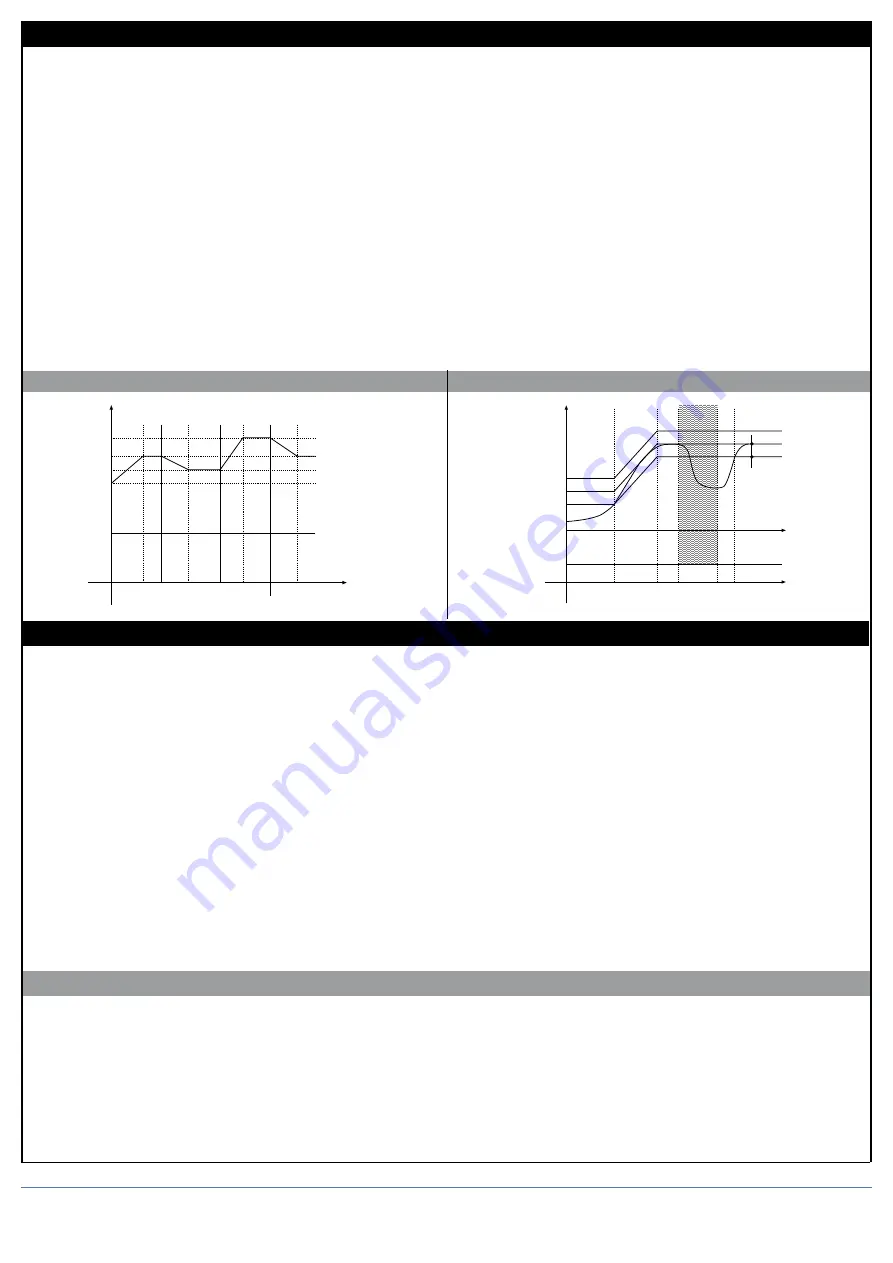
Programmer functions
7 • USING THE PROGRAMMER
There are up to 12 (16*) steps arrangeable in 4 programs. A program step contains the ramp and the hold time. Ramp times and hold times are programmable with a time base
selected as 99h59m or 99m59s. Time base accuracy is greater than 4 secs every 10 hours.
