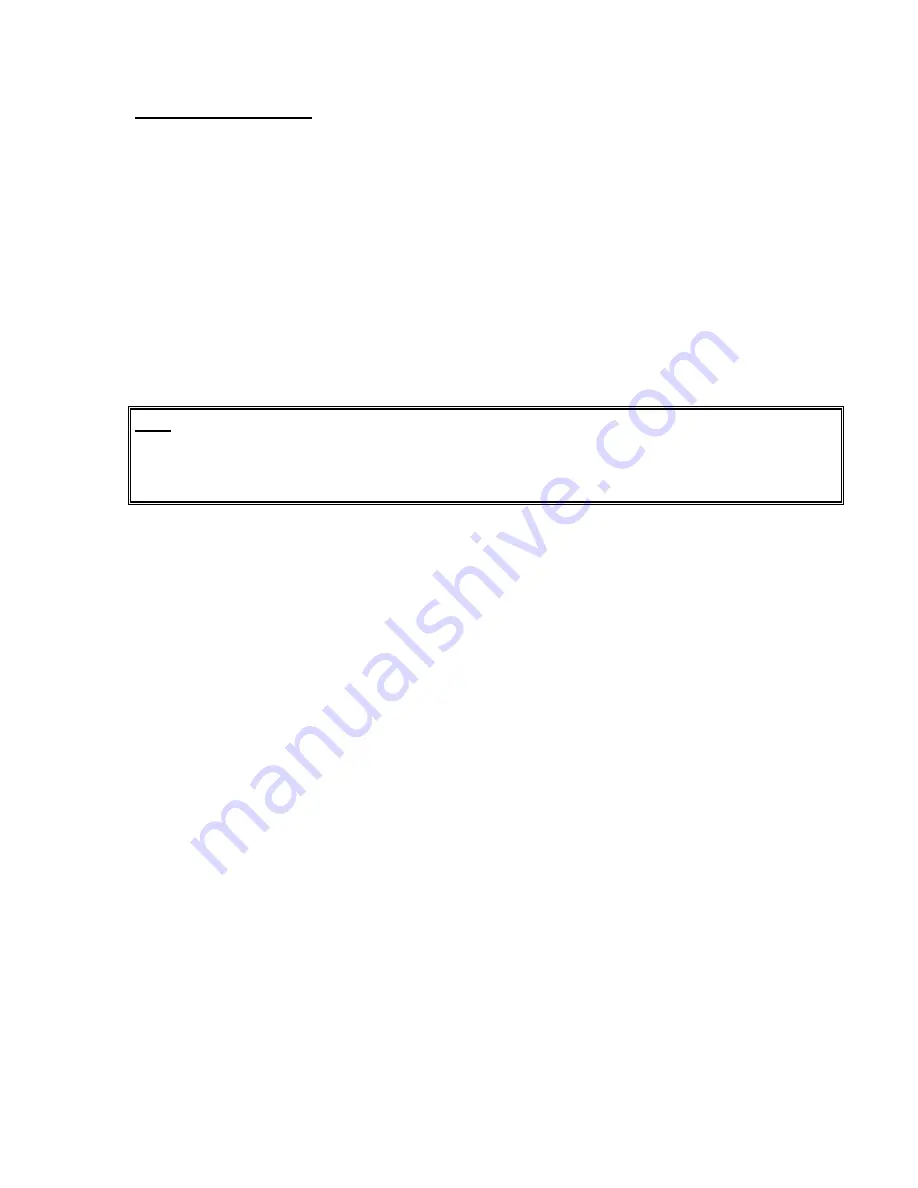
3
2. INSTALLATION
2.1 Preliminary Tests
Prior to installation, the sensors need to be checked for proper operation. Each tilt sensor is
supplied with a calibration report, which shows the relationship between readout digits and
inclination. The tilt sensor electrical leads (usually the red and black leads) are connected to a
readout box (see Section 3 for readout instructions) and the current reading compared to the
calibration readings. After backing off the clamp screw three full turns, carefully hold the sensor
in a vertical position and observe the reading. It will take a few seconds to come to equilibrium
and the sensor must be held in a steady position. The readings should be in the range of the
factory reading, but will vary according to inclination. The indicated temperature should be close
to ambient.
Note: Vibrating wire tilt sensors are shock sensitive and severe shocks can cause a
permanent offset or even break the suspension. (The unit will not survive a two foot (.5 m)
drop onto a hard surface.) When transporting the tiltmeter tighten the locking clamp
screw.
Checks of electrical continuity can also be made using an ohmmeter. Resistance between the
gage leads should be approximately 180
Ω
, ±10 ohms. Remember to add cable resistance when
checking. Remember to add cable resistance when checking. The resistance of 22 AWG stranded
copper leads is approximately 14.7
Ω
per 1,000 feet (48.5
Ω
per km), multiply this factor by two
to account for both directions.
Resistance between the green and white leads varies by temperature. Using Table 4 in Appendix
C, convert the resistance to temperature and compare the result to the ambient temperature.
Resistance between any conductor and the shield should exceed two megohms.
Summary of Contents for 6350
Page 2: ......
Page 4: ......
Page 24: ...18 APPENDIX A SAMPLE CALIBRATION REPORT Figure 11 Sample Model 6350 Calibration Report ...