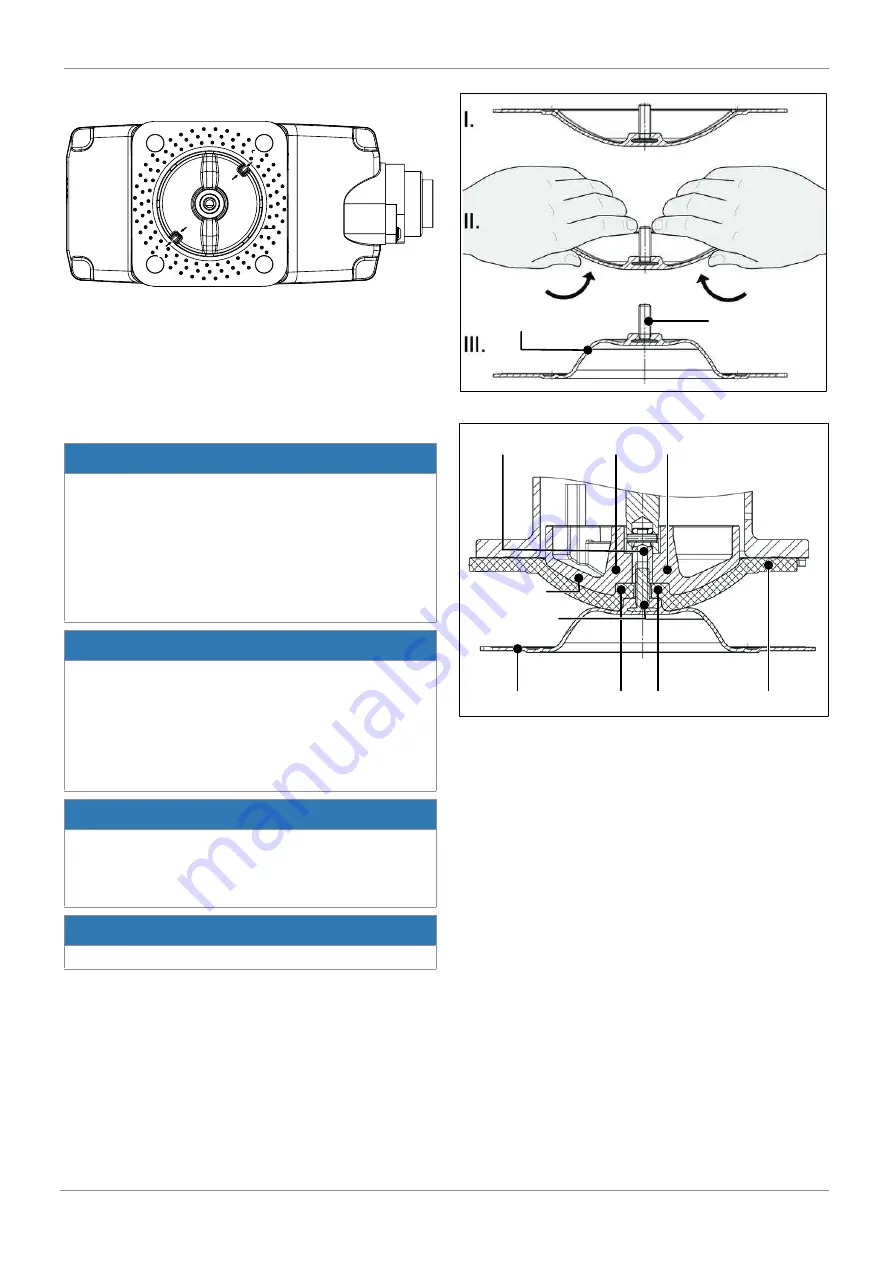
www.gemu-group.com
36 / 41
GEMÜ 629 eSyLite
14 Inspection and maintenance
14.4 Mounting the compressor
D
D
C
C
1. Place the compressor loosely on the actuator spindle.
2. Fit recesses
D
into guides
C
.
ð
The compressor must be able to be moved freely between
the guides.
14.5 Mounting the diaphragm
14.5.1 Mounting the convex diaphragm
NOTICE
▶
Fit the diaphragms suitable for the product (suitable for
medium, medium concentration, temperature and pres-
sure). The diaphragm is a wearing part. Check the tech-
nical condition and function of the product before com-
missioning and during the whole term of use. Carry out
checks regularly and determine the check intervals in ac-
cordance with the conditions of use and/or the regulatory
codes and provisions applicable for this application.
NOTICE
▶
If the diaphragm is not screwed into the adapter far
enough, the closing force is transmitted directly onto the
diaphragm pin and not via the compressor. This will
cause damage and early failure of the diaphragm and
leakage of the product. If the diaphragm is screwed in too
far, perfect sealing at the valve seat will not be achieved.
The function of the product is no longer ensured.
NOTICE
▶
Incorrectly mounted diaphragms cause the product leak-
age and emission of medium. In this case, remove the
diaphragms, check the complete valve and diaphragms
and reassemble again proceeding as described above.
NOTICE
▶
The compressor is loose and can fall out.
Diaphragm pin
Diaphragm face
Fig. 6: Inverting the diaphragm face
Compressor
Backing diaphragm
Diaphragm face
Diaphragm boss
Diaphragm pin
Adapter
Recess of compressor
Fig. 7: Screwing in the diaphragm face
1. Move the actuator
A
to the closed position.
2. Mount the compressor (see "Mounting the compressor").
3. Check if the compressor is fitted in the guides.
4. Invert the new diaphragm face manually (use a clean, pad-
ded mat with larger nominal sizes).
5. Position the new backing diaphragm onto the compressor.
6. Position the diaphragm face onto the backing diaphragm.
7. Screw diaphragm face tightly into the compressor manu-
ally.
ð
The diaphragm boss must fit closely in the recess of
the compressor.
8. If it is difficult to screw it in, check the thread and replace
damaged parts.
9. When definitive resistance is felt, turn back the diaphragm
until its bolt holes are in correct alignment with the bolt
holes of the actuator.
10. Press the diaphragm face tightly onto the backing dia-
phragm manually so that it returns to its original shape
and fits closely on the backing diaphragm.
11. Align the weir of compressor and diaphragm in parallel.