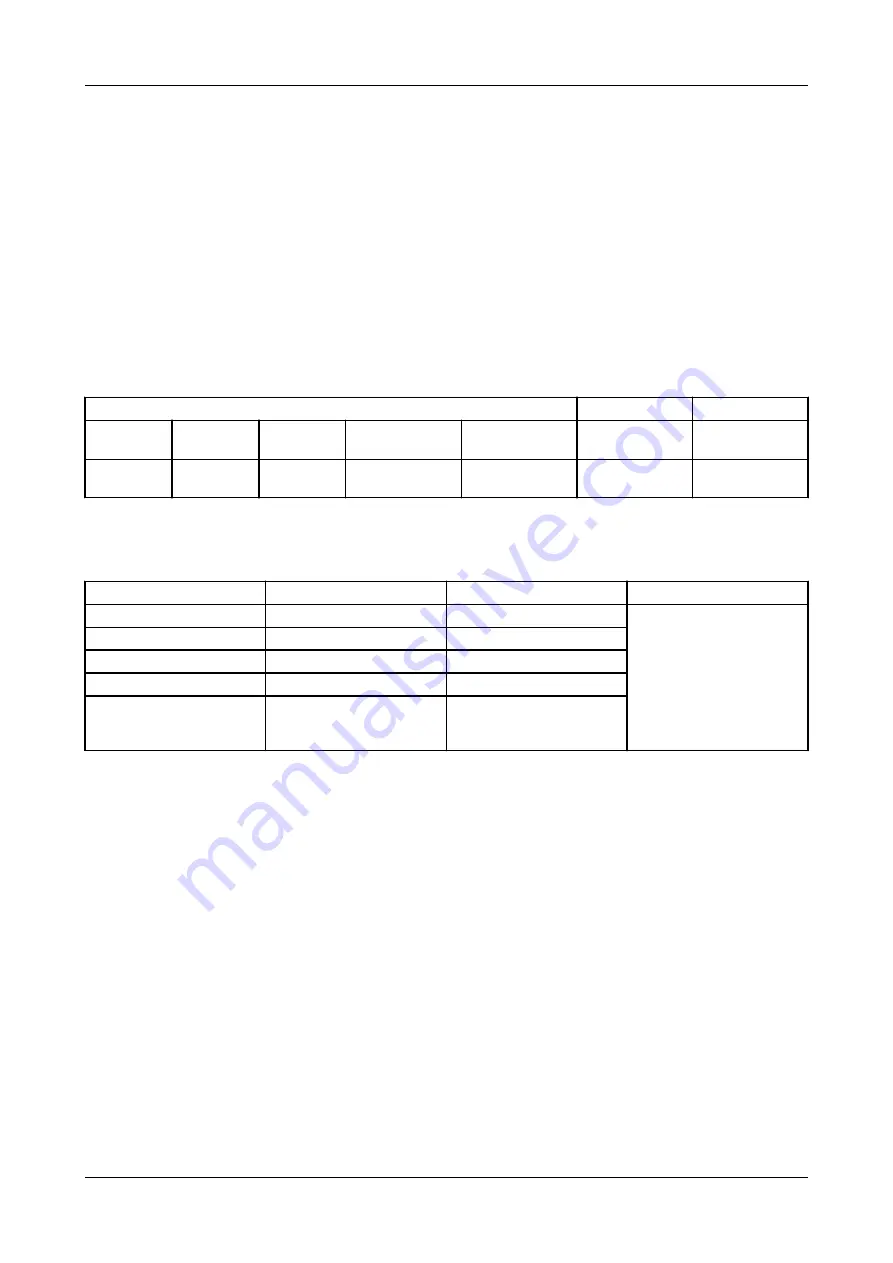
9.1.3
Cleaning the leakage cavity
To clean the leakage cavity, two flush valves are fitted in the seat area of the
double-seal valve C. Cleaning liquid is flushed into the leakage cavity through
one of the flush valves. The cleaning medium is discharged via the second flush
valve. This valve is also used for leakage detection in the event of seal damage.
If valve C is only equipped with a flush valve, this is only for leakage detection
and discharge. In this case, the leakage cavity cannot be cleaned separately.
The recommended admission pressure for the cleaning medium supply at the
inlet valve to the leakage cavity is 2.5 bar ± 0.5 bar. Pressure build-up between
the seals on the valve disc should always be avoided. Non-pressurised
discharging at the outlet valve is therefore required. The duration of the flushing
operation via the flush valve depends on the type of soiling and typically ranges
between 10 and 90 seconds.
Flow rates for cleaning the leakage cavity
Nominal
width
DN25
1"
DN40, DN50
1.5", 2"
DN 65, DN80
2.5", 3"
DN100
4"
DN125
DN150
6"
Kvs values
(l/h)
127
453
486
486
1490
1490
9.1.4
Rinsing operations
The table lists the values for the duration and number of rinsing operations.
Medium
Duration [s]
Number of rinsing operations
Beer
1...2
2...3
During every cleaning phase:
1.
Prerinse
2.
Hot caustic
3.
Intermediate rinse
4.
Acid
5.
Rinsing
Yeast
1...2
2...3
Fruit juices
2...6
3
Milk
2…5
3
Yoghurt
3…5
3
Depending on the cleaning method (medium, concentration, temperature and
contact times), the seals are affected to different degrees. This can impair the
function and the service life.
9.2
Passivation
Before commissioning a plant, passivation is usually carried out for long pipes
and tanks.
Valve blocks are usually excepted from this. Passivation is typically performed
using nitric acid (HNO
3
) at approx. 80 °C (176 °F) at a concentration of 3 % and a
contact time of 6 to 8 hours.
Cleaning
Passivation
430BAL008331EN_4
18.02.2022
39