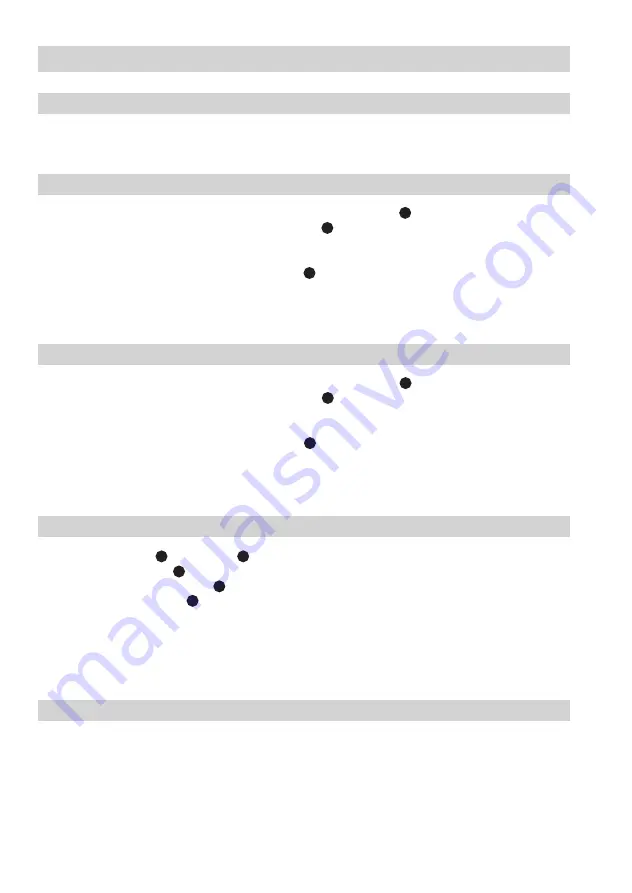
10
1. Remove cover from body , Fig. 2.
2. Lever control unit off its support using a screwdriver, Fig. 3.
3. Turn body, so that arrow points in the desired flow direction.
4. Position control unit on support and fix by two blows using a hammer and
a punch, Fig. 4.
5. Clean seating surfaces of body and cover.
6. Insert new gasket and reassemble body and cover. Tighten body screws in
diagonally opposite pairs with a torque of 35 Nm. After commissioning retighten
body screws.
Change Flow Direction
1. Take care of correct position of installation. Name plate must always be on top.
2. Take care of flow direction. The flow arrow is on the trap body. If necessary,
change direction of flow.
3. Consider space required for opening tap. When the trap is installed a space of
130 mm is required for removing cover .
4. Remove plastic plugs. They are only used as transit protection.
5. Clean seating surfaces of both flanges.
6. Install air trap.
Flanged Trap
A
C
D
1. Take care of correct position of installation. Name plate must always be on top.
2. Take care of flow direction. The flow arrow is on the trap body. If necessary,
change direction of flow.
3. Consider space required for opening trap. When the trap is installed a space of
130 mm is required for removing cover .
4. Remove plastic plugs. They are only used as transit protection.
5. Clean threads of screwed sockets.
6. Install air trap.
Screwed-Socket Trap
D
A
C
C
B
I
A
I
■
Allen key size 8, DIN 911L
■
Torque spanner 20 – 120 Nm, DIN ISO 6789
■
Screwdriver 5.5/125 mm, DIN 5265
■
Punch 120/10 mm, DIN 7250
■
Hammer 500 g, DIN 1041
Tools
Installation
The air trap can – depending on its body design – be installed in horizontal or vertical
pipelines with downward flow.
UNA 13 P
Summary of Contents for UNA 13P
Page 1: ...1 UNA 13P Installation Instructions 810518 00 Air Trap for Compressed Air and Gas ...
Page 3: ...3 TOP Parts Drawings Fig 2 D E C F G H I J A B ...
Page 4: ...4 Maintenance Fig 4 Fig 3 A I I ...
Page 13: ...13 ...
Page 14: ...14 810518 00 300c 1999 GESTRA GmbH Bremen Printed in Germany ...