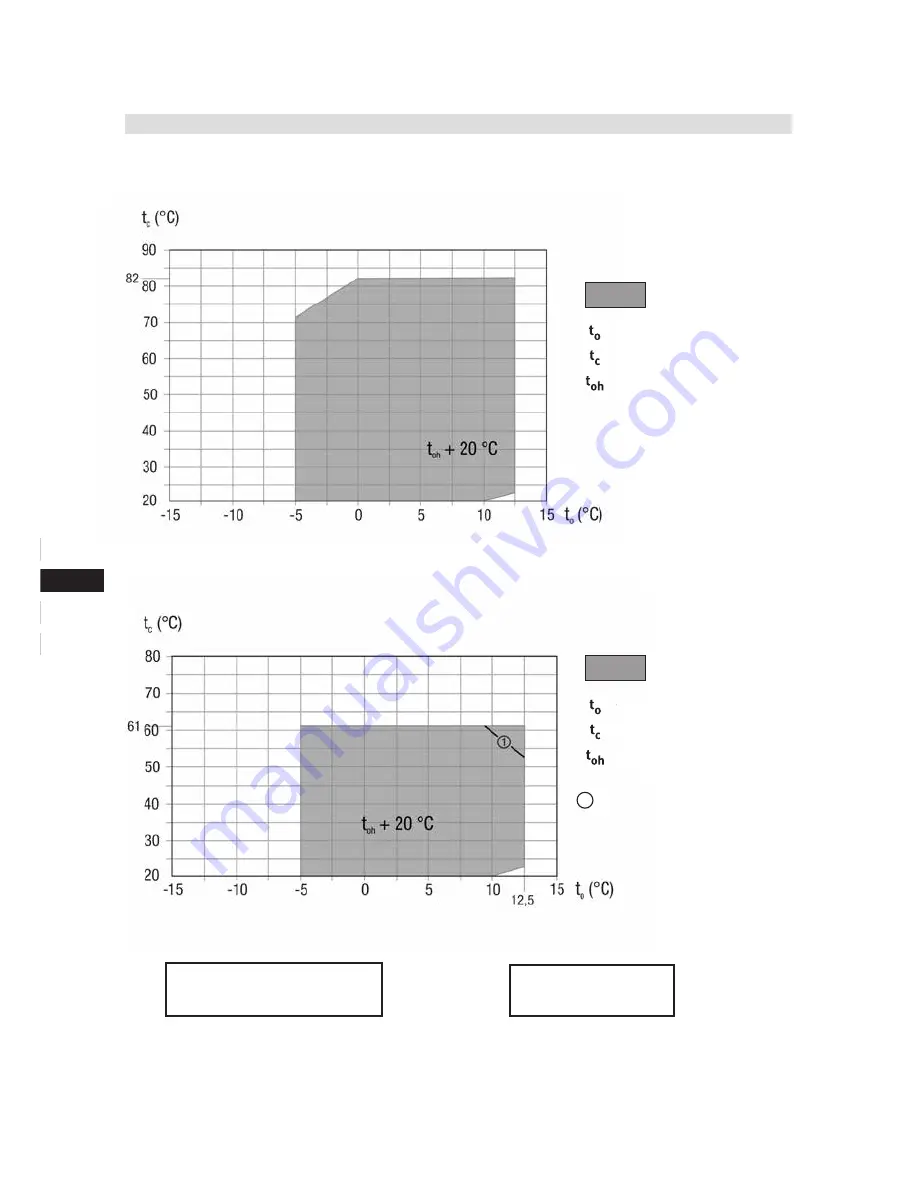
10
D
GB
F
E
96116-01.2016-DGbFE
3
|
Areas of application
3.4 Limits of application K Design (60 Hz)
• HFKW / HFC:
R134a, R407C
Fig. 7
Fig. 8
R134a
60 Hz
R407C
60 Hz
1
HGX34P/380-2 (A) K
observe the operating limits
Design for other
ranges on request
Unrestricted
application range
Evaporating temperature (°C)
Condensing temperature (°C)
Suction gas temperature (°C)
Unrestricted
application range
Evaporating temperature (°C)
Condensing temperature (°C)
Suction gas temperature (°C)
Max. permissible operating
pressure (LP/HP)
1)
: 19/28 bar
1)
LP = Low pressure
HP = High pressure