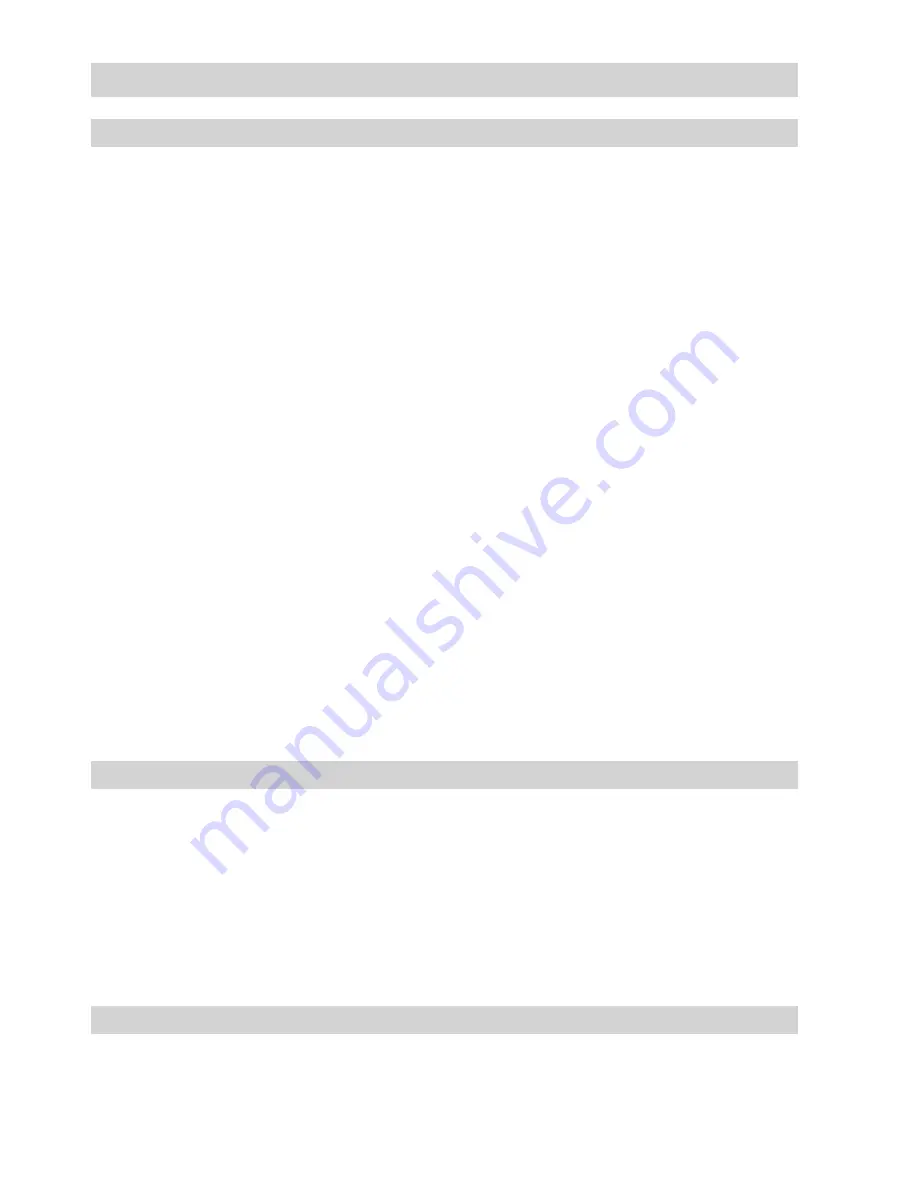
6
Explanantory Notes
- continued -
Function
The control unit LRR 1-40 features the following functions:
2-position controller for the control of the continuous blowdown valve via output relays or via CAN
bus,
3-position stepping controller for the control of the continuous blowdown valve via output relays or
via CAN bus,
Triggering of daily purging pulse (24 h) to actuate the continuous blowdown valve,
De-activation of control function during stand-by operation of steam boiler,
Alarm signal in the event of a malfunction in the conductivity electrode,
MAX limit alarm for conductivity (TDS) limiting,
MIN limit alarm or
Automatic blowdown control with timed actuation of the intermittent blowdown valve,
Analog actual value output (4-20 mA) for external conductivity indication (optional).
For these functions the control unit must evaluate at regular intervals the data telegrams sent off by the
conductivity electrodes LRG 16-40, LRG 16-41, LRG 17-40 and the the actuator EF 1-40 (continuous
blowdown valve BAE 46, BAE 47).
For the visual display of the process and the control of the continuous blowdown valve via CAN bus the
control unit will send a separate data telegram with the following content:
Type of conductivity electrode used with the CAN bus
MIN / MAX limit,
Continuous blowdown valve: setpoint of valve position,
Times for automatic intermittent blowdown control.
Use operating & display unit URB or SPECTOR
control
to commission, operate and monitor the conduc-
tivity electrode LRG, the control unit LRR and the actuator EF.
The control unit can only test the switching of the MIN / MAX output relays.
System components
LRG 16-40
Conductivity electrode LRG 16-40, PN 40, measurement with two electrodes
LRG 16-41
Conductivity electrode LRG 16-41, PN 40, measurement with four electrodes
LRG 17-40
Conductivity electrode LRG 17-40, PN 63, measurement with two electrodes
BAE 46, BAE 47
Continuous blowdown valve with actuator ARIS EF 1-1 or EF 1-40
Design
LRR 1-40
Plug-in unit in plastic case for installation in control cabinets. The terminals are externally accessible.
For mounting on a standardised supporting rail TS 35 x 15 DIN EN 50022.
External dimensions: 73 x 100 x 118