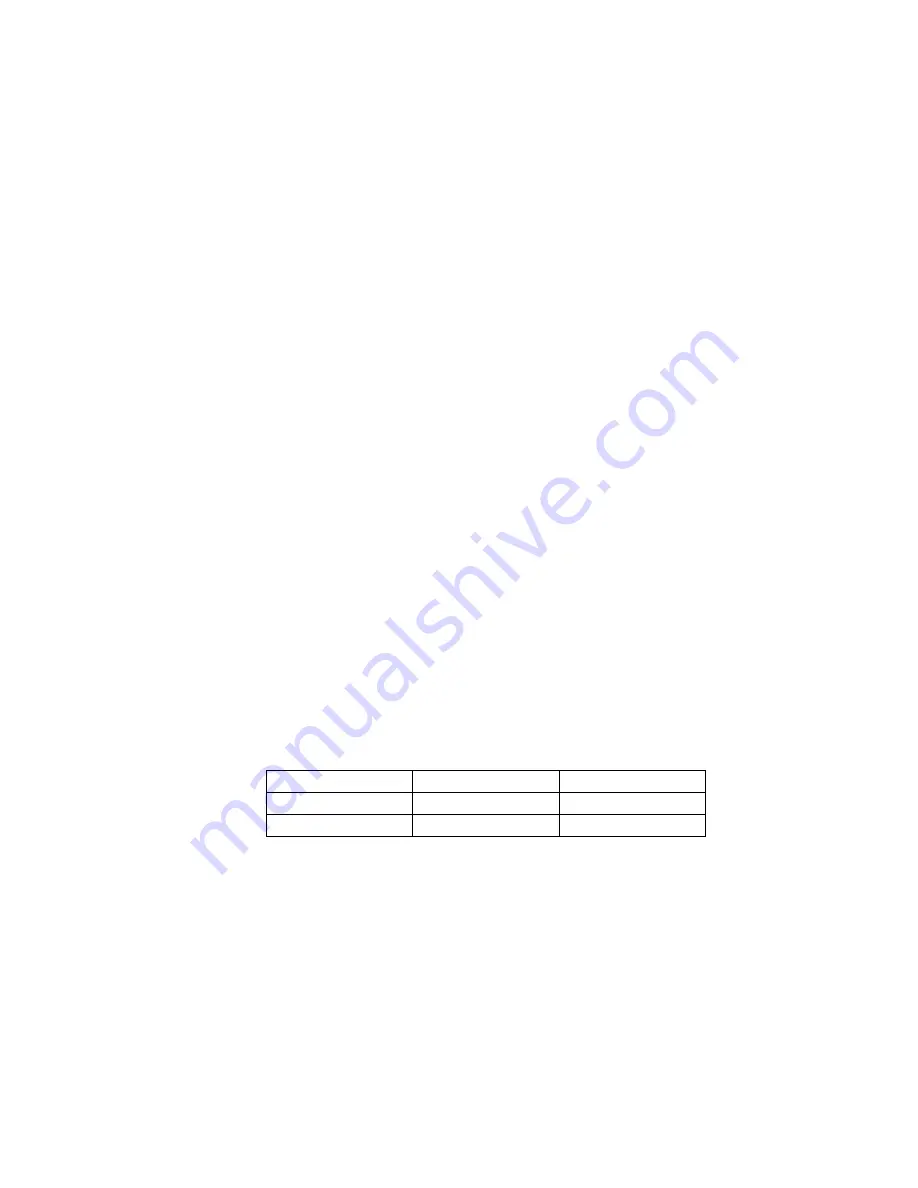
11
or the temperature changes are large (>10° C) corrections can be applied by applying the
following equation:
Dcorrected = F(R
1
- R
0
) + K(T
1
- T
0
)G
Equation 3 - Thermally Corrected Displacement Calculation
Where;
F
is the linear gauge factor (in mm or inches per digit) from the
model 4427 calibration
report
supplied with the equipment. (Figure 9 in Appendix C.1 shows a typical model
4427 long range displacement transducer calibration report.)
R
1
is the current reading.
R
0
is the initial reading.
T
1
is the current temperature ºC.
T
0
is the initial temperature ºC.
K is the thermal coefficient (see Equation 4).
G
is the linear gauge factor (in mm or inches per digit) from the
model 4400 calibration
report
supplied with the equipment. (Figure 10 in Appendix C.2 shows a typical model
4400 displacement transducer calibration report.)
Tests have determined that the thermal coefficient, K, changes with the position of the
transducer shaft. The first step in the temperature correction process is determination of
the proper thermal coefficient based on the following equation:
K = MR
1
+
B
Equation 4 - Thermal Coefficient Calculation
Where;
R
1
is the current reading.
M is the multiplier from Table 1.
B is the constant from Table 1.
Model:
4427-1-1M
4427-1-2M
Multiplier (M):
0.000369
0.000376
Constant (B):
0.572
0.328
Table 1 - Thermal Coefficients
5.2.2 The Extension Cable
The elongation of the extension cable (stainless steel aircraft cable) under ambient
temperature rises can be compensated by using the following compensation factor:
+ L x 17.3 x 10
-6
(T
1
-T
0
) inches or mm
Equation 5 - Elongation Correction
Where;
L is the length of the aircraft cable in inches or millimeters
T
0
is the initial temperature reading in degrees Centigrade.
T
1
is a subsequent temperature reading in degrees Centigrade.