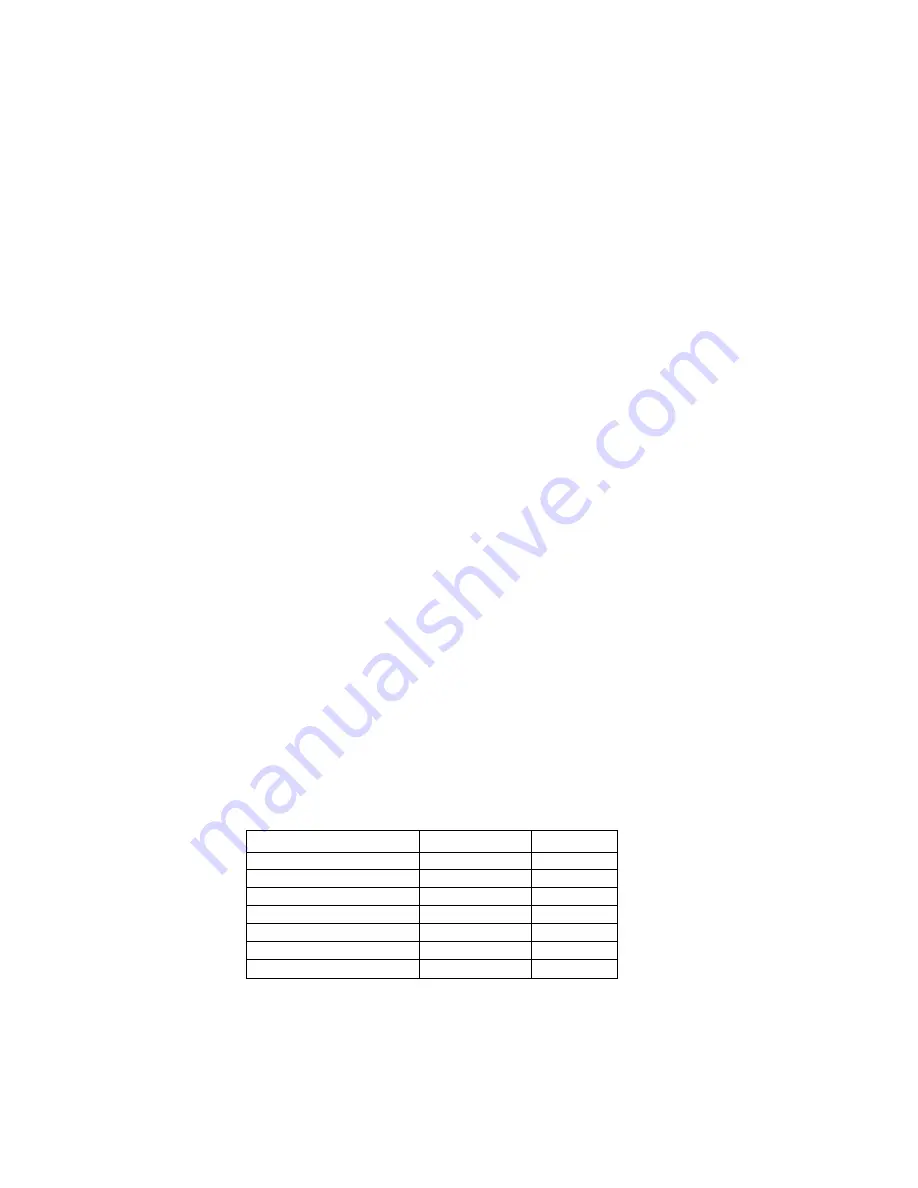
10
4.2 Temperature Correction
In most cases, temperature correction is not necessary, since the Model 4425 Vibrating Wire
Convergence Meter has a very small coefficient of thermal expansion. However, if maximum
accuracy is desired or the temperature changes are extreme (>10° C) corrections may be applied.
The following equation applies:
Dtemperature = (T
1
- T
0
) (K + LK
R
+ K
T
)
Equation 3 - Temperature Correction
Where;
Dtemperature is the deformation due to temperature change.
T
1
is the current temperature in degrees C.
T
0
is the initial temperature in degrees C.
K is the thermal coefficient of transducer, see Equation 4.
K
R
is the thermal coefficient of the connecting rod, see Table 4.
L is the length of the connecting rod, in millimeters or inches.
K
T
is the thermal coefficient of the turnbuckle/spring, 0.0007" or 0.0178 mm/°C.
Tests have determined that the transducer thermal coefficient,
K
, changes with the position of the
transducer shaft. The first step in the temperature correction process is determination of the
proper transducer thermal coefficient based on the following equation:
K = ((R
1
×
M)
+
B)
×
G
Equation 4 - Transducer Thermal Coefficient Calculation
Where;
K is the transducer thermal coefficient.
R
1
is the current reading in digits.
M is the multiplier from Table 3.
B is the constant from Table 3.
G is the calibration factor from the supplied calibration report.
Model
Multiplier Constant
4425-12 mm / 4425-0.5"
0.000375
1.08
4425-25 mm / 4425-1"
0.000369
0.572
4425-50 mm / 4425-2"
0.000376
0.328
4425-100 mm / 4425-4"
0.000398
0.0864
4425-150 mm / 4425-6"
0.000384
-0.3482
4425-200 mm / 4425-8.0"
0.000396
-0.4428
4425-300 mm / 4425-12"
0.000424
-0.6778
Table 3 - Transducer Thermal Coefficient Calculation Constants
Summary of Contents for 4425
Page 2: ......
Page 4: ......
Page 27: ...21 APPENDIX D EXAMPLE CALIBRATION REPORT Figure 13 Typical 4425 Calibration Report ...