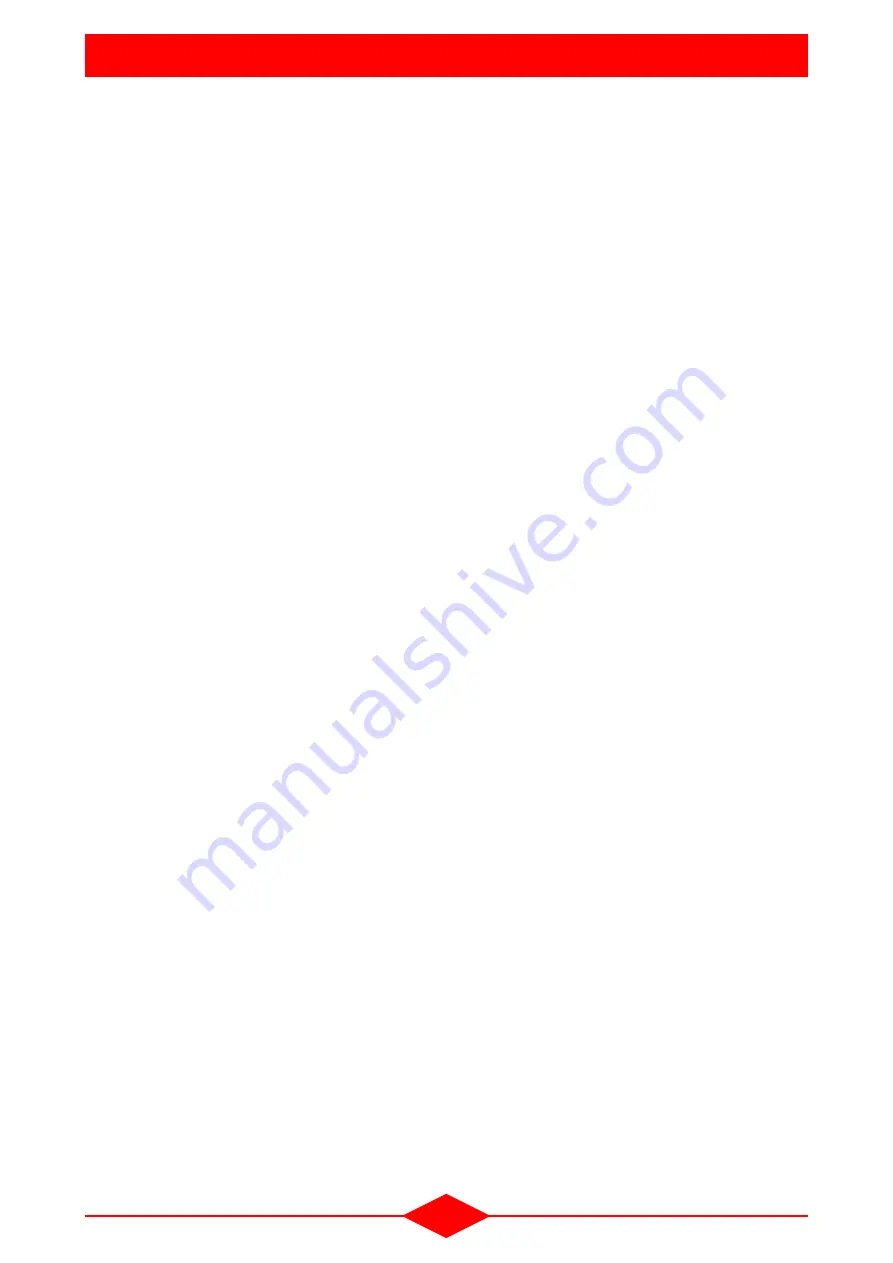
- 2 -
CONTENT
- GAS/CO2/CO/NOX FLOW CONTROL AND SERVICE PRESSURE CONTROL ............................... 10
2.1 - Surveillance procedure ............................................................................................................ 11
2.2 - Setting table ............................................................................................................................. 12
2.1 - Maintenance alarm .................................................................................................................. 19
2.2 - Maintenance code ................................................................................................................... 19
2.3 - Coding of maintenance alarms ................................................................................................ 19
2.4 - General activation of maintenance alarms .............................................................................. 19
2.5 - Activation of the individual maintenance alarm ....................................................................... 20
2.6 - Acknowledgement of maintenance alarms .............................................................................. 20
2.7 - Resetting the maintenance alarms .......................................................................................... 20
Summary of Contents for THI 10-35 SEP
Page 27: ...27 VI PARTS LISTS THI 10 50 C...
Page 30: ...30 PARTS LISTS THI 10 35 SEP...
Page 33: ...33 PARTS LISTS CONTROL BOX...