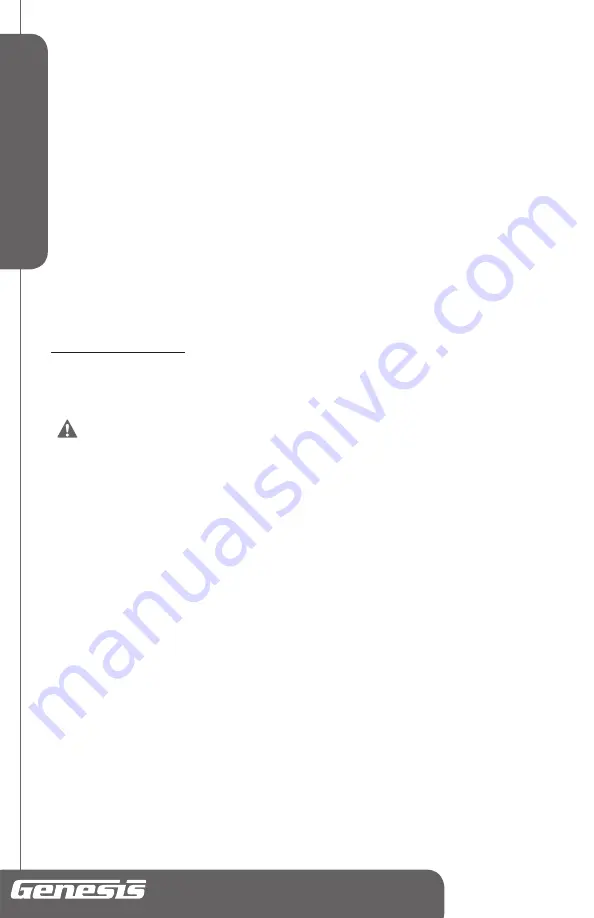
English
1/2" Impact Wrench Kit
Operator’s Manual GIW3075K
A 3/8” bolt generally requires two seconds of impacting time, while a 5/16” bolt will require only one second.
However, any contamination on the bolt or under the bolt head will affect impacting time. Additionally, fasteners
of the same diameters but with different lengths will require different impacting times to achieve the same
degree of tightness.
On work where correct torque is critical or a gasket is involved, it is best to run down each fastener lightly and
then complete the tightening process with an accurate hand torque wrench.
“BREAKING LOOSE” FASTENERS
This procedure may be used cautiously to remove the occasional fastener that has become “frozen”, usually due
to corrosion. Additionally, this procedure assumes that the fastener uses standard threads (clockwise to tighten,
counter-clockwise to loosen).
1. Spray the frozen fastener with penetrating oil designed to dissolve the corrosion causing the nut and/or bolt to
be “frozen”. follow the directions provided by the penetrating oil manufacturer.
2. Quickly press the rocker switch trigger up and then down. Rapidly changing the rotational direction of the tool
will help break the nut or bolt loose allowing its removal
3. use this technique sparingly and for only a few moments duration as it will cause motor wear with possible
premature failure. Keep in mind that in some cases the only way to successfully remove a nut or bolt is cutting
them off with the appropriate saw or cutting torch.
MAINTENANCE
CLEANING
Avoid using solvents when cleaning plastic parts. Most plastics are susceptible to damage from various types of
commercial solvents and may be damaged by their use. use clean cloths to remove dirt, dust, oil, grease, etc.
WARNING:
Do not at any time let brake fluids, gasoline, petroleum-based
products, penetrating oils, etc., come in contact with plastic parts. Chemicals can
damage, weaken or destroy plastic which may result in serious personal injury.
electric tools used on fiberglass material, wallboard, spackling compounds, or plaster are subject to accelerated
wear and possible premature failure because the fiberglass chips and grindings are highly abrasive to bearings,
brushes, commutators, etc. Consequently, we do not recommended using this tool for extended work on these
types of materials. However, if you do work with any of these materials, it is extremely important to clean the tool
using compressed air.
LUBRICATION
This tool is permanently lubricated at the factory and requires no additional lubrication.