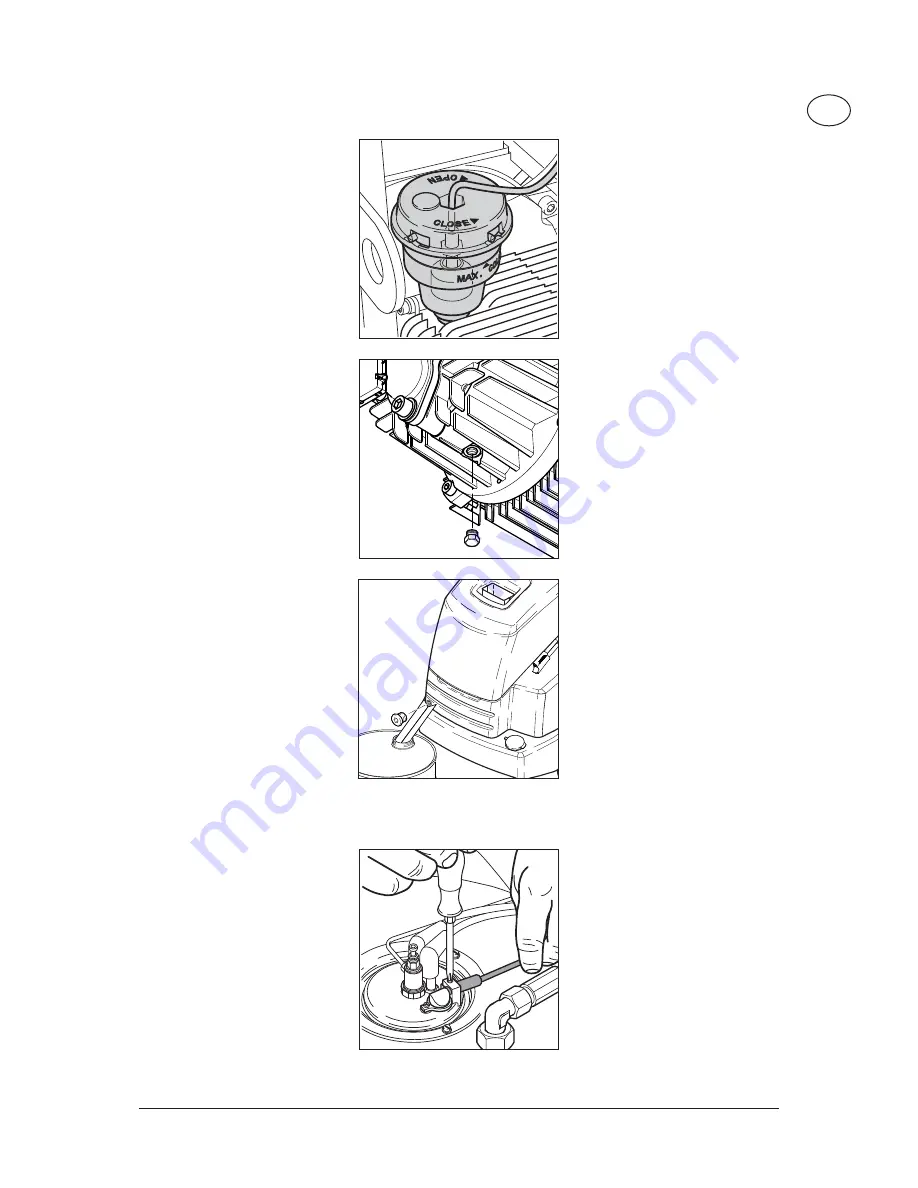
21
NEPTUNE 7 FA
1)
Options / model variants
Original instructions
EN
1. Check color of pump oil.
If the oil has a grey or white
shade, change the oil.
2. Top off oil level with fresh
oil if necessary.
Oil type see chapter 9.4 Techni-
cal Data.
1. Unscrew the oil drain plug
and drain oil into a suitable
container.
2. Check that the drain plug
gasket is in place and rein-
stall drain plug.
3. Fill pump with proper grade
and amount of oil.
Oil grade and capacity see
chapter ‘9.4 Technical Data’.
1. Prepare a container which
is capable of containing the
amount of fuel remaining in
the tank.
2. Place drain channel be-
neath the drain plug.
3. Remove the drain plug and
drain the fuel into the pre-
pared container carefully
not to spill fuel oil.
4. Check that the drain plug
gasket is in place and rein-
stall drain plug.
5. Check tank and plug for
leaks.
1. Remove the sensor and
clean with a soft cloth.
2. Confirm that the sensor is
correctly seated when rein-
stalling.
7.3.3
Checking the pump
oil quality
7.3.4
Changing the pump
oil
7.3.5
Emptying the fuel oil
tank
7.3.6 Flame
sensor