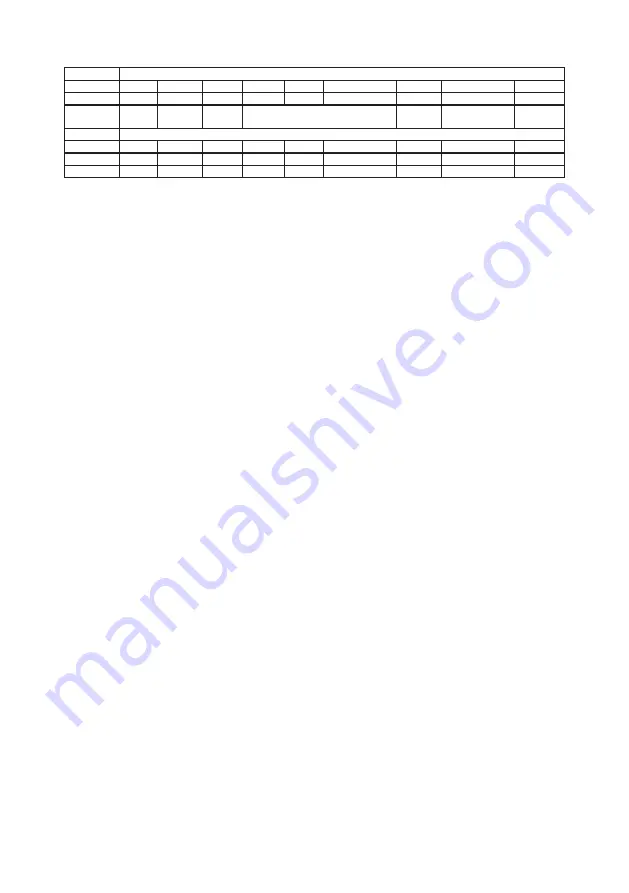
15
———— Absolute encoder interface ————
Connector
Pin
1
2
3
4
5
6
7
8
9
Signal
CLK+2
CLK-2
DTA+2
DTA-2
EQP (1)
Description
Clock +
Clock-
Datum +
Datum -
Equipotentiality
Reserved
Connector
PIN
1
2
3
4
5
6
Signal
CKL+2
CLK-2
DTA-2
DTA+2
EQP (1)
Description
Clock + Reserved
Clock-
Datum-
Datum + Equipotentiality
teabs02g
9-female pole D-sub connector of the wire
Reserved
X3 (internal connection)
(
1
) The EQP equipotentiality signal is internally connected to 0V via a 120-Ohm resistance.
The equipotentiality is used if the encoder power supply does not come from the drive XE
connector. It has to be performed in order to avoid that the power supply reference potential
exceeds the maximum value allowed by the drivers type 485 on the E-ABS card and on the
encoder. The equipotentiality can be obtained by connecting the 0V of the encoder power
supply to the pin number 8 of the 9-female pole D-sub connector.
This connector is not supplied with the cable braided wire connection. For this reason the braided
wire connections have to be performed on the terminals of the application card.
If the cable braided wire on the encoder side is ground connected, it is necessary to connect it
to the terminal 3 in order not to create any loop.
If the cable braided wire on the encoder side is not ground connected, it is preferable to connect
it to the terminal 6.
Refer to the example diagrams in chapter 8, Use Examples.
3.4 Second Encoder Connection
The 9-pole connector for the second encoder is connected to the E-ABS card via a flat cable
placed in the optional kit. Considering the connection mode, a mechanical fixing of the encoder
connector is required (for example with a clip on the drive openings) in order not to pull out the
flat cable from the E-ABS connector.
4. Power Supply
The card requires the digital power supply (0V, +5V) deriving from the application card. The
encoder is externally power supplied.
4.1 Encoder Power Supply through the Drive
This is the most common situation, as the foreseen encoder (see chapter 7, Technical Features)
has, together with the absolute section, also an incremental section. The information deriving
from the incremental section are used to feedback the drive control; as a consequence this
encoder is connected to the drive XE connector like a normal incremental encoder. Also the
encoder power supply derives from the XE connector. Such voltage has to be adjusted by
acting on the suitable drive parameter in order to compensate the voltage drop on the cable.
Refer to the example diagrams in chapter 8, Use Examples.
4.2 Encoder External Power Supply
If the encoder power supply derives from a different power pack, it is necessary to perform the
equipotentiality connection as the 0V of this power pack could be separated from the drive 0V.
As a consequence the procedure to be followed is the one described in the paragraph 3.2, First