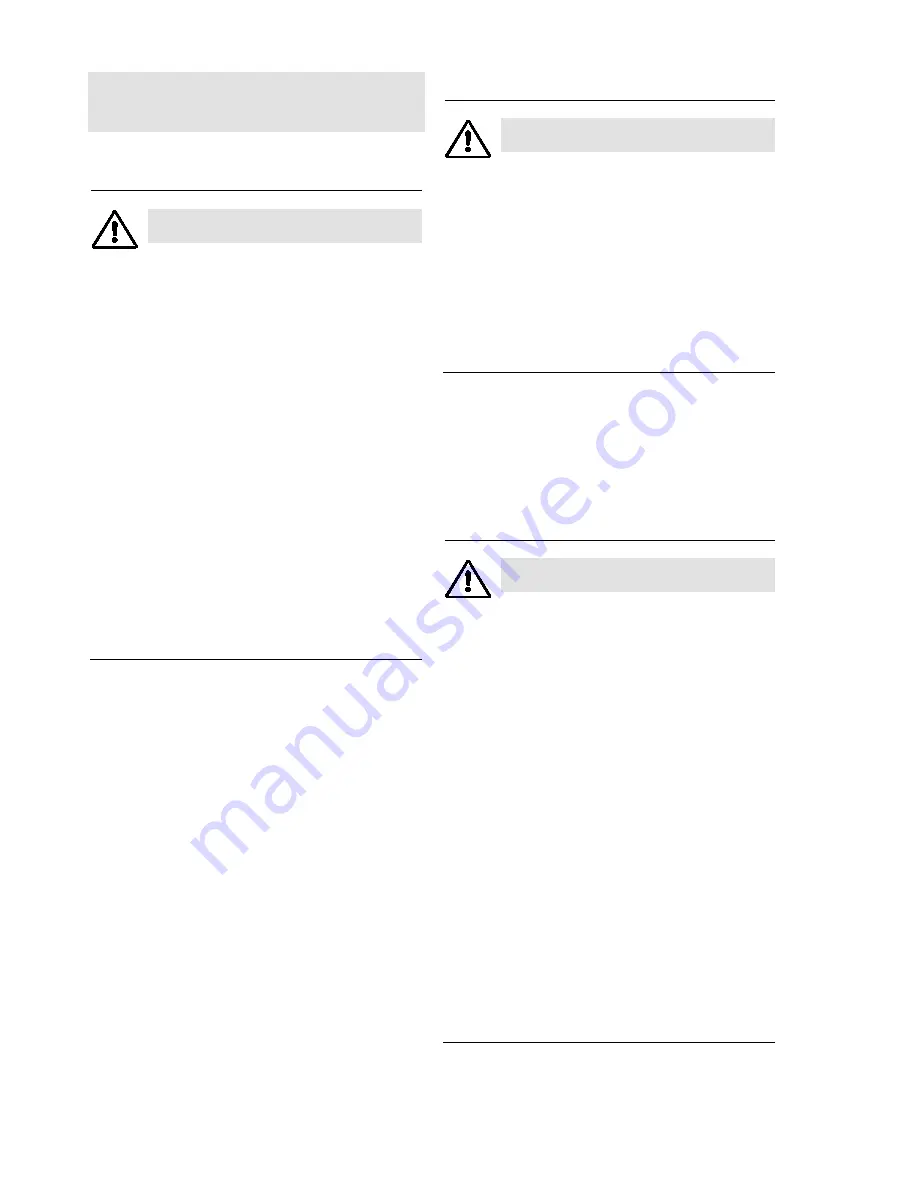
28
Putting the equipment out of
operation
Removing harmful substances
DANGER
If the equipment is used in contaminated
areas there is a risk of severe injuries or
death caused by harmful substances in or
on the equipment.
Only qualified personnel are allowed to
perform work on contaminated
equipment.
Always wear the protective clothing
prescribed for contaminated areas
when working on the equipment.
Make sure that the equipment is
completely decontaminated before
carrying out any service work.
Follow the pertinent instructions for
handling the hazardous substances in
question.
Qualified personnel must have extensive experience
with and a working knowledge of:
pertinent rules and regulations concerning
handling hazardous substances
special regulations for handling the hazardous
substances encountered on site
using the required personal protective
equipment (PPE) and clothing
Caution
Environmental damage may be caused by
poisonous fluid residues.
Before disposing of the equipment
make sure that it is clean and free of
fluid residues.
For the disposal of all materials
observe the pertinent legal regulations
concerning waste disposal.
Remove all residues from the equipment.
For the disposal of all residues observe the
pertinent legal regulations concerning waste
disposal.
Removing the equipment
DANGER
Personnel working on pipes are exposed to
safety risks and may suffer severe injuries,
poisoning or even loss of life.
Make sure that no hot or hazardous
fluid is in the equipment or the pipes.
Make sure that the pipes upstream
and downstream of the equipment are
depressurised.
Make sure that the installation is
switched off and protected against
unauthorised or unintended activation.
Make sure that the equipment and the
pipes have cooled down to room
temperatures.
Wear protective clothing that is
suitable for the fluid and, if necessary,
wear protective gear.
For more information on suitable protective clothing
and safety gear refer to the safety data sheet of the
fluid in question.