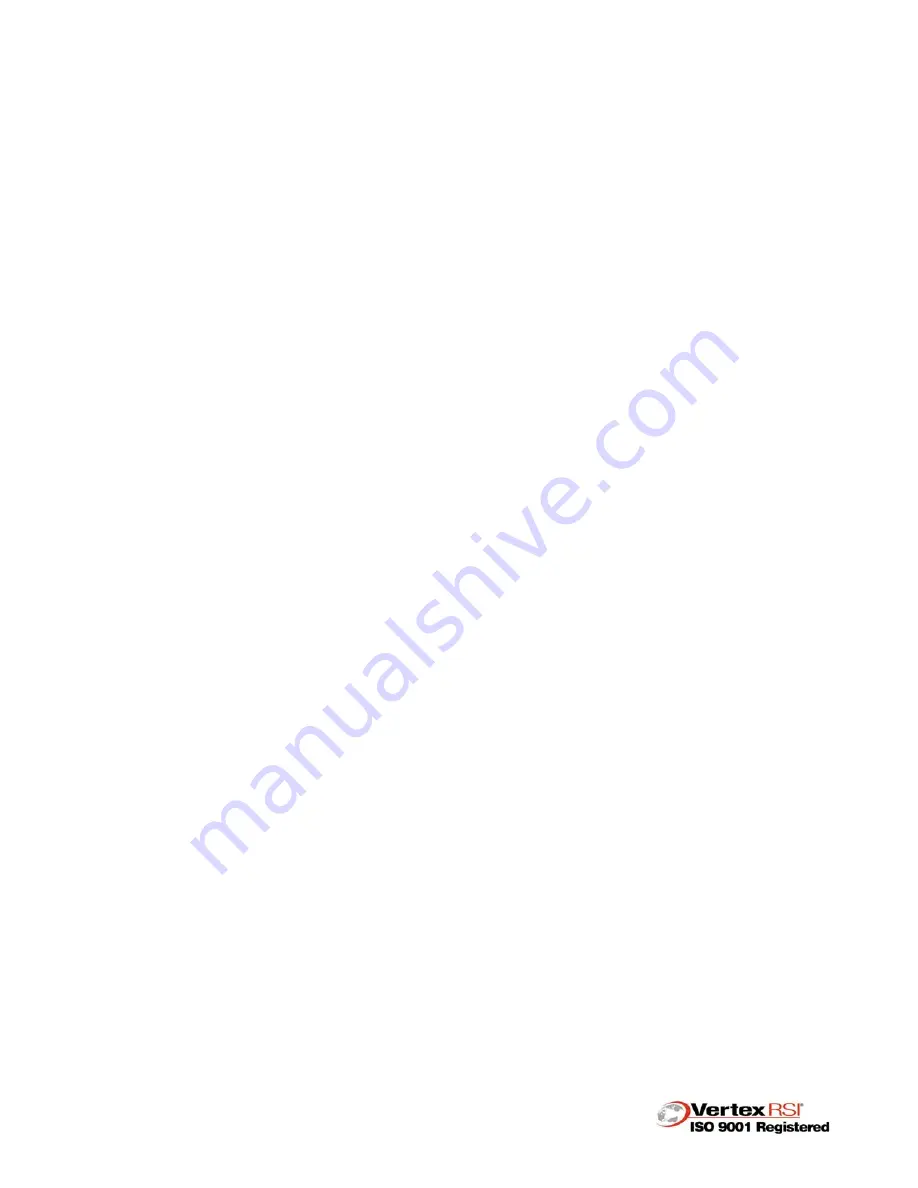
600-1152A 4
2.7
Limit Switches
Limit switches are provided on the elevation and the azimuth ax’es to prevent structural
and/or electrical damage due to excessive rotation (overtravel) of the system. The limit
switches are activated by tripping the lever arm against an adjustable stop.
2.8
Angular Position Indication
Angular position is indicated by two size 11 (standard) transducers, size 20 (high
accuracy) transducers, or optical encoders. Position indicators are Control System and
application dependent. Refer to the PROJECT CONFIGURATION for the specific
Control System utilized. One transducer is mounted on each axis (azimuth and
elevation). Their electrical outputs are monitored as digital readouts integral with the
antenna position controller.
Additional optional position indication is provided by direct reading mechanical vernier
and protractor arrangements. These are available on both the azimuth and the elevation
axis. The protractor and the vernier are installed so that the scribed mark at zero (0) on
the protractor and the similar mark at zero (0) on the vernier are precisely aligned when
the antenna is at zero look angle (azimuth or elevation). For any rotation about either
axis, the mark at zero (zero mark) on the vernier will line up with the antenna look angle
(in degrees) on the protractor. When the zero mark on the vernier falls between two
degree marks on the protractor, the vernier may be read to determine the look angle to
the nearest five (5) minutes of arc. For example, if the zero mark on the vernier falls
between 23 degrees and 24 degrees on the protractor, and the mark at 15 on the vernier
is aligned with any mark on the protractor, the look angle is 23 degrees and 15 minutes
(23 and 15'). Note that while the vernier can be read on either side of the zero mark, it
should always be read in the direction of the increasing angle on the protractor.
2.9
Reflector Backup Structure
The reflector backup structure is comprised of 24 steel radial rib trusses emanating from
a center hub structure. Interconnecting hoop members are provided to furnish the
structure with maximum stiffness capability.
2.10
Reflector Panels
Thirty-six trapezoidal aluminum reflector panels are provided with each reflector. The
panels are designed to meet the stiffness and load requirements for the overall
specification. The panels will support a carefully placed 300-pound soft-bottom shoe
load without permanent deformation of surface accuracy
2.11
Subreflector Support Assembly
The subreflector support structure consists of four spars fastened together by an apex
assembly to form a space truss protruding from the main reflector backup structure. The
spars have been structurally optimized to minimize the RF blockage and relative
displacements between the subreflector, feed launcher, and main reflector axis.
Summary of Contents for SATCOM Technologies KX 120
Page 3: ......
Page 20: ...Figure 1 Antenna Lubrication Points 600 1152A 11...