable and capable of bearing the full
weight of the
e-Brick(s)
and associated cabling. Units may be stacked a maximum of four
high using the location features on the top and base of the housing. To ensure stability the
carry handles act as fishplates to lock the units together, see Figure 2.
GEW UV
e-Brick
installation and operating manual
11 of 49
Figure 2: Stacking