Program selection from faceplate, digital input or serial line.
Program control from keys, digital inputs (START/STOP, RESET, end of program), serial line or events AL1/AL2/AL3.
Program stopping and restarting modes:
- from digital input; from “Raise” (START) key, “Lower” (STOP) key or “M/A” (RESET) key in absence of other enablings
- from state of alarms (ON = START)
- different modes of restarting after a power failure
• from setpoint prior to power failure
• from value of process variable at power-up
• with search for best setpoint forward/backward in time
• awaiting a start
In the STOP phase, it is possible to change:
- current setpoint
- current step time
- program number
- step number
- phase or segment (ramp or hold)
The clearance input and event outputs assigned to an individual step. Programmed input conditions are scanned at the beginning of every step.
If satisfied, execution begins with updating of assigned outputs and restart of time base.
Indication of end of program, with or without forcing of control output.
Setting a tolerance band for setpoint: if the process variable is outside the band, the time base stops (Hbb - Hold back band alarm).
Secondary setpoint with the same time base to manage a slave controller using retransmission output W1 or W2.
Full functional modularity, with easy exclusion of functions not needed. Up to 4 parameter groups to control and limit power, selectable by single segment (ramp and/or hold).
Function Hbb example (holding band)
Program example
6 • PROGRAMMER
The unit combines the functions of a single loop controller and programmer.
The programmer function lets you run a program as a series of steps, each of which has two segments:
√
a ramp
√
a hold.
Every step has its associated data:
• SPs: a setpoint value
• rPt: ramp time from 0.0 to 99h59m (time base in h. m.) or 99m59s (time base in m. s.); set a time that gives a faster or slower variation depending on the
initial value and on the final setpoint.
• Sot: hold time from 0.0 to 99h59m (time base in h. m.) or 99m59s (time base in m. s.).
• Hbb: tolerance band, symmetrically positioned above and below the setpoint, and referenced to the main input or the auxiliary input.
• Eur: outputs 1...4; combination codes for outputs (0-15) programmable for the ramp phase.
• EuS: outputs 1...4; combination codes for outputs (0-15) programmable for the hold phase.
• iPt: active inputs (ON) as clearance for execution.
• SLS: slave setpoint to transmit to a slave controller with the same time base.
• GrP: parameter groups to control and limit power (up to 4), selectable by single segment.
There are 12 (16*) program steps available that can make up a maximum of 4 programs.
Examples of arrangements:
2 program of 8 and 4 steps; 4 programs of 3 steps; 2 programs of 6 steps; etc...
It is important to remember that the parameter Sty defines enabling of Hbb (on the ramp, in hold, or both) and the reference value (PV or aux input).
(*) Alternative to custom linearization function (see parameter SP.Pr, Hrd menu).
Temperature
Step 5
Step 6
Step 7
Step 5
I° CYCLE
II° CYCLE
tr5
tp5
tr6
tp6
tr7
tp7
tr5
tp5
Start
SP06
SP05
SP07
Time
t
off
t
on
t
t
Temperature
Program recovery
S.P.
Ti
tw1
tr
tp1
tw2 tp2
tp = tp1 + tp2
Hbb
Power
Off
Time
tw = waiting time
tr = ramp time
tp = hold time
Variation of the local setpoint when the program is stopped will restart the current step, keeping the same ramp time.
If the unit is switched off and then switched on, the program can continue or can start again at the first step.
Or it can search for the step that has the setpoint closest to the PV (see Pty parameter in ProG configuration to define restart conditions).
STOP/START switching at end of program resets and restarts the program.
Fast simulation of program:
A selected program can easily be checked by running it in fast simulation mode.
To do this, set code Pty +64 in the ProG menu.
The program runs with the ramp and hold times limited to 20 and 10 seconds, respectively. Lower values entered are accepted.
10
80090G_MHW_1600-1800P_04-2013_ENG